The Industrial Internet and the Future of Work
The Industrial Internet and the Future of Work
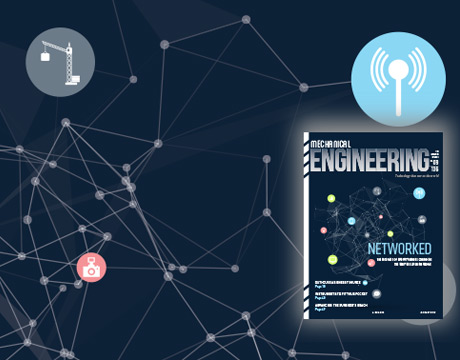
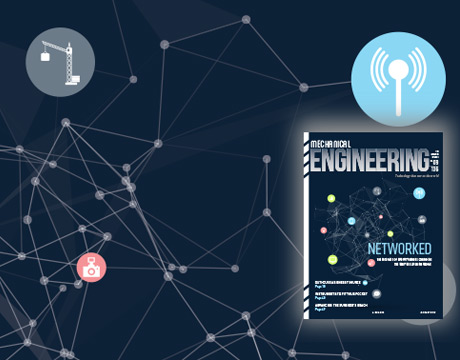
A powerful, deep, and far-reaching transformation is under way in industry. It is fundamentally changing the way we design and manufacture products, and what these products can do. It is making the complex supply and distribution networks that tie the global economy together faster, more flexible, and more resilient.
This transformation is what we call the Future of Work. Of the major forces converging to shape this transformation, the one of most interest to mechanical engineers is the Industrial Internet.
The lines between the physical and digital worlds are becoming increasingly blurred. The integration of cloud-based analytics (“Big Data”) with industrial machinery (“Big Iron”) is creating huge opportunities for productivity gains. In a 2012 white paper for GE, one of us (Annunziata, together with Peter C. Evans) wrote that the rapid decline in the costs of both electronic sensors and storing and processing data now allows us to harvest massive amounts of information from industrial machinery. Using advanced analytics, we can then draw insights that can increase efficiency.
Machines like gas turbines, jet engines, locomotives, and medical devices are becoming predictive, reactive, and social, making them better able to communicate seamlessly with each other and with us. The information they generate becomes intelligent, reaching us automatically and instantaneously when we need it and allowing us to fix things before they break. This eliminates downtime, improves the productivity of individual machines—as jet engines consume less fuel and wind turbines produce cheaper power—and raises the efficiency of entire systems, reducing delays in hospitals and in air traffic.
The Future of Work will substantially accelerate productivity and economic growth. In that 2012 white paper, for instance, the major economic benefits that can accrue from the Industrial Internet alone were estimated for specific sectors. A 1 percent gain in efficiency through deployment of the Industrial Internet would yield $90 billion savings in the oil and gas sector, $66 billion in the power sector, and $30 billion in aviation.
Some economists, notably Robert Gordon of Northwestern University, argue that modern innovations have nowhere near the transformative power and potential economic impact of the Industrial Revolution. But we believe the Future of Work will be as transformational as the Industrial Revolution, and possibly more so. This will bring major improvements to the quality of our lives.
The seeds of this transformation were sown some time ago and have taken time to germinate. But we are now entering the stage where the changes we describe are set to accelerate decisively. To use an expression coined by Ray Kurzweil of Google, we are entering the second half of the chessboard—the phase where changes become all of a sudden a lot more visible, where science fiction more quickly turns into reality.
Even so, this transformation will not happen by itself. We will have to invest in the new technologies and adapt organizations and managerial practices. We will need a robust cyber security approach to protect sensitive information and intellectual property, and to safeguard critical infrastructure from cyber-attacks. The education system will have to evolve to ensure that students are equipped with the right skills for this fast-changing economy. Continuous education and retraining will be needed to cushion the impact of transitional disruptions in the labor market.
It will require time and investment, but this wave of technological innovation will fundamentally transform the way we live.
Machines That Hear and Feel
The Industrial Internet is creating huge opportunities for productivity gains. Industrial machines are being equipped with a growing number of electronic sensors, which allow them to see, hear, and feel a lot more than ever before—all while generating enormous amounts of data. Sophisticated analytics then sift through this data, providing insights that allow us to operate machines—and thus fleets of airplanes and locomotives, and entire systems like power grids or hospitals—in entirely new, more efficient ways.
We are now entering a world where the machines we work with are not just intelligent, but brilliant.
Electronic sensors have been around for some time, so why are these sensors only now creating such gains in productivity? First, their cost is rapidly declining, making it cheaper and easier to deploy them. And thanks to advances of cloud computing, the cost of storing and processing data from these sensors is also dropping quickly, enabling the use of sensors to scale up at an accelerating pace.
And while many industrial assets have been endowed with sensors and software for some time, software has traditionally been physically embedded in hardware in a way that the hardware needs to change every time the software is upgraded. We are beginning to deploy technologies like embedded virtualization, multi-core processor technology, and advanced cloud-based communications throughout the industrial world. This new software-defined machine infrastructure will allow machine functionality to be virtualized in software, decoupling machine software from hardware and allowing us to automatically and remotely monitor, manage, and upgrade industrial assets.
This allows us to shift to preventive, condition-based maintenance. We’ll be able to fix machines before they break rather than service them on a fixed schedule, and it will take us towards zero unplanned downtime: no more power outages, no more flight delays, and no more factory shutdowns.
How will this impact industry? Here’s one example: Ten percent of flight delays and cancellations are currently caused by unscheduled maintenance events, costing the global airline industry an estimated $8 billion—not to mention the impact on all of us in terms of inconvenience, stress, and missed meetings as we sit helplessly in an airport terminal. To address this problem, GE has developed a self-learning predictive maintenance system that can be installed on any aircraft to predict problems a human operator might miss. While in flight, the aircraft will talk to technicians on the ground; by the time it lands, they will already know if anything needs to be serviced. For U.S. airlines alone, this system could prevent over 60,000 delays and cancellations a year, helping over 7 million passengers get to their destinations on time.
The health care industry also has huge gains at stake with the Industrial Internet; just a one percent reduction in existing inefficiencies could yield more than $60 billion in savings globally. Nurses today spend an average of 21 minutes per shift searching for equipment, which means less time spent caring for patients. Industrial Internet technologies can enable hospitals to electronically monitor and connect patients, staff, and medical equipment, reducing bed turnaround times by nearly one hour each.
When you need surgery, one hour matters; it means more patients can be treated and more lives can be saved.
Similar advances are taking place in energy, including renewables like wind. Remote monitoring and diagnostics, which allow wind turbines to communicate with each other and adjust the pitch of their blades in a coordinated way as the wind changes, have helped reduce the electricity generation cost in wind farms to less than 5 cents per kWh. Ten years ago, the equivalent cost was over 30 cents—six times as much.
Faster and Smarter Outcomes
Industrial Internet tools and applications also help people collaborate in a faster and smarter way—making jobs not just more efficient but more rewarding. For instance, secure and reliable cloud-based platforms today allow teams of physicians and caregivers to quickly confer on patient cases, simultaneously access images and reports, and collaborate on diagnosis and treatment plans. By better leveraging each other’s reports and expertise, health care professionals can deliver better health outcomes.
Systems like this are made possible by integrated digital software platforms that support a combination of information collection and storage, new analytic capabilities, and new modes of collaboration. These platforms can provide a standard way to run industrial scale analytics, and connect machines, data, and people. They can be deployed on machines, on-premises or in the cloud, and support technologies for distributed computing and big data analytics, asset data management, machine-to-machine communication and mobility—all in a secure environment that protects industrial data and safeguards access to machines, networks and systems.
It isn’t only the Industrial Internet that is transforming the nature of work. Advanced manufacturing is digitally linking together design, product engineering, manufacturing, supply chain, distribution, and remanufacturing (or servicing) into one cohesive, intelligent system—what we call the Brilliant Factory. New production techniques like additive manufacturing, or 3-D printing, allow us to create completely new parts and products with new properties.
What’s more, technological progress and economic growth are contributing to a seismic shift in the role that human beings play in the production process. Technological progress, notably in high-performance computing, robotics, and artificial intelligence, is extending the range of tasks that machines can perform better than humans can. This may have painful short-term costs as some jobs are displaced and some skills made obsolete. But it dramatically augments the power and economic value of the areas where humans excel: creativity, entrepreneurship, and interpersonal abilities.
And the linking together of the collective intelligence of human beings across the globe, integrated by digital communication networks, will create a human version of high-performance computing—the global brain. Open-source platforms and crowd-sourcing are two of the most effective ways to unleash the creativity and entrepreneurship potential of the global brain. Industry is increasingly relying on both in a trend that will deliver greater flexibility and greater rewards to both employers and employees—and redefine relationships between the two.
Shaping the Future
The Future of Work is being shaped by a profound transformation, driven by the meshing of the digital and the physical worlds, the emergence of new design and production techniques, and a seismic shift in the role that human beings play in the production process. Most of these changes have been under way for some time, but they are now gaining speed and scale in a way that will rapidly change the face of industry as we know it.
The Industrial Internet is leveraging the power of Big Data to create a new generation of brilliant machines that are predictive, reactive and able to communicate seamlessly with each other and with us. Advanced manufacturing techniques like 3-D printing are not only yielding new products, but allowing a faster feedback loop between design, prototyping, production, and customer experience. They are triggering a data-driven reorganization of the supply and distribution networks that tie the individual factory into its ecosystem of customers, distributors, and suppliers.
All this will result in the ability for the entire production process to adjust in real time, automatically, to unexpected circumstances, guaranteeing zero unplanned downtime at the production system level. These changes in turn will allow a faster move towards distributed manufacturing, including through greater reliance on micro-factories.
Technological progress will push a growing share of the workforce toward creativity and entrepreneurship, where humans have a clear comparative advantage over machines. The global brain—the collective intelligence of human beings across the globe integrated by digital communication networks—will grow bigger and more powerful as tens of millions more people gain access to education and to the Internet, becoming able to both tap the global stock of knowledge and contribute to it.
This transformation will take time to unleash its full potential. It will require us to invest in new technologies and adapt organizations and managerial practices. We will need a robust cyber security approach to protect sensitive information and intellectual property and safeguard critical infrastructure from cyber-attacks. The education system will have to evolve to ensure that students are equipped with the right skills for this fast-changing economy. Continuous education and retraining can cushion the impact of inevitable transitional disruptions in the labor market.
The Future of Work will require time and investment, but it will reboot productivity growth and economic activity. And it will reshuffle the competitive landscape for companies and countries alike, and it will fundamentally change—for the better—the way we work and the way we live. ME