{{ result.Title }}
{{ result.WebinarStart | moment }}
{{ result.WebinarEndTimeString }}
{{ result.WebinarStart | moment }} - {{ result.WebinarEnd | moment }}
{{ result.Profiles.Title }}
{{ result.Profiles.ProfileNames }}
{{ result.Summary }}
{{ result.WebinarCtaText }}
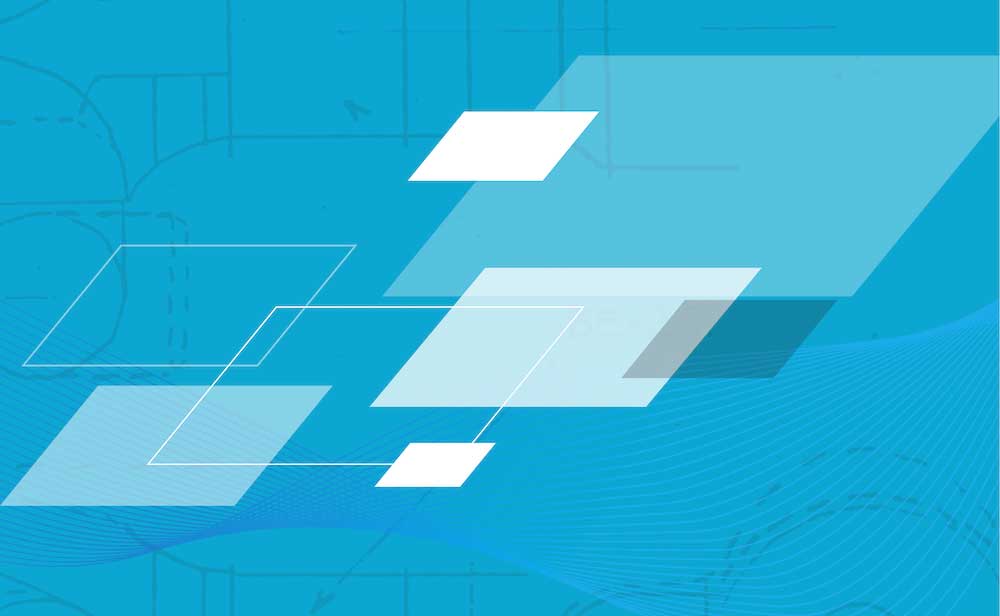
{{ result.ContentFormatText }}
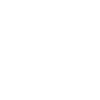
Premium
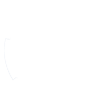
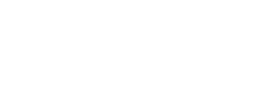
{{ dateDisplay(result.Date) }}
{{ result.Title }}
{{ result.Profiles.Title }}
{{ result.Profiles.ProfileNames}}
{{ result.Content }}
{{ result.Sponsor.Intro }}