Inspiration from the Trees
Inspiration from the Trees
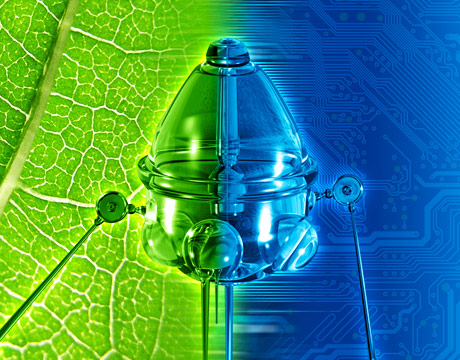
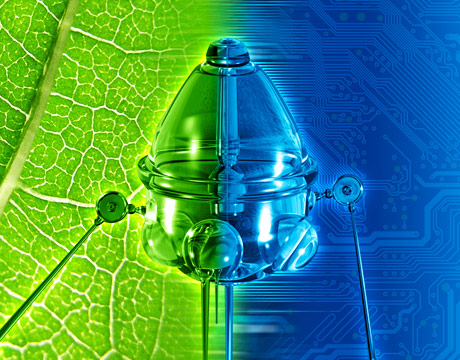
Cost is often a reality when creating robotics. Peko Hosoi, professor of mechanical engineering at MIT, and her team knew this well and recently asked: Could scaling down reduce costs for small robots?
“It’s tough for a lot of robotics because of the need for valves and pumps. They need tighter and tighter parts that have to machine down and they become expensive,” she says. “To get a servo valve that was a cubic centimeter can be unbelievably expensive per valve. That’s not even for nano. Can we rethink systems to where places in nature and systems add up together to small, cheap components?”
Her team decided trees and plants provided a potential answer because they have small components that create a giant pump when combined together, she says. The team went to work on what would eventually lead to a microfluidic pump to aid small robotics, called a “tree on a chip,” with the idea, among other things, of an external pump not being necessary.
With trees, there is a sugar channel and water channel and water flows into the sugar channel and drives the flow, she says, but, when it’s done quickly, it is not ideal for robotics. “Our challenge was how to have pumping at a constant flow rate,” she says. “Trees have this kind of gas tank and the leaves are photosynthesizing and producing sugars. So you need to have that kind of tank that couples with the phloem, which is the sugar-water piece, which is then in contact with xylem. It’s adding a third piece—not just sugar and water, but also needing a source that is metered into the sugar-water channel.”
They ran the system with dextran—literally a little reservoir of it—and separated that from the sugar water channel with a membrane that allows dextran molecules to pass through at a steady rate, Hosoi says.
“We also ran it with a sugar cube. We laser cut a couple pieces of acrylic and we laser cut a little slot for the sugar cube and slot it in,” she explains. “And the sugar cube just goes for weeks.”
They were also looking at the measure of flow rate. “It’s about questions like what kinds of pressures can this generate and flow rates can it generate?” she says. “The measurement is pretty simple. You have the pump and attach it to a long, thin capillary and the fluid starts to move down the capillary and you track the interface of the fluid as it moves down the capillary. It tells you what the flow rate is. We can estimate what kinds of pressures these pumps can generate. We measure flow rates and pressures for different membranes and what the membrane does is it sets the concentration of the sugar in the sugar channel.”
With the real drivers behind the work being an interest in cost savings with natural systems that are good at reaching very complex structures and behaviors in electronics, she says it’s something many in the ME field should consider. “We are good at cheap complexity with the advent of transistors and integrated circuit boards,” she says. “In mechanical, we just have to think more about this.”
Eric Butterman is an independent writer.
Our challenge was how to have pumping at a constant flow rate. Trees have this kind of gas tank and the leaves are photosynthesizing and producing sugars.Prof. Peko Hosoi, MIT
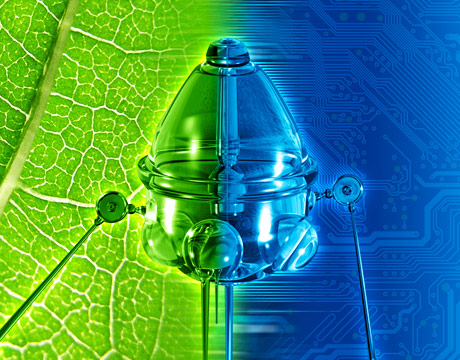
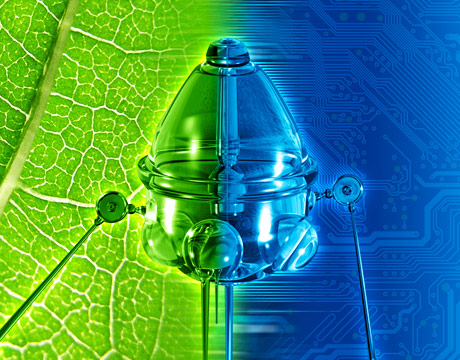