Combining Parts Simplifies Assembly, Improves Quality
Combining Parts Simplifies Assembly, Improves Quality
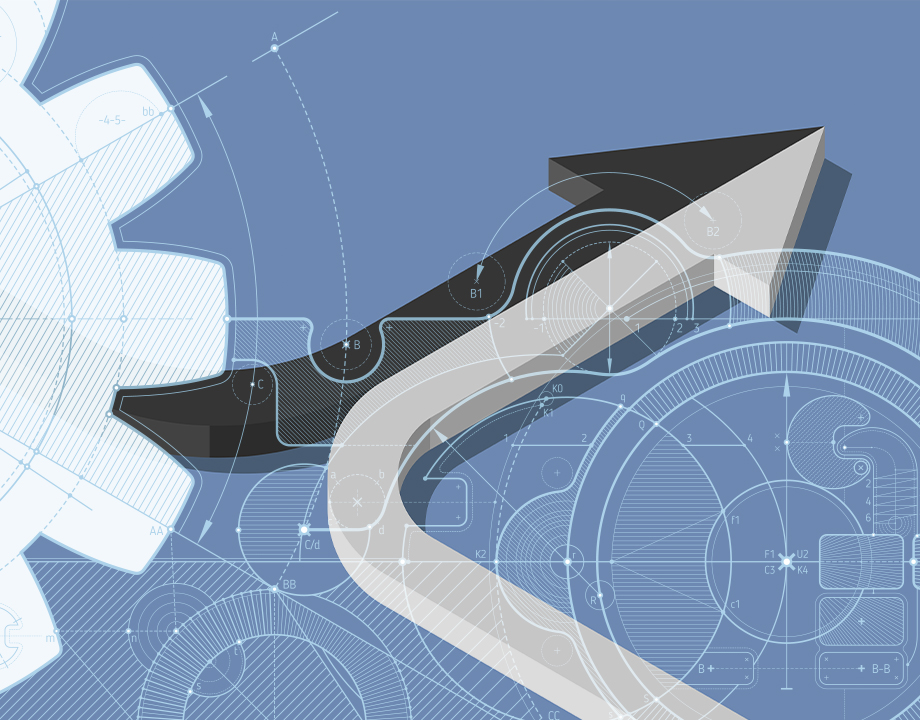
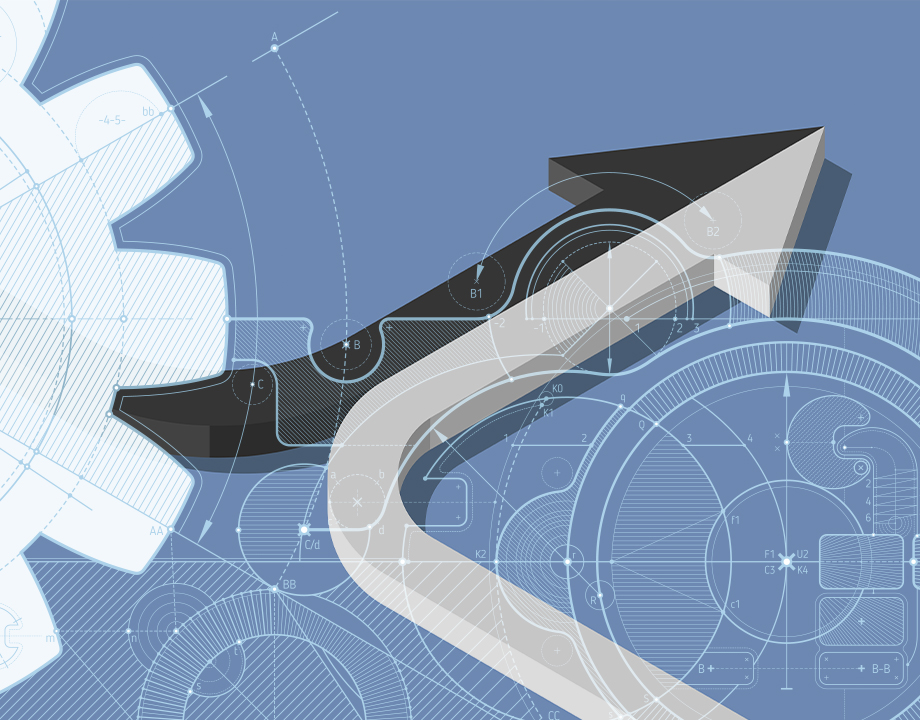
There is growing interest among manufacturers in combining multiple parts into a single part to simplify assembly and improve product quality, functionality, and longevity.
As products get smaller and more complex, with challenging geometries and assemblies, there is more interest in combining multiple parts into a single part. This simplifies assembly and also improves production efficiency.
In many cases, additive manufacturing (AM) is the enabling technology for creating a single combined part to replace multiple parts, which is faster and less costly than making these parts with CNC machines and fastening or welding them together.
When done in the correct circumstances, combining parts saves time and money and improves product quality and longevity. Other advantages of part consolidation are:
- Weight reduction. Using AM, combining parts into a single part results in a lighter-weight part, especially if metal parts are being replaced by a single plastic part with comparable properties. Combining parts eliminates the need for screws or fasteners, making the final part even lighter.
- Reduced assembly and quality control costs. Fewer parts means easier and less time-consuming assembly and faster production, which reduces labor hours, inventory management, and fixturing/tooling. Faster production also gets the final product to market more quickly.
- Less material waste. Consolidating parts typically reduces the amount of material used in a product. With AM, an exact amount of material is used, resulting in virtually no waste. Lattice structures also create open space within a product. Considering that material-related costs are about 40% of total manufacturing costs, the savings that results from part consolidation is significant.
- Increased reliability. Consolidating multiple parts into a single part greatly reduces the number of potential points of failure (points of contact or joining), reducing the risk of failure. This also reduces maintenance costs over the life of the product.
- Improved performance. Part optimization results in lighter-weight products with improved performance. Properties that can be enhanced include heat flow, strength-to-weight ratio, fluid flow, flexibility, and shock absorption.
Mostly for Assembly
AM allows engineers to consolidate parts into a single engineered part that can fit exactly into smaller and geometrically more challenging spaces in complex assemblies. Sometimes this can actually simplify the geometry of the part.
Design for additive manufacturing (DfAM), which utilizes powerful generative software and other analytical tools such as finite element analysis (FEA), is usually the go-to technology for assembly consolidation, often creating a single final part that can only be manufactured with AM.
Not all assemblies need part consolidation. For example, it is not worth the effort or cost to combine two parts into a single part, but combining 20 or more parts into a single part would lead to far greater efficiencies and savings. Single parts that are lighter-weight compared to the multiple parts they are replacing are especially beneficial in the automotive and aviation industries to improve fuel efficiencies.
The four main steps for part consolidation are:
- Select the assembly for consolidation.
- Use generative design and FEA to test hundreds of possible consolidation designs to find the best solution for the assembly.
- Use the data from Step 2 to redesign the parts and possibly the assembly to accommodate the geometry of the new single part (or several, depending on the complexity of the parts and their location in the assembly) and any other modifications needed to improve functionality and performance.
- Retest and validate the new design and parts using FEA to be sure their specifications match the original requirements of the design. Then 3D-print the consolidated design as a prototype or production-ready component.
Examples of Consolidation
- General Motors engineers used generative design and modeling to redesign a seat bracket, combining eight parts into one 3D-printed part after going through 150 artificial intelligence (AI)-based design iterations. The final bracket was 40% lighter and 20% stronger than the original part.
- DMG MORI, a manufacturer of machining equipment, redesigned a robotic end effector using generative design and other simulation tools The new design has 60% fewer components, is nearly two-thirds lighter, and has 45% fewer sealing points in the pneumatic system, with handling precision improved by a factor of 16x.
- GE Aviation developed a metal 3D-printed fuel nozzle tip for its LEAP aircraft engine in 2015—since then over 100,000 have been manufactured. The original redesign consolidated 20 separate components into one single 3D-printed part. Today, GE has advanced their process to include using ceramic matrix composite (CMC) materials and AM to make multiple parts.
More Design Freedom
Generative design, combined with AM processes, allows engineers to redesign assemblies to have fewer parts, which improves quality by reducing the number of potential failure points; assembly consolidations also result in longer-lasting products. Ultimately, by having the technologies and tools they need to consolidate assemblies and reduce the number of parts, engineers can broaden their design thinking to create components or products that have increased functionality and are more cost-effective to make.Mark Crawford is a science and technology writer based in Corrales, N.M.
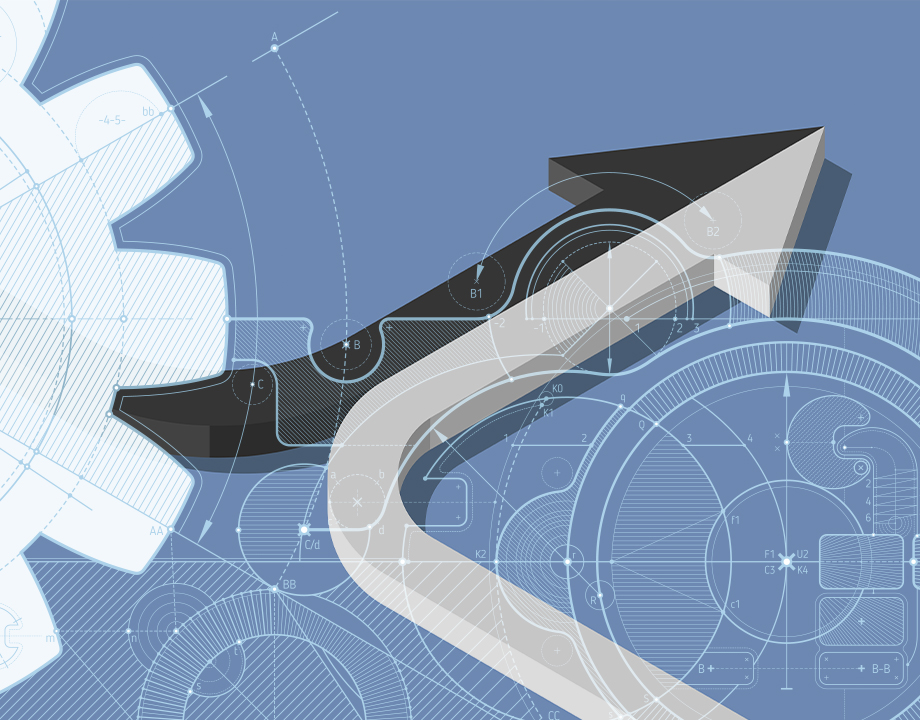
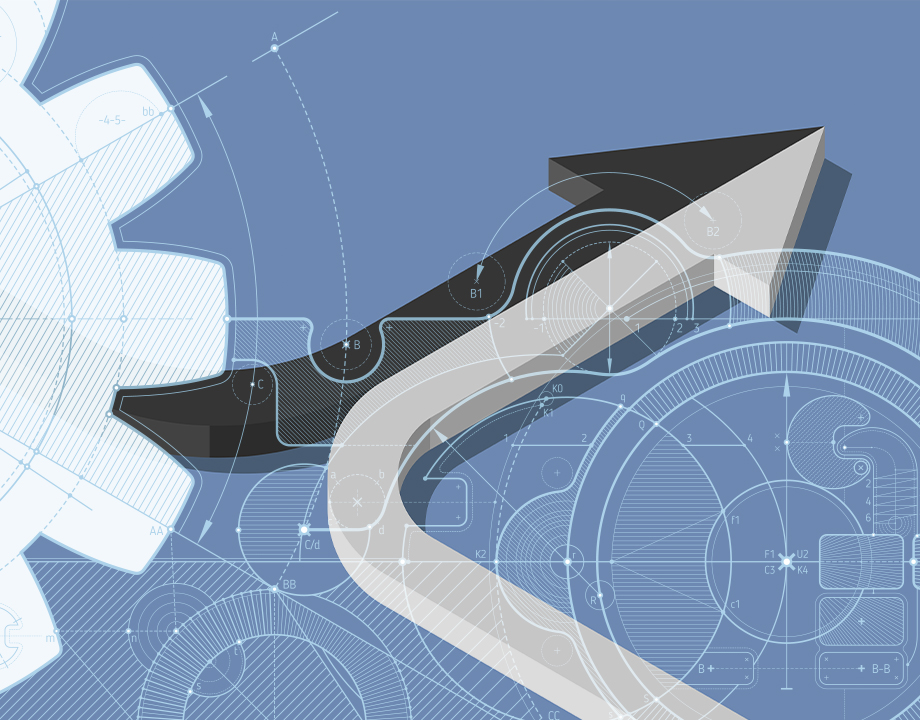