7 Trends Shaping Construction in 2023
7 Trends Shaping Construction in 2023
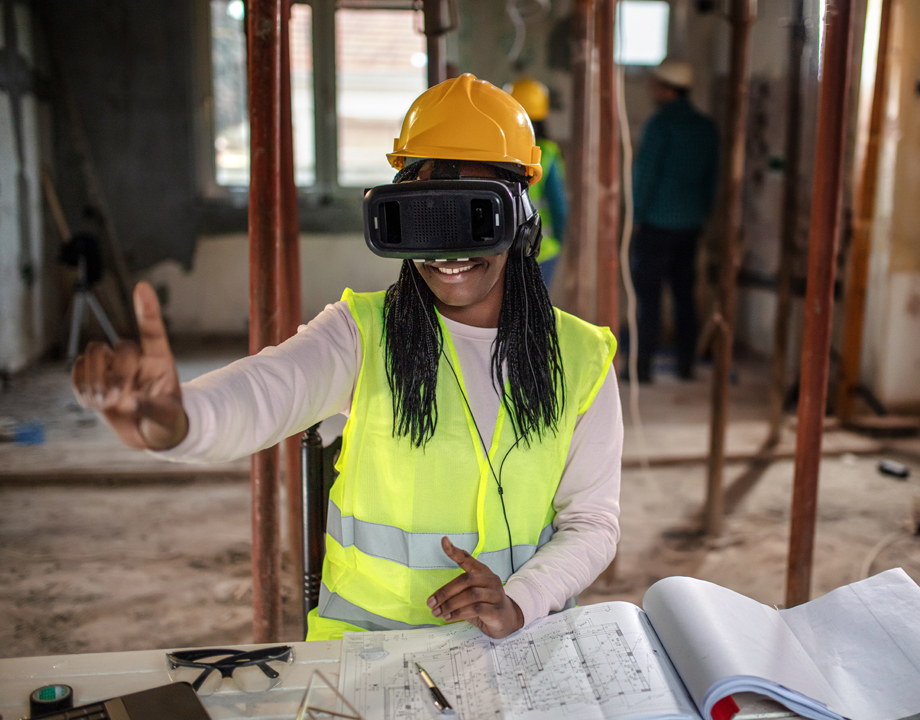
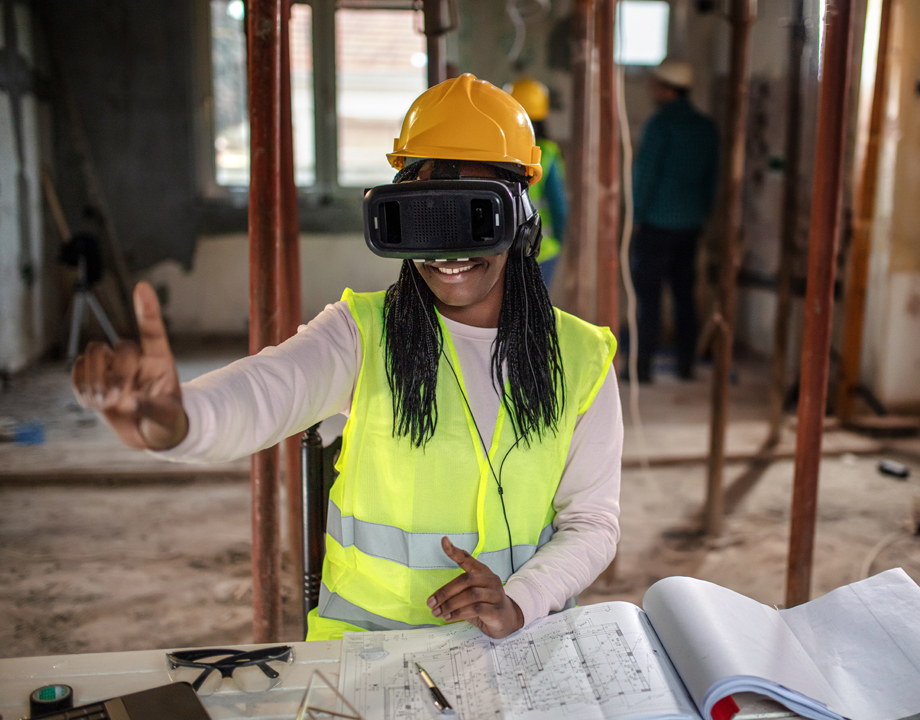
Heading toward mid-2023, trends relating to workforce, technology, and supply chain continue to shape decisions across the construction industry.
Overall, 2022 was an uneven year for the U.S. construction industry, which had to deal with inflation, high interest rates, supply chain disruptions, rising material costs, and a tight labor market. Even so, U.S. builders are cautiously optimistic for 2023, due in part to their successes in adopting digital strategies during the COVID-19 pandemic.
Here are seven key trends that construction firms will encounter in 2023:
Become a Member: How to Join ASME
However, some companies are more proactive than others in embracing and investing in Industry 4.0 technologies. To be competitive, they realize they must be agile for client needs and changing economic conditions. This is happening slowly but steadily—according to the Manufacturing Industry Report by Salesforce, nearly 50 percent of construction professionals report that their companies are changing their business models to be more responsive to changing social or economic conditions.
Mark Crawford is technology writer in Corrales, N.M.
Here are seven key trends that construction firms will encounter in 2023:
1. Sustainability
Building operations and construction generate about 40 percent of energy-related carbon dioxide emissions around the world. Builders and developers are looking for ways to reduce the impacts of their construction projects on the environment. This includes constructing energy-efficient buildings that use less energy (including solar and wind) and producing fewer greenhouse gas emissions, as well as incorporating sustainable materials and green-building methods. Other strategies are converting material waste into useful aggregate onsite and using eco-friendly, locally sourced building materials and products.2. Supply chain management
Hitting deadlines is critical for all stakeholders on a building project—even short delays can cause significant financial losses. A key factor in staying on schedule is supply chain management, including accurate forecasting software for supply needs, timely procurement for just-in-time deliveries, and efficient warehouse management. Materials can be tracked with smart sensors to identify their exact locations during shipping. It is also important to have one or more redundant supply chains as back-ups in case key suppliers have delivery issues or go out of business.3. Virtual reality
Using a virtual reality (VR) simulation system, construction workers can enter and walk through a highly detailed, three-dimensional, interactive rendering of a project and see all the important design structures before they start to build. VR also makes their digital building information modeling (BIM) systems even more effective, allowing the project team to see potential clash points between layouts for electrical or plumbing systems, for example. VR also makes it easier for all stakeholders to communicate effectively in real time, including training programs and identifying safety risks on the project.Become a Member: How to Join ASME
4. Labor shortages
Most construction companies are faced with personnel shortages as their older employees retire, taking with them valuable industry knowledge, with far fewer workers moving into these empty positions. During COVID-19, many construction workers resigned in search of better job opportunities as they re-evaluated career options. Currently, there are about 25 percent more empty construction positions than new hires coming on board, which limits how much new work a construction firm can take on. To attract workers, companies are offering competitive wages and benefits, bonuses, flex time, worker development and training, and better tools and technologies.5. Diversity
Construction companies are looking everywhere to try and fill current and future openings, with many targeting women and underrepresented minorities to help fill positions. To stay competitive, companies are offering additional incentives such as parental leave, flex time, and even daycare to make their construction positions more appealing. Seven of the industry’s largest contractors launched Construction Inclusion Week in 2021. This industry-wide awareness initiative doubled in size after just one year and has grown into an established 501(c)(6) organization that aims to build awareness of the need to improve diversity and inclusion in the construction industry by providing content and resources at all levels.6. Rental equipment
The U.S. equipment rental industry is expected to grow at a rate of 3.4 percent in 2023. More builders are opting to rent equipment to minimize up-front capital investment and save on maintenance costs and expensive repairs. Some rental businesses offer other benefits, such as 24/7 on-site maintenance, repair, and equipment replacement. Renting equipment and being able to swap out machines at minimal expense gives construction companies the opportunity to test out different machines and brands before purchasing.7. Generative design
Generative design in architecture and construction uses powerful software programs to quickly evaluate hundreds or even thousands of building models to identify the best design for a proposed project. Project engineers input design goals, materials, cost constraints, and other data points into the program, which then rapidly evaluates all possible solutions. This saves a huge amount of project development time and allows the engineering and building teams to hit the ground running. Generative design is a highly effective way to identify and correct any flaws in a design before construction starts.Moving forward
There is plenty for construction companies to think about in 2023. First and foremost is fulfilling client needs and surpassing all their expectations. This is enabled by new technologies that allow builders to complete projects faster than before.However, some companies are more proactive than others in embracing and investing in Industry 4.0 technologies. To be competitive, they realize they must be agile for client needs and changing economic conditions. This is happening slowly but steadily—according to the Manufacturing Industry Report by Salesforce, nearly 50 percent of construction professionals report that their companies are changing their business models to be more responsive to changing social or economic conditions.
Mark Crawford is technology writer in Corrales, N.M.
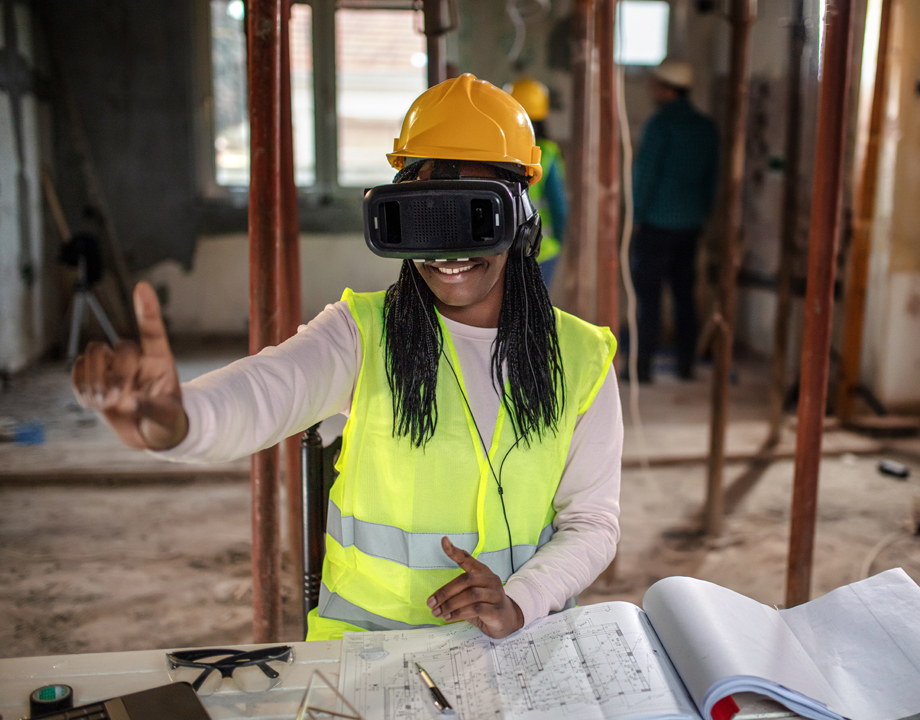
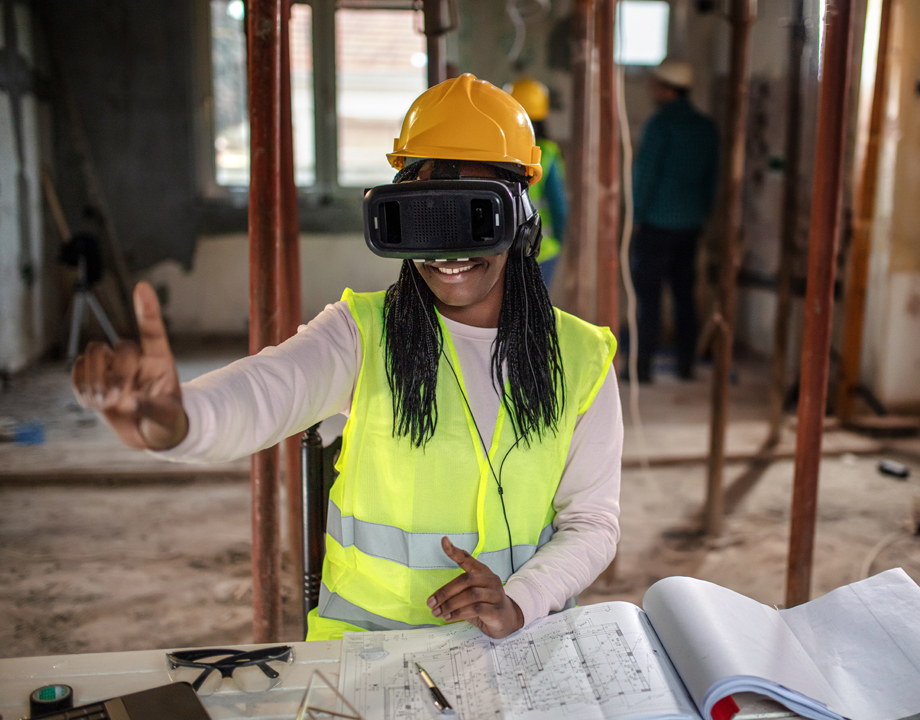