Clean Power from Burning Trash
Clean Power from Burning Trash
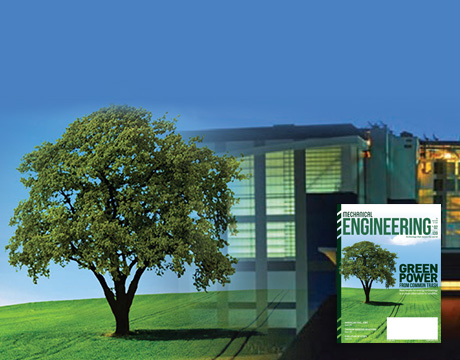
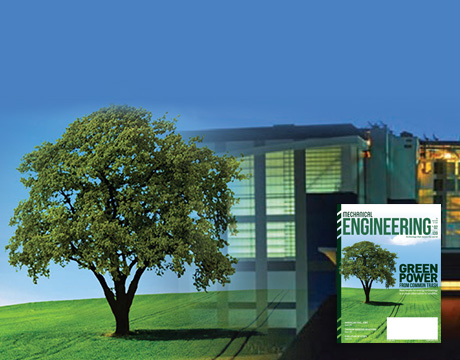
For the past 20 years, municipalities have had few choices for disposing of solid waste. If landfills were nearing capacity, cities were usually forced to spend millions of dollars to design, permit, and build a new one—despite issues with odor, greenhouse gas emissions, and pollution.
That changed in July 2015, when the Solid Waste Authority of Palm Beach County, Fla., began operating Palm Beach Renewable Energy Facility No. 2. It is the first greenfield waste-to-energy plant for municipal solid waste built in the United States in two decades. With combustion and air pollution equipment designed and supplied by The Babcock & Wilcox Co. (B&W), the new facility addresses the pollution and cost issues that stopped municipalities from building waste-to-energy plants for two decades. This is a technology that can change how local governments approach solid waste management, renewable energy, and sustainability.
Based on data from month-long acceptance tests, the Palm Beach facility ranks as the cleanest, most efficient plant of its kind in the world. It generates enough electricity to power 44,000 homes while reducing the volume of waste to be landfilled by 90 percent—enough to extend the lifespan of Palm Beach County’s landfill by up to 30 years.
Like existing waste-to-energy facilities, the new plant earns millions of dollars annually from selling electrical power to the local power company and reclaiming metals left in municipal waste after recycling. Unlike previous facilities, it competes head to head with landfilling on total cost alone.
This waste-to-energy plant also comes with significant environmental benefits. It eliminates the burial of problematic wastes that routinely emit tons of volatile organic compounds and problematic chemicals. The emissions from Palm Beach County’s new waste-to-energy facility are as low as or lower than the cleanest gas-fired turbine generators.
In fact, this waste-to-energy plant slashes the total net release of greenhouse gases to zero or below in severalways. First, waste-to-energy plants emit less net carbon dioxide than fossil fuel plants that use gas, oil, or coal. This is because more than 60 percent of municipal solid waste consists of food, agricultural waste, paper, wood, and other types of biomass. EPA classifies biomass as a renewable resource that adds no net carbon dioxide to the ecosystem.
Second, if the food, paper, and wood in municipal solid waste were landfilled, it would decompose and emit methane. Eliminating emissions of methane—a greenhouse gas 28 to 36 times more powerful than carbon dioxide, according to the EPA—more than offsets any release of carbon dioxide from the facility. This transforms waste-to-energy into a better way to reduce greenhouse gases than landfilling alone.
The advanced technology that makes this plant’s achievements possible represents two decades of progress in hundreds of waste-to-energy plants built in Europe and Asia. Babcock & Wilcox designed many of them. It brings together the best global technologies to set a new standard in economics and emissions reduction that could make it part of long-term renewable energy and sustainability strategy.
Boiler
Each day, the new Palm Beach waste-to-energy plant burns up to 3,000 tons of municipal solid waste created by Palm Beach County’s 1.4 million residents. The facility cost $674 million, or $224,700 per ton of daily capacity, to construct. On an inflation-adjusted basis, this is less than similar, less clean, plants built 20 years ago. It processes waste for about $25 per ton, roughly as much as burying the waste in Palm Beach County’s landfill.
A number of technical advances make these economics possible. They include an innovative grate system on which to burn waste and an advanced emissions control system. The plant’s modularized design saved construction time and costs, while its integrated design maximized energy recovery and minimized water use.
A good example of that integration is the facility’s use of water. The facility gets its water from a variety of sources. Between 5 and 15 percent comes from rain, and 25 to 35 percent from non-potable industrial water. The remaining 60 percent is recycled from water used in the cooling tower of an older waste-to-energy facility next door. In the past, this plant’s water was injected into a deep well for disposal.
The facility also saves water by using an air-cooled (rather than a water-cooled) heat exchanger to condense steam after it exits the turbine, so it can be returned as condensate to the power cycle.
Through recycle and reuse, the new facility actually lowers the amount of water that both facilities need to inject into deep underground wells. The result is water discharge for the new facility that is better than net zero—less that what the older facility discharged alone.
;custompagebreak;The Palm Beach waste-to-energy facility consists of two central elements: the boiler and the emissions control systems.
The boiler system uses three 1,000-ton-per-day boilers to power a 95 MW turbine generator. It also features several advanced technologies used for the first time in the United States. This starts with the crane loading area. The plant collects waste in a football-field-sized pit that’s 40 feet deep. Operators use two of the facility’s three 16-ton cranes to mix the waste so it will burn more uniformly in the boiler. The cranes generate electricity when braking and can run autonomously at night to feed the boilers.
The cranes deliver the waste to a hopper, where hydraulic rams push it onto an inclined grate that runs under the furnace. Grates are often maintenance trouble spots because their holes plug up. B&W Volund’s DynaGrate combustion system solves this problem by using grate bars (with air gaps between them) that rotate back and forth 60 degrees to mix and move the waste down its length. Operators can control the grate speed and air flow in each of the grate’s eight modular sections. This enables them to control the burn very precisely, while reducing carbon monoxide combustion products and unburned carbon in the ash.
Despite Palm Beach County’s extensive curbside recycling, metals remain in the waste. These are captured in the bottom ash. After cooling, the ash goes to a rotating drum magnetic separator, where large electromagnets remove iron and steel. The remaining ash then goes through an eddy current separator to recover aluminum and other non-ferrous metals from the ash.
On average, the facility has recovered 2,000 tons of steel and iron and 100 tons of aluminum per month. The remaining ash is mixed with lime to stabilize the ash so it is safe for landfilling. In Europe, this material is used in construction materials and as aggregate for roadbeds. This type of recycling is being evaluated in Palm Beach as well.
Emissions
Meanwhile, the waste burned on the grate has undergone partial combustion. This produces carbon monoxide and nitrogen oxides (CO and NOx). As the products of combustion, or flue gas, move up through the furnace, they pass by an overfire air system, which injects the balance of the combustion air into the gas. This effectively completes combustion and converts NOx into nitrogen and oxygen (N2 and O2) and turns CO into carbon dioxide (CO2). Maintaining gas temperatures above 1800 °F for 2 seconds or more also destroys organic compounds, including dioxins and furans.
The hot flue gas then passes through the boiler components that turn water into superheated steam. This steam powers the turbine generator and then goes to an air-cooled heat exchanger, where it condenses into water and returns to the power cycle.
The flue gas exiting the boiler has cooled enough to enter the emissions control system. The first step involves spraying activated carbon particles into the flue gas to absorb mercury vapor and any residual dioxins and furans not destroyed in the furnace.
The flue gas then moves to a piece of machinery called the spray dryer absorber, where a spray of lime slurry absorbs sulfur dioxide, hydrogen chloride, and hydrogen fluoride, air pollutants found in the flue gas.
The flue gas then moves into a bag house containing a small forest of six-inch-diameter fluoropolymer membrane-coated bags. As the flue gas passes through the bags, it deposits entrained ash, spent activated carbon and lime, and any other particulate on the outside of the bags in a filter cake deposit. The cleaned flue gas then passes up through the center of the bag.
Unreacted lime and carbon in the filter cake continue to scrub pollutants from the gases that pass through the bags. To prevent the cake from building up, a pulse of pressurized air periodically shakes the bag and knocks it o.. This ash is recovered and mixed with bottom ash from the furnace for disposal.
The last emissions step converts any remaining NOx into nitrogen gas and water vapor through selective catalytic reduction, or SCR. This involves mixing ammonia into flue gas and flowing the mixture over a catalyst. The Palm Beach facility is the first U.S. waste-to- energy plant to use this catalyst technology. Unfortunately, the flue gas exits the bag house at around 280 °F. It must reach 450 °F before passing over the SCR catalyst. The facility does this by reheating the gas by recapturing some of the heat from the hot flue gas exiting the SCR reactor and adding a small amount of boiler drum steam to provide the additional energy to reach 450 °F. This additional heat input from the boiler drum is then recaptured into the deaerator water system—integrating the emissions control system into the power cycle to maximize energy efficiency.
;custompagebreak;Performance
Palm Beach Renewable Energy Facility No. 2 was designed to generate power, recover metals, and reduce waste volumes and pollution. The only way to justify its cost and complexity is to assess how well it accomplishes these goals. The plant’s initial 30-day acceptance test in 2015 demonstrated that it is the cleanest and most efficient waste-to-energy plant of its kind in the world today.
During the month-long acceptance tests to validate plant operations, the facility easily met its guaranteed capacity of 3,000 tons per day of post-recycled municipal solid waste without interruption. The plant was also guaranteed to generate 625 kWh per ton of waste, the highest ever in a waste-to- energy plant using an air-cooled condenser. It exceeded that target by 6 to 8 percent.
The facility also exceeded its guaranteed metals recovery rates. It recovered 97.2 percent of all ferrous metal in the waste (versus a 90 percent guarantee) and 88.6 percent of non-ferrous metal (compared with an 85 percent guarantee).
Primary air pollutants, such as nitrogen oxides and sulfur oxides, were not only below those required by the new plant’s emissions permit, but were as good or better than those of the best gas turbines.
Waste-to-energy plants have special emissions requirements. They must strictly curtail the release of dioxins, furans, and trace mercury, cadmium, and lead. The new plant’s permit sets emission limits measured in millionths and billionths of a gram per dry standard cubic meter of gas.
Test results showed that the facility’s emissions are, at their maximum, an order of magnitude lower than those limits. This makes it the best in class of any waste-to-energy plant in the world.
To put these results into perspective, before the 1980s, scientists did not understand the environmental risks of dioxins and furans. As a result, waste-to-energy plants were allowed to discharge the equivalent of more than 10,000 nanograms per dry standard cubic meter. Palm Beach facility’s measured emissions are four orders of magnitude lower, a 99.996 percent reduction.
As noted earlier, municipal solid waste buried in landfills emits methane, a powerful greenhouse gas. In 2007, a study that used an EPA evaluation methodology determined that collecting methane from landfills and then flaring or burning it for power would reduce emissions dramatically when compared with landfilling alone. Yet about 30 percent of a landfill’s methane still escapes into the atmosphere.
According to the same study, waste-to-energy plants produce lower net greenhouse gas emissions than any landfilling option. Not only do they displace fossil fuels to produce electricity, but they effectively eliminate methane landfill emissions by burning the biodegradable landfill waste that forms methane. According to the EPA, this reduces net greenhouse gas emissions by 1 ton for every 1 ton of municipal solid waste burned. The Palm Beach plant achieves similar results.
In addition, the plant also recovers more than 95 percent of the metals left in post-combustion bottom ash. This reduces the CO2 emissions that would have been generated by processing virgin ore to make those metals.
Despite its superior environmental performance, no municipality can afford to build a waste-to-energy plant unless it can compete head-to-head economically with landfilling. As previously noted, Palm Beach County’s new facility has demonstrated this by processing waste for $25 per ton, about the same as the county’s landfill.
The Solid Waste Authority earns millions of dollars per year by selling electricity back to the local power company (without a premium) and by selling recovered metals. In addition, the new plant saves money by reducing landfill volume by 90 percent. This extends the life of the existing landfill and avoids expensive permitting and construction of a new one.
Finally, the facility’s design is highly modularized and integrated. Certainly, its cost, $674 million in 2012 dollars, sounds impressive. Yet, on an inflation-adjusted basis, it cost less to build than the less efficient and less environmentally sound waste-to-energy plants built 20 years ago.
Waste-to-energy plants cannot compete everywhere. Many municipalities can dispose of solid waste for less than $25 per ton. But in many parts of Florida, as well as urban areas such as New York City, Chicago and Cleveland, landfill costs may reach $40 to $50 per ton. Waste-to-energy plants give municipalities facing rising landfill costs an economically and environmentally sound alternative to consider. ME
JOHN B. KITTO, JR. PE is an ASME Fellow and was the development manager for the Palm Beach Waste-to-Energy Project for Babcock & Wilcox in Barberton, Ohio.
LARRY A. HINER is project developer for industrial steam generation (including waste-to-energy) with Babcock & Wilcox in Barberton, Ohio.
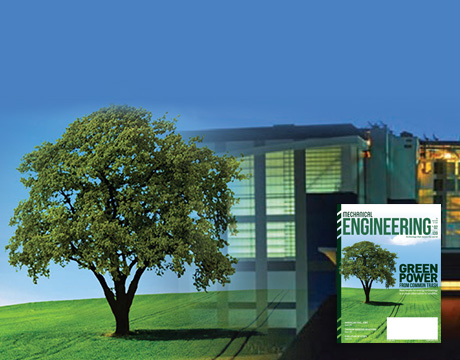
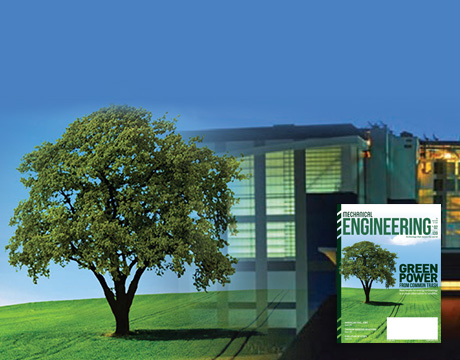