Advanced Optical Films for Mobile Electronics and Displays
Advanced Optical Films for Mobile Electronics and Displays
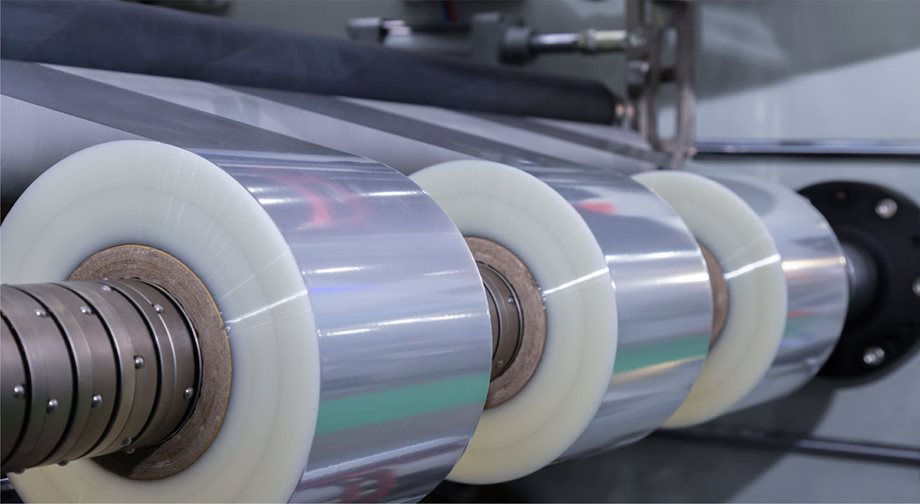
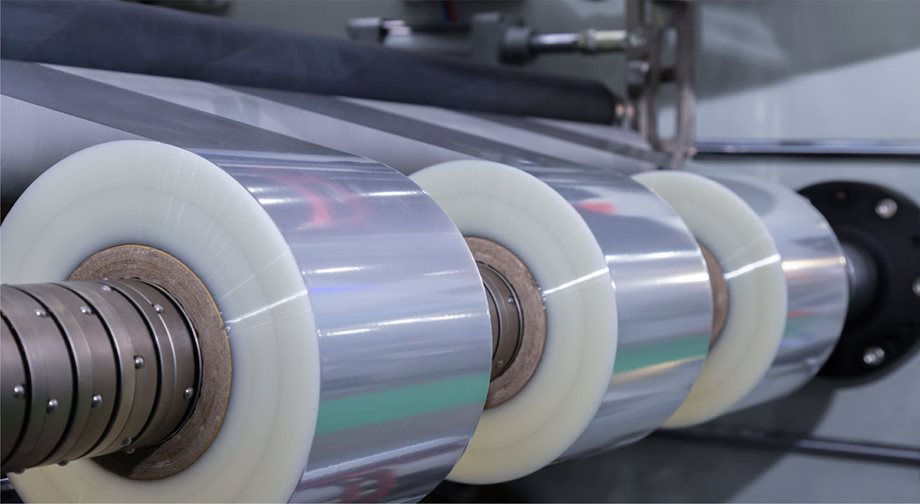
Advanced optical films can manipulate the physical properties of light to meet the demands of today’s advanced electronics.
Advanced optical films provide a number of screen enhancements in today’s mobile electronics and display systems. Inclusive of directional light-control films, anti-glare films, device-protective films and brightness-enhancement films, these materials are converted to form a custom product that extends screen life, increases its efficiency, and enhances its optical properties.
Material Suppliers, such as 3M Company (Display Materials and Systems Division), are constantly innovating for thinner better performing films. Their portfolio consists of three functional groups: directional light control, protection, and brightness enhancement. These films collectively manipulate the physical properties of light to fulfill the display requirements of today’s mobile electronics, consumer electronics, automotive displays, wearable devices and medical display systems.
These three functional groups can be broken down further into the following categories:
Brightness-enhancement films (BEFs) serve a targeted application. Manufacturers integrate the films into a display backlight architecture to increase brightness, decrease weight, mitigate heat and extend battery life. BEFs may also feature a structured surface to recycle and collimate light, increase the viewing angle of the display and improve backlight efficiency.
You May Also Like: Advanced Thermal Interface Materials for Electronic Assemblies
BEFs vary in construction and function based on the Supplier. For example, 3M BEF is a family of optical films with precision micro- replicated prisms that refract and collimate light toward the viewer. These films are available with a variety of prism angles and with various haze and matte finishes. A single BEF or two BEFs crossed at 90° collimate light and increase on-axis brightness of liquid crystal displays (LCDs). The films also increase backlight uniformity and hide defects.
Dual brightness enhancement films feature reflective polarizers. These multi-layered optical films recycle non-polarized light that would otherwise be absorbed by the rear polarizer. They increase backlight by 30 to 40 percent, while distributing polarized light over a wide viewing angle. They are also available with an optically clear adhesive
Non-metallic color-neutral reflectors that reflect 98 percent of all wavelengths across the visible spectrum. These films improve the recycling efficiency of LCD backlights and are paired with dual brightness enhancement film with reflective polarizers to maximize backlight efficiency. Films can range in thickness, for example, 3M ESR film thickness ranges from 65 to 82 microns, and halogen-free versions are also available.
Recommended for You: Adding Textures to Touchscreens
Directional light control films are a group of films that address data privacy needs, field of view requirements and interference concerns of consumer electronics, autonomous vehicles, commercial kiosks and medical displays. These films are integrated into a display to provide a narrow field-of-view, eliminate reflections and glare or provide precise positioning of automotive heads-up display systems. Directional light control films an include gold privacy filters, high-clarity products, touchscreen products and other directional light control films.
Protective films provide an optically transparent barrier. They improve a display’s scratch resistance, impact resistance, UV resistance and water resistance, while maintaining optical transmittance. These products may also provide additional functionality, including anti-glare treatments, contrast enhancements and an organic encapsulation or barrier.
Explore More: AR Goggles for Swimmers
Barrier films are lighter, more flexible and more impact resistant than glass. The optically clear film consists of a multilayer polymer-oxide coating on a heat-stable, optical-grade polyester (PET) base. The non-conductive, protective film provides an oxygen and water vapor barrier for sensitive electronics, display systems or even solar cells. The 3M line of Flexible Transparent Barrier films also features:
To achieve desired characteristics with tight tolerances, vendors require display film solutions that can be converted precisely and efficiently. It is important to work with advanced converting processes that address display film requirements of mobile electronics and other display systems. Core competencies necessary in a converting partner include producing die-cut components with zero-gap tolerances, in cleanroom manufacturing environments, with advanced manufacturing technology. Advanced processes for display technologies include waste-saving procedures like segmented frames.
Advanced OLED and LED display technologies require deliverables that maintain ultra-tight tolerances. Multi-layered optical films for these advanced display systems are produced by converting a stack of high-tack materials.
However, to maintain product orientation and achieve required dimensional accuracies throughout the conversion process, precise registration and web control are paramount. Converters often maintain registration control by incorporating multi-station, servo-driven rotary presses with a proprietary MR- Module and programmable logic controllers. They model and produce multi-layered optical film assemblies and achieve zero-gap tolerances, which provides their customers with the following benefits.
High-quality LED displays, OLED screens, touchscreens, and other high-performance electronic components exhibit increased sensitivity to debris, particulates, and contamination. Ideal converting partner cleanroom capabilities include FDA- registered class 100 to class 100,000 cleanroom facilities, as defined by the United States federal standard concerning the classification of cleanrooms, U.S. FED STD 209E. High-precision converting and advanced rotary die-cutting technologies can be housed in a cleanroom environment to provide high yield rates and low reject rates in volume production and maintains the integrity of OCAs and protective, light-control, or brightness properties.
A backlight only transmits 8% of generated light through a display. With demand for large, high-resolution displays and the need to meet Energy Star 8.0 regulations, manufacturers must rely on advanced optical film solutions to innovate electronics displays. The next step is to find a converting partner that provides high-quality, high-performance optical film solutions at the lowest total cost of ownership. The manufacturers’ fully integrated, in-house, precision converting capabilities and multiple facilities offer competitive solutions to complex manufacturing, and assembly requirements globally.
Magnus Tedestedt is vice president of engineered materials at Boyd Corporation.
Material Suppliers, such as 3M Company (Display Materials and Systems Division), are constantly innovating for thinner better performing films. Their portfolio consists of three functional groups: directional light control, protection, and brightness enhancement. These films collectively manipulate the physical properties of light to fulfill the display requirements of today’s mobile electronics, consumer electronics, automotive displays, wearable devices and medical display systems.
These three functional groups can be broken down further into the following categories:
Brightness-Enhancement Films
Brightness-enhancement films (BEFs) serve a targeted application. Manufacturers integrate the films into a display backlight architecture to increase brightness, decrease weight, mitigate heat and extend battery life. BEFs may also feature a structured surface to recycle and collimate light, increase the viewing angle of the display and improve backlight efficiency.
You May Also Like: Advanced Thermal Interface Materials for Electronic Assemblies
BEFs vary in construction and function based on the Supplier. For example, 3M BEF is a family of optical films with precision micro- replicated prisms that refract and collimate light toward the viewer. These films are available with a variety of prism angles and with various haze and matte finishes. A single BEF or two BEFs crossed at 90° collimate light and increase on-axis brightness of liquid crystal displays (LCDs). The films also increase backlight uniformity and hide defects.
Dual Brightness Enhancement Films
Dual brightness enhancement films feature reflective polarizers. These multi-layered optical films recycle non-polarized light that would otherwise be absorbed by the rear polarizer. They increase backlight by 30 to 40 percent, while distributing polarized light over a wide viewing angle. They are also available with an optically clear adhesive
Enhanced Specular Reflector Films
Non-metallic color-neutral reflectors that reflect 98 percent of all wavelengths across the visible spectrum. These films improve the recycling efficiency of LCD backlights and are paired with dual brightness enhancement film with reflective polarizers to maximize backlight efficiency. Films can range in thickness, for example, 3M ESR film thickness ranges from 65 to 82 microns, and halogen-free versions are also available.
Recommended for You: Adding Textures to Touchscreens
Directional Light Control Films
Directional light control films are a group of films that address data privacy needs, field of view requirements and interference concerns of consumer electronics, autonomous vehicles, commercial kiosks and medical displays. These films are integrated into a display to provide a narrow field-of-view, eliminate reflections and glare or provide precise positioning of automotive heads-up display systems. Directional light control films an include gold privacy filters, high-clarity products, touchscreen products and other directional light control films.
Protective Films
Protective films provide an optically transparent barrier. They improve a display’s scratch resistance, impact resistance, UV resistance and water resistance, while maintaining optical transmittance. These products may also provide additional functionality, including anti-glare treatments, contrast enhancements and an organic encapsulation or barrier.
Explore More: AR Goggles for Swimmers
Flexible Transparent Barrier Films
Barrier films are lighter, more flexible and more impact resistant than glass. The optically clear film consists of a multilayer polymer-oxide coating on a heat-stable, optical-grade polyester (PET) base. The non-conductive, protective film provides an oxygen and water vapor barrier for sensitive electronics, display systems or even solar cells. The 3M line of Flexible Transparent Barrier films also features:
- 88 percent transmittance (>85 percent)
- Thickness of 52 µm
- Low haze; less than 2.5 percent
- High clarity; greater than 95 percent
Considerations for Advanced Converting of Optical Films
To achieve desired characteristics with tight tolerances, vendors require display film solutions that can be converted precisely and efficiently. It is important to work with advanced converting processes that address display film requirements of mobile electronics and other display systems. Core competencies necessary in a converting partner include producing die-cut components with zero-gap tolerances, in cleanroom manufacturing environments, with advanced manufacturing technology. Advanced processes for display technologies include waste-saving procedures like segmented frames.
Tight Tolerances
Advanced OLED and LED display technologies require deliverables that maintain ultra-tight tolerances. Multi-layered optical films for these advanced display systems are produced by converting a stack of high-tack materials.
However, to maintain product orientation and achieve required dimensional accuracies throughout the conversion process, precise registration and web control are paramount. Converters often maintain registration control by incorporating multi-station, servo-driven rotary presses with a proprietary MR- Module and programmable logic controllers. They model and produce multi-layered optical film assemblies and achieve zero-gap tolerances, which provides their customers with the following benefits.
- Increased functionality and life expectancy of electronic display modules
- Enhanced degree of protection against ingress and moisture
- Ability to address challenges when handling and die-cutting optically clear adhesive (OCA)
- Inclusion of multi-station, servo-driven rotary presses and proprietary technologies to maintain registration control and support ultra-tight tolerances
Cleanroom Capabilities
High-quality LED displays, OLED screens, touchscreens, and other high-performance electronic components exhibit increased sensitivity to debris, particulates, and contamination. Ideal converting partner cleanroom capabilities include FDA- registered class 100 to class 100,000 cleanroom facilities, as defined by the United States federal standard concerning the classification of cleanrooms, U.S. FED STD 209E. High-precision converting and advanced rotary die-cutting technologies can be housed in a cleanroom environment to provide high yield rates and low reject rates in volume production and maintains the integrity of OCAs and protective, light-control, or brightness properties.
Future Demand of Advanced Optical Films
A backlight only transmits 8% of generated light through a display. With demand for large, high-resolution displays and the need to meet Energy Star 8.0 regulations, manufacturers must rely on advanced optical film solutions to innovate electronics displays. The next step is to find a converting partner that provides high-quality, high-performance optical film solutions at the lowest total cost of ownership. The manufacturers’ fully integrated, in-house, precision converting capabilities and multiple facilities offer competitive solutions to complex manufacturing, and assembly requirements globally.
Magnus Tedestedt is vice president of engineered materials at Boyd Corporation.
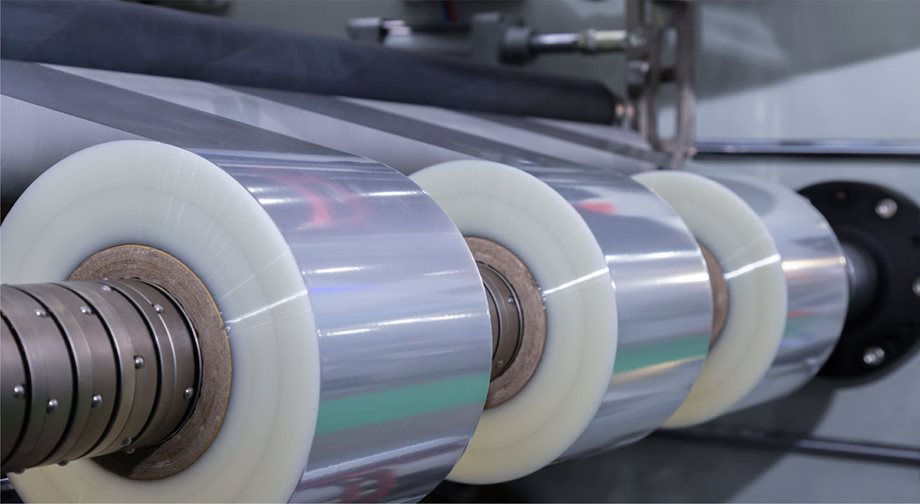
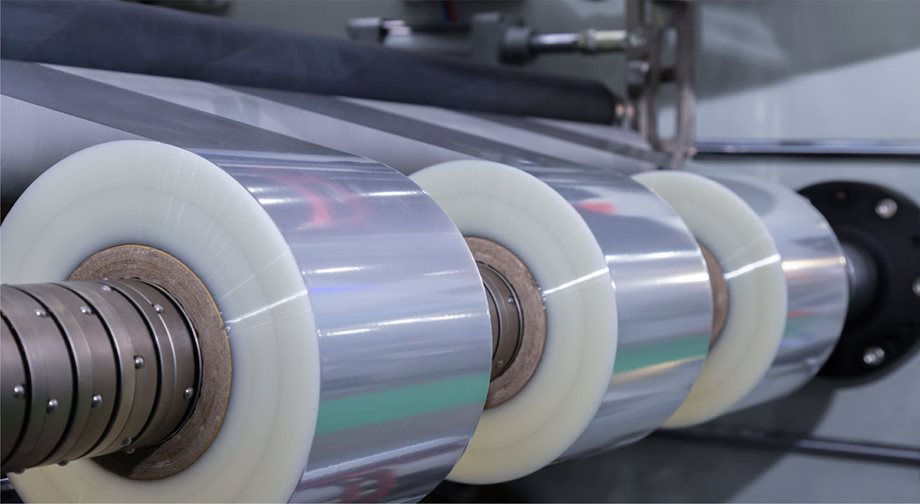