Modern Techniques for Inspecting High-Pressure Vessels
Modern Techniques for Inspecting High-Pressure Vessels
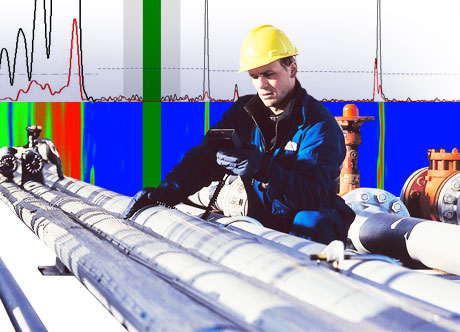
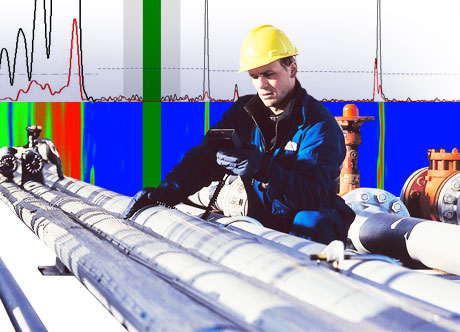
Many high-pressure vessels contain deep bores, thick sections, complex geometries, or miniscule cracks that can affect equipment safety or lifetime. Non-destructive examination (NDE) techniques assess high-pressure vessel designs and equipment for fitness-for-service.
Advanced technologies offer many improvements over traditional techniques such as liquid-penetrant testing, magnetic-particle testing, eddy-current testing, or single-element ultrasonic testing. In addition to providing more accurate assessments, speeding up turnaround times, and reducing maintenance costs, they can detect smaller defects in more locations.
Typically, high-pressure vessel owners outsource NDE inspections to specialists, who work with a variety of inspection and analysis techniques daily. They perform on-site evaluations at their customers' locations and offer many techniques to suit the need. NDE specialists now use advanced techniques to provide benchmarking of new vessels before they go into service, to execute repeated safety checks, and to inspect known defects to assess if they have grown.
NDE Techniques
Guided-wave testing (GWT) shoots guided low-frequency ultrasonic waves along long sections of tubes, pipes, or other thick-walled reactor vessels. Its long-range screening detects changes in material properties due to corrosion or cracking around the circumference and changes in the cross sectional area in its path. When placed on a pipe, a wave collar emits waves that inspect 100% of the volume within its reach, sometimes extending to more than 100'. The energy industry has used GWT testing for more than a decade, and other industries are now beginning to take advantage of its ability to inspect inaccessible piping and thick-walled components.
Eddy-current array (ECA) techniques detect flaws in the surface of conductive materials by detecting changes in the eddy current from a probe coil's magnetic field. The technology is similar to conventional eddy-current testing, but new ECA probes contain an array of coils that facilitate scanning large areas at once with sizes that fit specific part geometries. Not only can array probes inspect a vessel quicker than single-coil probes, but they more readily measure the size and location of flaws and improve the flaw-detection rate.
Linear-phased array (LPA) inspections perform volumetric analysis using ultrasonics with probe heads that have an array of transducers that both transmit and receive pulses. When pulsed sequentially, they steer and focus an ultrasonic beam through multiple angles to image a component's cross section. Depending on the ultrasonic signal power, the array's focusing capability, and materials under test, LPA provides high-resolution measurements to detect small cracks deep within a solid part. Unlike conventional ultrasonic techniques, these advanced transducer heads can create 3D data that make it easier to locate and size flaws in objects with wall thicknesses in excess of 1'.
Rapid, Accurate, Permanent Record
ECA and LPA inspection systems record the ultrasonic or eddy current output as well as the location of the probe tip in 3D space. Measurement involves holding a probe tip stationary or moving it around, either by hand or with a motorized controller or robotic arm. Remote monitoring with probes mounted in fully-automatic mode provides rapid, repeatable computerized data.
Jeff Milligan, a senior engineer at Structural Integrity Associates, which performs comprehensive NDE inspections for customers with high-pressure equipment, says one of the most important advantages that digital 3-D measuring technologies such as these offer, is the ability to record and store data. "Having a permanent record allows vessel owners to feel more confident about its condition. Multiple people can now analyze and verify the data, and a company can keep a permanent record on file to compare with future inspections. Manual techniques of the past did not allow that."
Debbie Sniderman is CEO of VI Ventures LLC, a technical consulting company.
Having a permanent record allows vessel owners to feel more confident about its condition.Jeff Milligan, senior engineer, Structural Integrity Associates
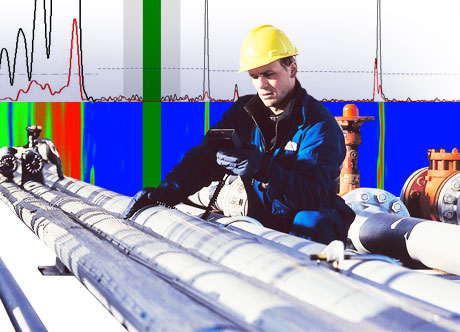
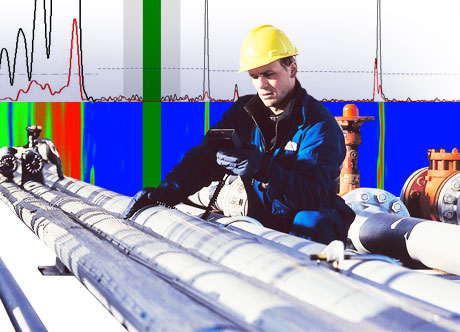