Complex Channels Make for Better Heat Exchange
Complex Channels Make for Better Heat Exchange
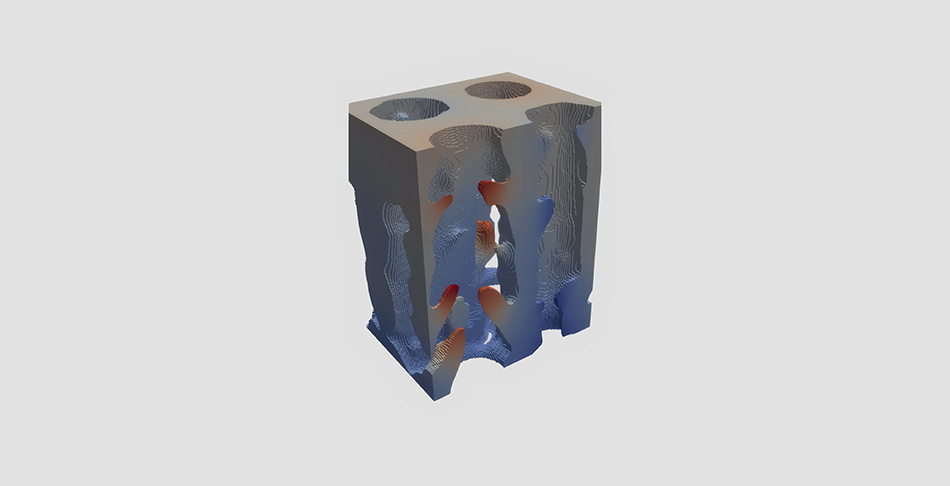
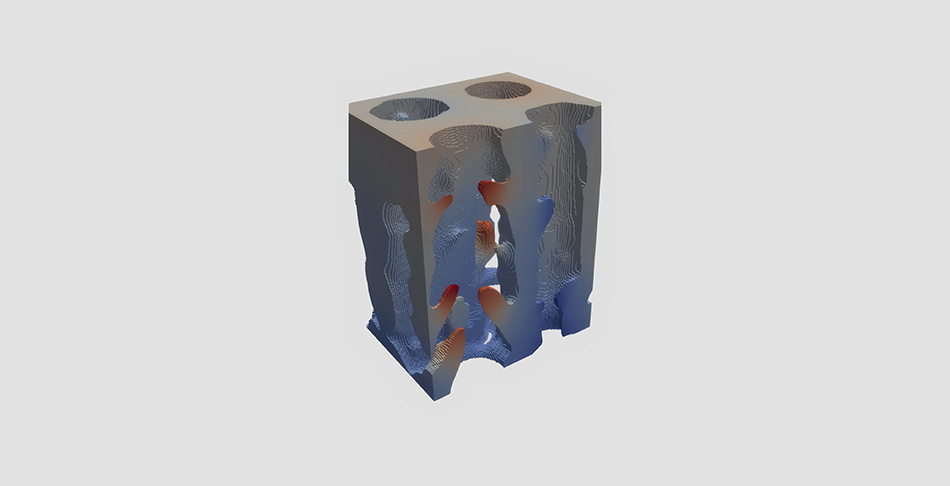
Engineers tested heat exchangers with convoluted flow channels against simpler ones in high-temperature applications. The complex heat exchangers showed a performance improvement of 27 percent.
High-temperature heat exchangers are essential components in many technologies, with critical applications in aerospace, power generation, industrial processes, manufacturing, and aviation. The primary purpose of a heat exchanger is to transfer heat between two fluids. Traditionally, this is done using simple geometries, such as straight cylindrical channels, that are also easy to manufacture and analyze.
However, straight pipes are not always the most efficient way of transferring heat between hot and cold fluids.
With his expertise in topology optimization and additive manufacturing, Xiaoping Qian, a professor of mechanical engineering at the University of Wisconsin-Madison, wanted to see if he could significantly improve heat exchanger performance by rethinking the geometry of the flow channels.
“Heat transfer efficiency is strongly influenced by the shape and structure of these channels,” Qian said. “Topology optimization—a computational method for distributing material optimally within a design space—can be used to create flow geometries that enhance heat transfer. At the same time, additive manufacturing [AM] offers the freedom to fabricate these complex, optimized designs. Unlike traditional methods, it allows for intricate shapes at no additional cost in complexity.”
By combining topology optimization and additive manufacturing, Qian believed he could design and produce heat exchangers with highly efficient, customized flow paths—maximizing thermal performance while maintaining manufacturability.
Designing complex 3D flow paths required solving the governing equations for fluid flow and heat transfer in three dimensions—an extremely computationally intensive task.
“During topology optimization, these equations must be solved repeatedly across many iterations, which can take several days even on high-performance computing systems with hundreds of CPUs,” Qian said.
In heat exchanger design, it is commonly assumed that increasing the contact area between a solid wall and a fluid improves heat transfer. However, Qian’s results showed that this is not always the case. While contact area plays a role, the behavior of fluid flow—strongly influenced by channel geometry—can be even more critical. “Optimized designs may feature smaller surface areas, yet outperform traditional ones because the flow is structured to enhance heat transfer more effectively under constraints like pressure drop,” he said. “This highlights the importance of considering both flow dynamics and geometry, rather than relying solely on maximizing surface area.”
After determining the best optimized design, Qian partnered with Dan Thoma, a professor of materials science and engineering at UW, to 3D-print the heat exchanger using a metal AM technique called laser powder bed fusion. The most efficient heat exchanger designs often involve intricate and twisted flow channels. AM techniques such as laser powder bed fusion can build components by selectively melting metal powders to form solid walls.
“However, in complex geometries, loose powder can become trapped in internal flow paths, making post-processing and powder removal difficult,” Qian said. “Ensuring that the optimized structures are both manufacturable and cleanable poses a significant challenge in translating high-performance designs into practical, functional components.”
Qian’s team built two full-size heat exchangers with different core designs—one traditional and one optimized—that were experimentally tested under high-temperature conditions. The core of the optimized heat exchanger was comprised of topologically optimized unit cells. Mark Anderson, a professor of mechanical engineering at UW, conducted thermal-hydraulic tests on these two heat exchangers. The topology-optimized heat exchanger outperformed the straight-channel heat exchanger in the categories of heat transfer, power density, and effectiveness, achieving 27.6 percent higher gravimetric power density than the straight channel heat exchanger. The higher power density enables the heat exchanger to be lighter and more compact—useful attributes for aerospace and aviation applications.
“Our approach breaks from this convention,” Qian said. “We use topology optimization, a computational design method that derives geometry directly from the governing physics of fluid flow and heat transfer—without making assumptions about the shape of flow channels. This dramatically expands the design space and enables the discovery of high-performance heat exchanger configurations that would be difficult, if not impossible, to conceive through intuition alone.”
An especially novel aspect of this research is the integration of manufacturability constraints into the design process. “Our formulation incorporates limits on wall thickness, minimum channel width, overhang angles, and powder removal requirements—all critical for additive manufacturing,” Qian said. “By embedding these constraints into the optimization, we ensure that the resulting complex, high-efficiency designs are not only theoretically optimal, but also practical to fabricate. Without such considerations, features like twisted flow paths could trap powder or violate the physical limits of AM, making production unfeasible.”
Qian and his team plan to expand their computational design approach to a wide range of real-world heat exchanger applications. These include systems in power generation, chemical processing, nuclear thermal management, automotive and aerospace engineering, and renewable energy technologies—all of which rely on efficient heat exchange between fluids.
Beyond enhancing heat transfer, the integration of topology optimization with AM unlocks powerful opportunities for product innovation across various industries. This approach enables engineers to harness the geometric freedom of 3D printing to boost performance through functionally tailored designs, reduce weight and material usage, and simplify assemblies by consolidating multiple components into single, optimized structures.
“In the long term,” Qian said, “we envision our approach playing a key role in designing next-generation thermal components where efficiency, sustainability, and advanced manufacturing all converge.”
Mark Crawford is a technology writer in Corrales, N.M.
However, straight pipes are not always the most efficient way of transferring heat between hot and cold fluids.
With his expertise in topology optimization and additive manufacturing, Xiaoping Qian, a professor of mechanical engineering at the University of Wisconsin-Madison, wanted to see if he could significantly improve heat exchanger performance by rethinking the geometry of the flow channels.
“Heat transfer efficiency is strongly influenced by the shape and structure of these channels,” Qian said. “Topology optimization—a computational method for distributing material optimally within a design space—can be used to create flow geometries that enhance heat transfer. At the same time, additive manufacturing [AM] offers the freedom to fabricate these complex, optimized designs. Unlike traditional methods, it allows for intricate shapes at no additional cost in complexity.”
By combining topology optimization and additive manufacturing, Qian believed he could design and produce heat exchangers with highly efficient, customized flow paths—maximizing thermal performance while maintaining manufacturability.
3D flow
Qian’s goal was to develop a design for the hot and cold fluid channels inside a heat exchanger that would maximize heat transfer. His aim was to increase a heat exchanger’s efficiency by optimizing the design of its hot and cold fluid channels with intricate geometries and complex surface features.Designing complex 3D flow paths required solving the governing equations for fluid flow and heat transfer in three dimensions—an extremely computationally intensive task.
“During topology optimization, these equations must be solved repeatedly across many iterations, which can take several days even on high-performance computing systems with hundreds of CPUs,” Qian said.
In heat exchanger design, it is commonly assumed that increasing the contact area between a solid wall and a fluid improves heat transfer. However, Qian’s results showed that this is not always the case. While contact area plays a role, the behavior of fluid flow—strongly influenced by channel geometry—can be even more critical. “Optimized designs may feature smaller surface areas, yet outperform traditional ones because the flow is structured to enhance heat transfer more effectively under constraints like pressure drop,” he said. “This highlights the importance of considering both flow dynamics and geometry, rather than relying solely on maximizing surface area.”
After determining the best optimized design, Qian partnered with Dan Thoma, a professor of materials science and engineering at UW, to 3D-print the heat exchanger using a metal AM technique called laser powder bed fusion. The most efficient heat exchanger designs often involve intricate and twisted flow channels. AM techniques such as laser powder bed fusion can build components by selectively melting metal powders to form solid walls.
“However, in complex geometries, loose powder can become trapped in internal flow paths, making post-processing and powder removal difficult,” Qian said. “Ensuring that the optimized structures are both manufacturable and cleanable poses a significant challenge in translating high-performance designs into practical, functional components.”
Qian’s team built two full-size heat exchangers with different core designs—one traditional and one optimized—that were experimentally tested under high-temperature conditions. The core of the optimized heat exchanger was comprised of topologically optimized unit cells. Mark Anderson, a professor of mechanical engineering at UW, conducted thermal-hydraulic tests on these two heat exchangers. The topology-optimized heat exchanger outperformed the straight-channel heat exchanger in the categories of heat transfer, power density, and effectiveness, achieving 27.6 percent higher gravimetric power density than the straight channel heat exchanger. The higher power density enables the heat exchanger to be lighter and more compact—useful attributes for aerospace and aviation applications.
Optimizing topology
Traditional heat exchanger design often depends on an engineer’s intuition to sketch out initial geometries, followed by iterative performance testing using computational fluid dynamics tools. Designers typically adjust and re-size the geometry based on simulation results in an effort to improve heat transfer efficiency.“Our approach breaks from this convention,” Qian said. “We use topology optimization, a computational design method that derives geometry directly from the governing physics of fluid flow and heat transfer—without making assumptions about the shape of flow channels. This dramatically expands the design space and enables the discovery of high-performance heat exchanger configurations that would be difficult, if not impossible, to conceive through intuition alone.”
An especially novel aspect of this research is the integration of manufacturability constraints into the design process. “Our formulation incorporates limits on wall thickness, minimum channel width, overhang angles, and powder removal requirements—all critical for additive manufacturing,” Qian said. “By embedding these constraints into the optimization, we ensure that the resulting complex, high-efficiency designs are not only theoretically optimal, but also practical to fabricate. Without such considerations, features like twisted flow paths could trap powder or violate the physical limits of AM, making production unfeasible.”
Qian and his team plan to expand their computational design approach to a wide range of real-world heat exchanger applications. These include systems in power generation, chemical processing, nuclear thermal management, automotive and aerospace engineering, and renewable energy technologies—all of which rely on efficient heat exchange between fluids.
Beyond enhancing heat transfer, the integration of topology optimization with AM unlocks powerful opportunities for product innovation across various industries. This approach enables engineers to harness the geometric freedom of 3D printing to boost performance through functionally tailored designs, reduce weight and material usage, and simplify assemblies by consolidating multiple components into single, optimized structures.
“In the long term,” Qian said, “we envision our approach playing a key role in designing next-generation thermal components where efficiency, sustainability, and advanced manufacturing all converge.”
Mark Crawford is a technology writer in Corrales, N.M.
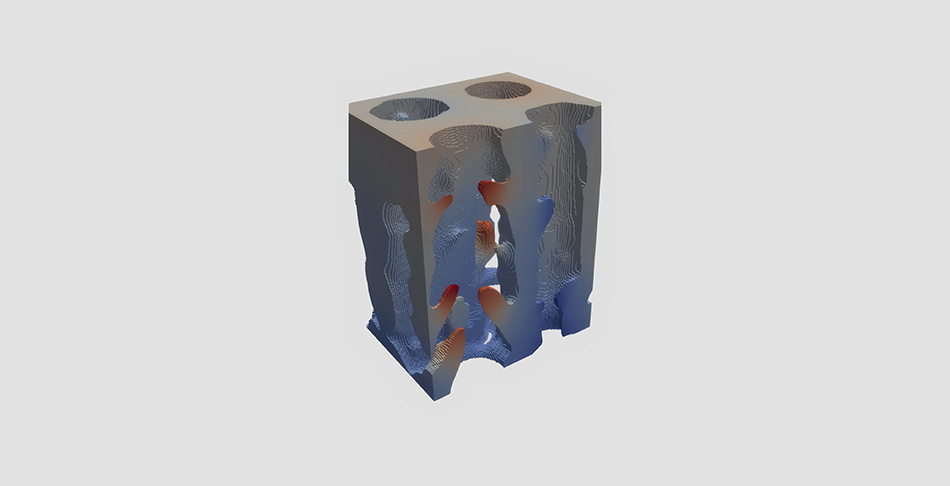
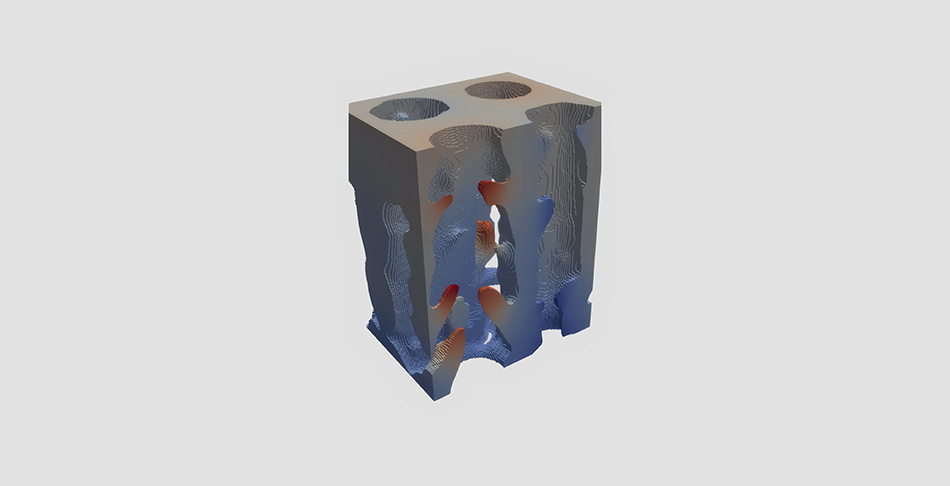