Lightweight Metal Composite Floats on Water
Lightweight Metal Composite Floats on Water
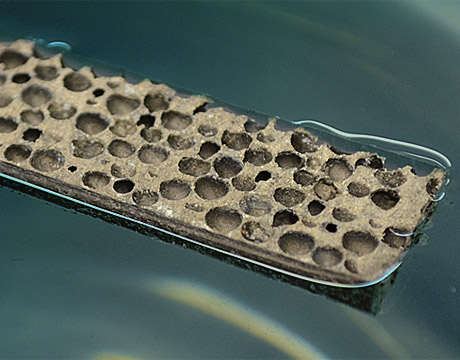
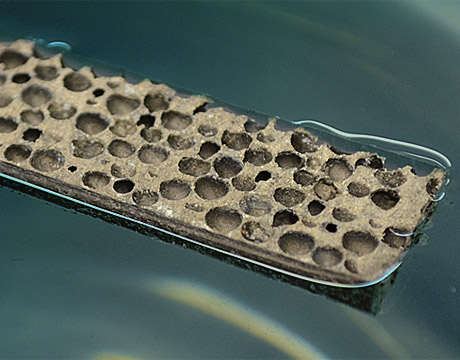
Metal composite light enough to float on water. Image: Nikhil Gupta / NYU Polytechnic School of Engineering
Lightweight polymer matrix composites are increasingly being used to replace metal-based materials to reduce weight in manufactured products, especially automobiles and aircraft. However, most polymer matrix composites can only tolerate temperatures of 150°C or less, making them unsuitable for engine and exhaust components.
Now, however, a magnesium-matrix composite invented by researchers at New York University Polytechnic School of Engineering, in collaboration with Deep Springs Technology and the Army Research Laboratory, may reverse this trend back toward metal composites. The new material is remarkable in several ways—not only it is light enough to float on water, it is as strong as other composite materials being used today and can withstand temperatures over 400°C.
Silicon Carbide Makes the Difference
Led by Nikhil Gupta, associate professor of mechanical and aerospace engineering at New York University Polytechnic School of Engineering in Brooklyn, a research team from his department and from Deep Springs Technology developed the new material from a magnesium alloy matrix known as AZ91D, a cast magnesium alloy containing 9 weight percent aluminum, 1 weight percent zinc, 0.3 weight percent manganese.
Magnesium alloys show tremendous potential for weight-sensitive applications, especially in the automotive, aerospace, defense, and electronics industries. Although magnesium is a promising low-density metal, years ago there were initial concerns about flammability and processing issues. However, new magnesium alloys and processing methods have solved these issues.
The density of the new magnesium-matrix composite material is only 0.92 grams per cubic centimeter, compared to the density of water at 1.0 g/cc—meaning it will float on water.
“Tests on its high-temperature properties show that the mechanical properties are retained up to about 400°C,” states Gupta. “In addition, the compressive strength at low and high strain rate is found to be comparable to other existing aluminum and magnesium matrix composites that have densities in the range 1.2 to 1.5 g/cc.”
The secret to this strength are the hollow silicon carbide particles that were developed and manufactured by DST. The exterior shell of a single particle can withstand pressure exceeding 25,000 pounds per square inch before it ruptures—one hundred times the maximum pressure in a fire hose. The hollow particles also provide impact protection because each shell (if it fails) absorbs some of the energy of the impact.
“One of the greatest challenges was determining the optimum concentration of particles,” says Gupta. “Particles that were mixed in high-volume fractions in the matrix tended to break, resulting in a higher-than-expected density. On the other hand, the fewer the particles used, the greater the density of the material.”
The composite can be customized for density and other properties by adding more or fewer shells into the metal matrix to fit the requirements of the application.
Future Applications
This new magnesium-matrix composite material is strong, heat resistant, and lighter than water. For example, a boat made from this material would not sink, even if its structure was damaged.
“This is the first time anybody has been able to achieve such a low density in metal matrix composite material,” says Gupta. It is also strong enough to withstand harsh operational environments, making it attractive for boat flooring, automobile parts, buoyancy modules, and defense applications, such as vehicle armor.
Gupta’s new composite material could be ready for prototype testing in as little as three years. Finding applications for military vehicles is a top priority. For example, newer or experimental platforms such as Ultra Heavy-Lift Amphibious Connector (UHAC) may especially benefit from metallic lightweight materials. However, notes Gupta, there is still a lot of research that needs to be done, including determining appropriate heat treatments to further enhance the mechanical properties, experimenting with different particle types in the composite, and determining corrosion resistance.
“Although important, density is only a small part of a large set of properties that determine applicability of a material in any industrial applications,” says Gupta. “Strength, ductility, modulus, corrosion resistance and many other properties may be relevant to the actual application. We will strive to also push boundaries forward on as many of these properties as possible.”
Mark Crawford is an independent writer.
This is the first time anybody has been able to achieve such a low density in a metal matrix composite material. Prof. Nikhil Gupta, NYU Polytechnic School of Engineering
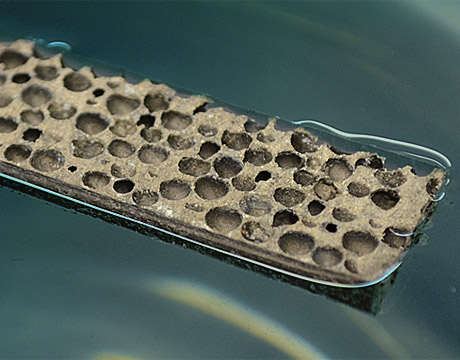
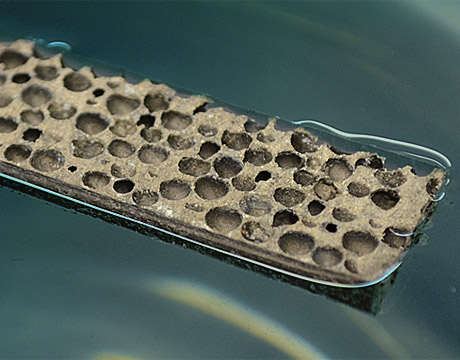