Manufacturing Blog: Engineers Needed to Fill AI Tool Gaps
Manufacturing Blog: Engineers Needed to Fill AI Tool Gaps
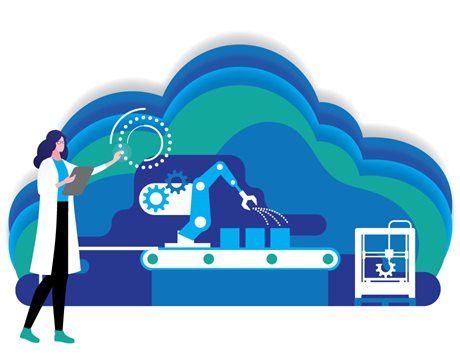
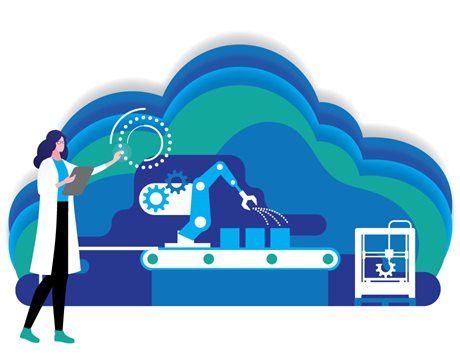
It takes human and artificial intelligence to make generative design and topology optimization work.
Imagine the day when AI engineering tools design fully optimized parts ready for immediate production through additive manufacturing (AM). For some, this would be a dream come true, and for others, a nightmare that threatens their livelihoods.
Well, there is excellent news for both camps. Yes, algorithms will increasingly shoulder the burden of design, but it will take talented designers and engineers to make it happen today and for quite a while into the future.
That is certainly the case when people talk about generative design and topology optimization, two AI engineering tools increasingly used in design and manufacturing. Both rely on simulation, but they are two distinct processes that produce very different results.
The future of generative design and topology optimization is clear: these tools will improve over time and become the norm for designers and engineers. Those who are already working with these tools believe that now is the time to begin the journey of exploration and learning.
Generative design starts with a blank slate. Engineers enter an array of pre-defined goals, constraints, and parameters and the software produces a set of design possibilities. Essentially, generative design is a concept generator. The engineering team then selects the best candidates and continues the design and optimization process.
Read Our Latest Blog: Generative Design and Engineering Jobs
Topology optimization, on the other hand, starts with an existing design created either traditionally or generatively. It then modifies it to create a structure optimized for performance, cost, or production time. As with generative design, engineers use their expertise to define the performance thresholds.
The two tools have a lot in common. In their current states, neither of them is a one-step, fully automated design creator. Both require human intervention to create designs that are ready for manufacturing.
On the front end, we need skilled, savvy engineering teams to define the appropriate inputs, or we wind up in a “garbage in, garbage out” situation.
On the back end, professionals must massage, analyze, interpret, revise, and repurpose the configurations produced by generative design and topology optimization. This takes engineering expertise plus a variety of CAD, CAE, and related software packages to get the job done.
Opinions vary about the capability of these tools. In their present state, their power and sophistication often depend on the user’s objectives.
For engineers tackling a single part with one static loading condition, the tools do their jobs well, though the workflow is a bit kludgy. On the other hand, someone working at a systems level with multi-physics, dynamic conditions will likely argue that more development is needed.
So, where do you fit in? The journey starts with AI tools, but to really put it to work for your specific tasks, you will need to understand today’s workflows and the human skills needed to harness their power.
Regardless of the project and the AI tool, you will need additional CAD/PLM work. At the design level, for example, you may need to add such features as mounting bosses to generative designs and smooth topology-optimized features.
You May Also Like: How Industry 4.0 Impacts Engineering Design
For design and product management, engineers will need to craft editable parametric models using AI output as a reference.
For CAD/PLM operations, you must evaluate the degree to which you can use AI output in your software package. Sometimes, they plug right in. In a worst-case scenario, however, you would have to use the AI design as a reference model and rebuild your design from scratch.
You will also need to review manufacturability and make modifications as needed. The output of these tools is not inherently printable with additive manufacturing.
Also, you will need to conduct more thorough, second-level analyses of your designs. There are a vast number of additive processes, materials, and printing parameters available. Their combinations yield strikingly different mechanical properties that have not been fully documented. As a result, the simulations used for both generative design and topology optimization will be approximations of the actual results.
Those with higher-level demands will want to investigate the methodology to achieve system-level or multi-physics AI design. While some packages are better than others, it is still early days for these concepts.
The complex interactions between components in a system (sub-assembly) are typically beyond the current capabilities of generative design and topology optimization. These tools are not capable of addressing dynamic loading, nor are they capable of considering multiple mechanical, thermal, and flow characteristics simultaneously.
As you embark on your journey, evaluate these operations—and others—to understand the tools you need—and also the human interactions and the workflow.
AI-driven design will change how we approach design and engineering, but it will not eliminate the need for trained professionals. It will, however, alter the skillsets engineers need in the future.
For those looking for new challenges—and for those who want to lead the way—the time is now to begin the journey. These tools need human intervention at all stages of the design process. They need smart, experienced people to make them work. Today, there is only a tiny pool of engineers who have that expertise.
Editors' Pick: Should You Design for Additive Manufacturing?
For those in management roles, begin to build your generative design and topology optimization teams. This will enable you to take advantage of what these tools now offer and prepare for what is to come. And once you have the talent, do everything in your power to keep them, because these skills are going to be in high demand and there are not enough engineers to satisfy the need.
Todd Grimm is president of T. A. Grimm & Associates, an additive manufacturing consulting and communications company, and a 30-year industry veteran.
Well, there is excellent news for both camps. Yes, algorithms will increasingly shoulder the burden of design, but it will take talented designers and engineers to make it happen today and for quite a while into the future.
That is certainly the case when people talk about generative design and topology optimization, two AI engineering tools increasingly used in design and manufacturing. Both rely on simulation, but they are two distinct processes that produce very different results.
The future of generative design and topology optimization is clear: these tools will improve over time and become the norm for designers and engineers. Those who are already working with these tools believe that now is the time to begin the journey of exploration and learning.
AI Tools
Generative design starts with a blank slate. Engineers enter an array of pre-defined goals, constraints, and parameters and the software produces a set of design possibilities. Essentially, generative design is a concept generator. The engineering team then selects the best candidates and continues the design and optimization process.
Read Our Latest Blog: Generative Design and Engineering Jobs
Topology optimization, on the other hand, starts with an existing design created either traditionally or generatively. It then modifies it to create a structure optimized for performance, cost, or production time. As with generative design, engineers use their expertise to define the performance thresholds.
The two tools have a lot in common. In their current states, neither of them is a one-step, fully automated design creator. Both require human intervention to create designs that are ready for manufacturing.
On the front end, we need skilled, savvy engineering teams to define the appropriate inputs, or we wind up in a “garbage in, garbage out” situation.
On the back end, professionals must massage, analyze, interpret, revise, and repurpose the configurations produced by generative design and topology optimization. This takes engineering expertise plus a variety of CAD, CAE, and related software packages to get the job done.
Opinions vary about the capability of these tools. In their present state, their power and sophistication often depend on the user’s objectives.
For engineers tackling a single part with one static loading condition, the tools do their jobs well, though the workflow is a bit kludgy. On the other hand, someone working at a systems level with multi-physics, dynamic conditions will likely argue that more development is needed.
Considerations
So, where do you fit in? The journey starts with AI tools, but to really put it to work for your specific tasks, you will need to understand today’s workflows and the human skills needed to harness their power.
Regardless of the project and the AI tool, you will need additional CAD/PLM work. At the design level, for example, you may need to add such features as mounting bosses to generative designs and smooth topology-optimized features.
You May Also Like: How Industry 4.0 Impacts Engineering Design
For design and product management, engineers will need to craft editable parametric models using AI output as a reference.
For CAD/PLM operations, you must evaluate the degree to which you can use AI output in your software package. Sometimes, they plug right in. In a worst-case scenario, however, you would have to use the AI design as a reference model and rebuild your design from scratch.
You will also need to review manufacturability and make modifications as needed. The output of these tools is not inherently printable with additive manufacturing.
Also, you will need to conduct more thorough, second-level analyses of your designs. There are a vast number of additive processes, materials, and printing parameters available. Their combinations yield strikingly different mechanical properties that have not been fully documented. As a result, the simulations used for both generative design and topology optimization will be approximations of the actual results.
Those with higher-level demands will want to investigate the methodology to achieve system-level or multi-physics AI design. While some packages are better than others, it is still early days for these concepts.
The complex interactions between components in a system (sub-assembly) are typically beyond the current capabilities of generative design and topology optimization. These tools are not capable of addressing dynamic loading, nor are they capable of considering multiple mechanical, thermal, and flow characteristics simultaneously.
As you embark on your journey, evaluate these operations—and others—to understand the tools you need—and also the human interactions and the workflow.
Your Future
AI-driven design will change how we approach design and engineering, but it will not eliminate the need for trained professionals. It will, however, alter the skillsets engineers need in the future.
For those looking for new challenges—and for those who want to lead the way—the time is now to begin the journey. These tools need human intervention at all stages of the design process. They need smart, experienced people to make them work. Today, there is only a tiny pool of engineers who have that expertise.
Editors' Pick: Should You Design for Additive Manufacturing?
For those in management roles, begin to build your generative design and topology optimization teams. This will enable you to take advantage of what these tools now offer and prepare for what is to come. And once you have the talent, do everything in your power to keep them, because these skills are going to be in high demand and there are not enough engineers to satisfy the need.
Todd Grimm is president of T. A. Grimm & Associates, an additive manufacturing consulting and communications company, and a 30-year industry veteran.
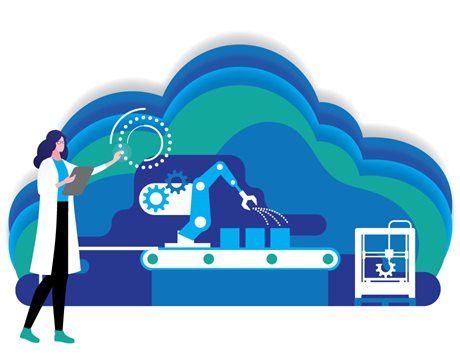
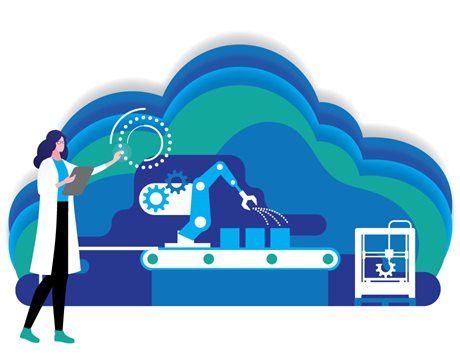