Q&A: Room-Temperature Process Restores Damaged Metals to Full Strength
Q&A: Room-Temperature Process Restores Damaged Metals to Full Strength
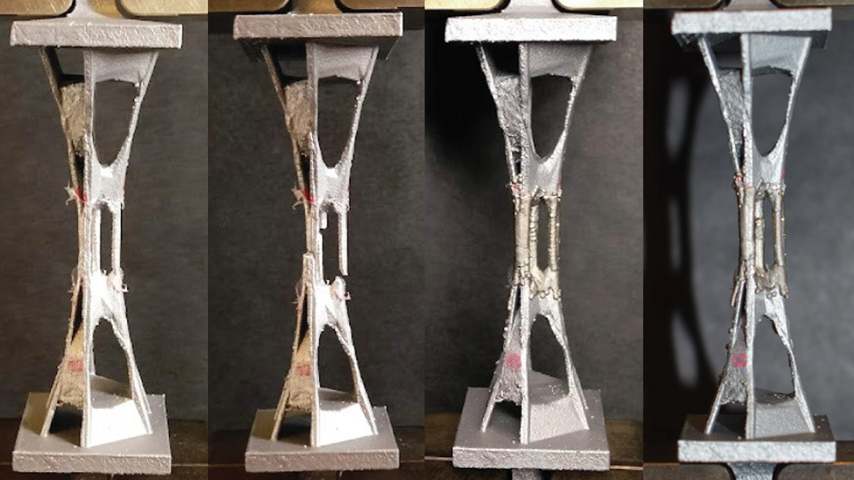
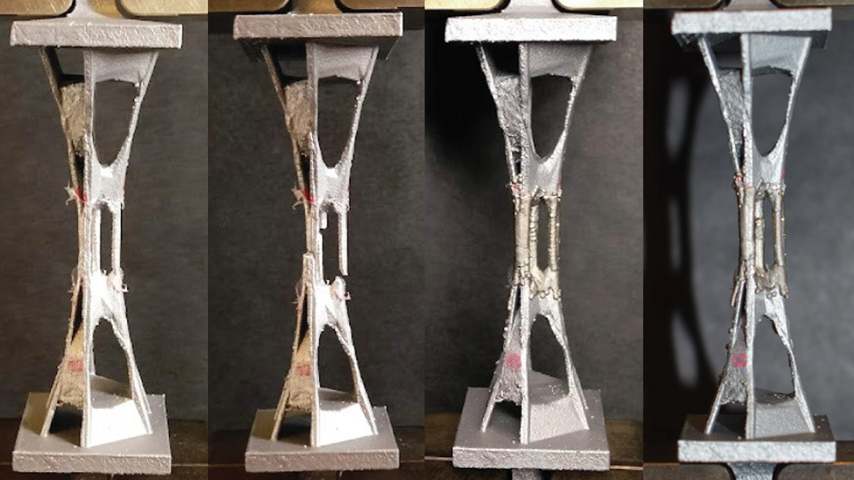
Inspired by the natural healing of bone, researchers have developed a room-temperature electrochemical self-healing process that completely restores tough-to-heal metals and metal alloys.
Researchers at the University of Pennsylvania, led by assistant professor of mechanical engineering and applied mechanics James Pikul, have developed a new metal-healing technique that fully restores previously fractured or otherwise unrepairable metals to full original strength—presenting sustainable options for manufacturers and especially users of heavy equipment.
The standard approach for this kind of repair is high-temperature welding, which only works for certain alloys and can create its own cracks under extreme heat. As a result, difficult-to-repair metals are often discarded in landfills, causing both economic and environmental problems.
Inspired by the natural healing of bone, Pikul’s team developed a new process called electrochemical healing that repairs fractures in various metallic materials, including steel, aluminum alloys, and even complex 3D-printed structures, under room-temperature conditions. The process recovers the metal’s full tensile strength, even for un-weldable aluminum alloys used in aerospace.
AMSE recently interviewed Pikul to learn more about his new process, which creates a new approach for repairing metals in a cost-effective and sustainable way.
ASME: What inspired this idea? Was there an “aha” moment?
Pikul: There were several. We have always been inspired by bone. Everyone knows that bone heals, but it was not until we dove deeper into understanding how it works that we realized we could mimic some of bone’s capabilities with electrochemistry.
Bone heals quite differently than most modern “self-healing” materials, which rely on a healing compound or chemistry being very close to the place where the material breaks. Bone is different in that when it breaks, energy, proteins, and building blocks for re-growth are transported from other parts of the body to the fracture location through the bloodstream. We wondered if this transport-based healing mechanism could be applied to hard materials [such as, metal and ceramics], since bone is also a hard material.
Also, most self-healing materials are soft [made of polymers] and the self-healing works because polymers can move at room temperature. Hard materials like metals and bone do not move at all at room temperature, which is why we need to heat them up.
Here is our second “aha” moment: Although solid metals cannot move at room temperature, metal ions in water can easily move at room temperature. So, we used electrochemistry to turn solid metal into metal ions by taking away the metal’s electrons. This can be done with a battery. We can then move those metal ions and turn them back into solid metal by giving them electrons. Therefore, by controlling where we remove and add electrons, we are effectively moving solid metal between these locations, all at room temperature.
ASME: Please share a few more details about this process.
Pikul: To allow the metal to “heal,” we put the metal in a salty water mixture [electrolyte] that contained nickel ions. We then applied a negative voltage, which moved ions in the electrolyte toward the metal cracks, leading to an increase in electrons, until metal ions from the electrolyte started to steal excess electrons—a chemical reaction called reduction. This turned the ions into solid metal atoms, and as atoms grew on the surface, they healed the fracture. We applied a protective polymer coating to the metal to act as a barrier, so when it was exposed to the electrolyte nickel plating, or healing, the process was limited to the fracture site so it could not affect any other parts of the metal structure.
ASME: What were the biggest research challenges in developing this idea?
Pikul: The biggest challenge was applying this approach to a broad set of useful metals. If one simply takes two pieces of broken metal and connects them with an electrochemically deposited bridge, the repaired metal will very likely break easily. This is not too surprising, since it has been known in the electrochemistry community that electroplated metals do not adhere well to certain metals, such as aluminum alloys. It took us some time and careful experimentation to figure out the different ways these repaired metals break and how to find the sweet spot for healing where we can fully restore the original metal’s strength. Our research showed we can heal nickel, low-carbon steel, two un-weldable aluminum alloys, and a 3D-printed difficult-to-weld shellular structure, using a single common electrolyte.
What surprised us the most was that we were able to recover 100 percent of the strength across all the metals we tried. We were expecting it to only work well for a few alloys, but we were able to repair aircraft-grade aluminum, common steels, and even 3D printed alloys, which was incredibly exciting.
ASME: What aspects of your work would be of most interest to mechanical engineers?
Pikul: I feel like everything about this is interesting to mechanical engineering—especially the transport of ions through electrochemistry for the heat and mass transfer scientists and the growth of metal to repair structural members for mechanics and materials engineers. I think a particularly cool visual of this process is that the metal grows like squeezing a gel out of tube, except it is not a liquid—it is a hard and strong nickel or copper, and when two of these growing interfaces connect, they form strong bonds, as if the metals were cast together. And we can control where this happens with electricity and electrolyte placement.
I think engineers will also be interested to know that this approach can repair what people considered un-weldable or difficult-to-weld metals. We can also use it to repair complex geometries and 3D-printed parts where you cannot possibly get a welding torch to access all the part surfaces. And because it can be done at room temperature, you can repair metal with composites or electronics nearby and you do not have to work about the high temperature deforming or destroying the other parts of your device.
ASME: What is the greatest value of what you have discovered so far?
Pikul: Well, humans have been shaping and repairing metals for over 6,000 years, and over this time they have only been able to do this by heating the metal to close to, or above, its melting point. This costs lots of energy, produces lots of CO2, and damages anything nearby that is not a metal or ceramic. It’s a very brute-force approach. As far as we can tell, our work is the first time in the 6,000 years that humans have been using metal that someone has healed structural metals at room temperature. We think that alone is amazing, but in addition, our approach allows us to tap into all the advances in modern electronics since it uses electrochemistry.
AMSE: What are your next steps?
Pikul: We have had interest from companies and have considered starting a company to meet those needs, but we also need to do more testing to understand how the repaired metals hold their strength under different loading conditions and temperature fluctuations. For 3D-printed metal parts in particular, there are very few ways to repair them, and it is resource-intensive to have to melt down these parts, turn them into powders, and re-print them when even the smallest amount of damage occurs. We hope that our new approach to repair can extend the lifetime of 3D-printed metals.
ASME: What else would you like people to know about your electrochemical self-healing process?
Pikul: Besides just fixing broken parts, it is important to realize how important repair and recycling are to a modern CO2-neutral economy. Annually, the mining, refining, and processing of structural metals result in over 3 billion tons of CO2-equivalent emissions. The mining and refining of aluminum alone produces over 14,000 tons of by-products. Improving the sustainability of structural metals, through a circular economic model based on recycling and repair, plays an important role in mitigating greenhouse gas emissions and addressing many detrimental ecological effects.
Mark Crawford is technology writer in Corrales, N.M.
The standard approach for this kind of repair is high-temperature welding, which only works for certain alloys and can create its own cracks under extreme heat. As a result, difficult-to-repair metals are often discarded in landfills, causing both economic and environmental problems.
Inspired by the natural healing of bone, Pikul’s team developed a new process called electrochemical healing that repairs fractures in various metallic materials, including steel, aluminum alloys, and even complex 3D-printed structures, under room-temperature conditions. The process recovers the metal’s full tensile strength, even for un-weldable aluminum alloys used in aerospace.
AMSE recently interviewed Pikul to learn more about his new process, which creates a new approach for repairing metals in a cost-effective and sustainable way.
ASME: What inspired this idea? Was there an “aha” moment?
Pikul: There were several. We have always been inspired by bone. Everyone knows that bone heals, but it was not until we dove deeper into understanding how it works that we realized we could mimic some of bone’s capabilities with electrochemistry.
Bone heals quite differently than most modern “self-healing” materials, which rely on a healing compound or chemistry being very close to the place where the material breaks. Bone is different in that when it breaks, energy, proteins, and building blocks for re-growth are transported from other parts of the body to the fracture location through the bloodstream. We wondered if this transport-based healing mechanism could be applied to hard materials [such as, metal and ceramics], since bone is also a hard material.
Also, most self-healing materials are soft [made of polymers] and the self-healing works because polymers can move at room temperature. Hard materials like metals and bone do not move at all at room temperature, which is why we need to heat them up.
Here is our second “aha” moment: Although solid metals cannot move at room temperature, metal ions in water can easily move at room temperature. So, we used electrochemistry to turn solid metal into metal ions by taking away the metal’s electrons. This can be done with a battery. We can then move those metal ions and turn them back into solid metal by giving them electrons. Therefore, by controlling where we remove and add electrons, we are effectively moving solid metal between these locations, all at room temperature.
ASME: Please share a few more details about this process.
Pikul: To allow the metal to “heal,” we put the metal in a salty water mixture [electrolyte] that contained nickel ions. We then applied a negative voltage, which moved ions in the electrolyte toward the metal cracks, leading to an increase in electrons, until metal ions from the electrolyte started to steal excess electrons—a chemical reaction called reduction. This turned the ions into solid metal atoms, and as atoms grew on the surface, they healed the fracture. We applied a protective polymer coating to the metal to act as a barrier, so when it was exposed to the electrolyte nickel plating, or healing, the process was limited to the fracture site so it could not affect any other parts of the metal structure.
ASME: What were the biggest research challenges in developing this idea?
Pikul: The biggest challenge was applying this approach to a broad set of useful metals. If one simply takes two pieces of broken metal and connects them with an electrochemically deposited bridge, the repaired metal will very likely break easily. This is not too surprising, since it has been known in the electrochemistry community that electroplated metals do not adhere well to certain metals, such as aluminum alloys. It took us some time and careful experimentation to figure out the different ways these repaired metals break and how to find the sweet spot for healing where we can fully restore the original metal’s strength. Our research showed we can heal nickel, low-carbon steel, two un-weldable aluminum alloys, and a 3D-printed difficult-to-weld shellular structure, using a single common electrolyte.
What surprised us the most was that we were able to recover 100 percent of the strength across all the metals we tried. We were expecting it to only work well for a few alloys, but we were able to repair aircraft-grade aluminum, common steels, and even 3D printed alloys, which was incredibly exciting.
ASME: What aspects of your work would be of most interest to mechanical engineers?
Pikul: I feel like everything about this is interesting to mechanical engineering—especially the transport of ions through electrochemistry for the heat and mass transfer scientists and the growth of metal to repair structural members for mechanics and materials engineers. I think a particularly cool visual of this process is that the metal grows like squeezing a gel out of tube, except it is not a liquid—it is a hard and strong nickel or copper, and when two of these growing interfaces connect, they form strong bonds, as if the metals were cast together. And we can control where this happens with electricity and electrolyte placement.
I think engineers will also be interested to know that this approach can repair what people considered un-weldable or difficult-to-weld metals. We can also use it to repair complex geometries and 3D-printed parts where you cannot possibly get a welding torch to access all the part surfaces. And because it can be done at room temperature, you can repair metal with composites or electronics nearby and you do not have to work about the high temperature deforming or destroying the other parts of your device.
ASME: What is the greatest value of what you have discovered so far?
Pikul: Well, humans have been shaping and repairing metals for over 6,000 years, and over this time they have only been able to do this by heating the metal to close to, or above, its melting point. This costs lots of energy, produces lots of CO2, and damages anything nearby that is not a metal or ceramic. It’s a very brute-force approach. As far as we can tell, our work is the first time in the 6,000 years that humans have been using metal that someone has healed structural metals at room temperature. We think that alone is amazing, but in addition, our approach allows us to tap into all the advances in modern electronics since it uses electrochemistry.
AMSE: What are your next steps?
Pikul: We have had interest from companies and have considered starting a company to meet those needs, but we also need to do more testing to understand how the repaired metals hold their strength under different loading conditions and temperature fluctuations. For 3D-printed metal parts in particular, there are very few ways to repair them, and it is resource-intensive to have to melt down these parts, turn them into powders, and re-print them when even the smallest amount of damage occurs. We hope that our new approach to repair can extend the lifetime of 3D-printed metals.
ASME: What else would you like people to know about your electrochemical self-healing process?
Pikul: Besides just fixing broken parts, it is important to realize how important repair and recycling are to a modern CO2-neutral economy. Annually, the mining, refining, and processing of structural metals result in over 3 billion tons of CO2-equivalent emissions. The mining and refining of aluminum alone produces over 14,000 tons of by-products. Improving the sustainability of structural metals, through a circular economic model based on recycling and repair, plays an important role in mitigating greenhouse gas emissions and addressing many detrimental ecological effects.
Mark Crawford is technology writer in Corrales, N.M.
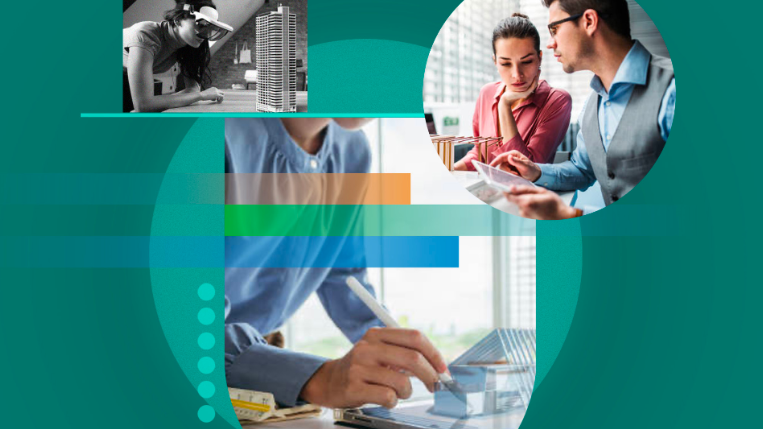
Pulse of the Profession: CAD in 2030
CAD technologies and their applications have been steadily evolving ever since, ushering in a bevy of new techniques and approaches over the decades.