Rare Earth Recovery from End-of-Life Device is Just One Solution
Rare Earth Recovery from End-of-Life Device is Just One Solution
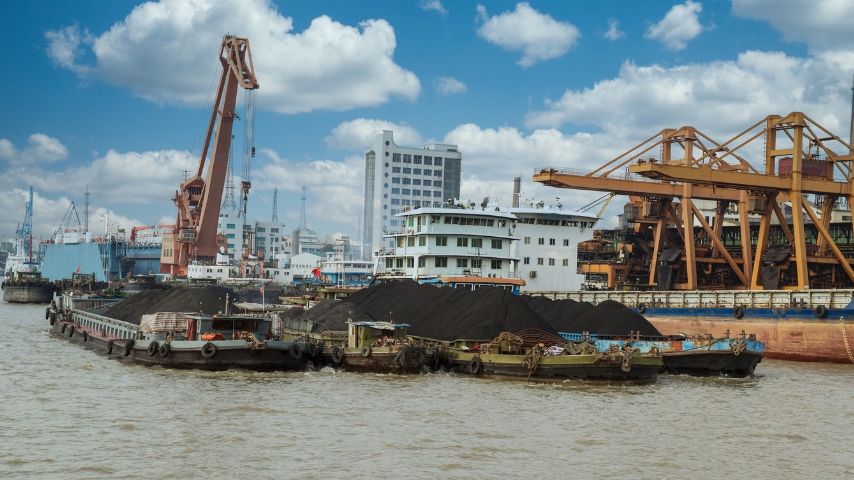
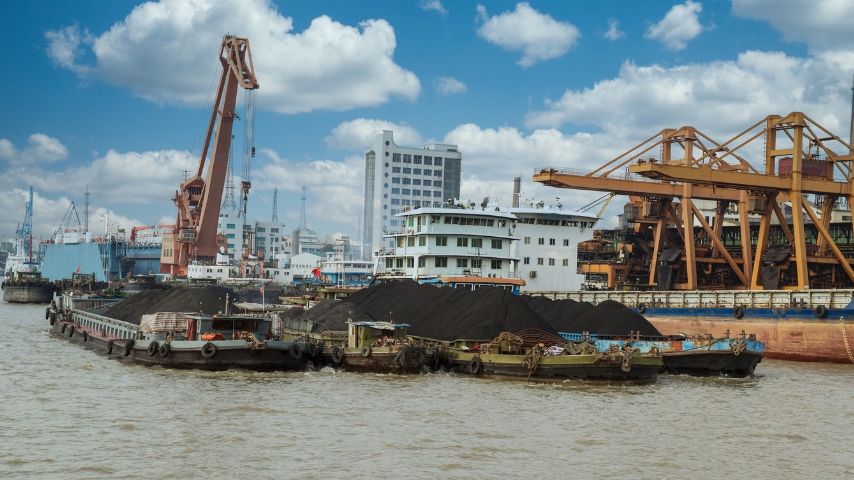
Despite the challenge payback is high for processes that recover rare earth minerals from end-of-life devices. Researchers are also examining other, less straightforward solutions.
Despite the challenges, recovering rare earth minerals from end-of-life devices such as hard disk drives (HDDs), electric vehicles, wind turbines, and advanced electronics happen across the globe because the payback is extremely high. HDDs, for example, contain rare earth elements including Neodymium (Nd), Praseodymium (Pr), and Dysprosium (Dy).
Growing world-wide instability has made the stakes even higher. Indeed, solutions are part of the call to action articulated by the 2024 National Defense Industrial Strategy’s objective that includes the expansion of domestic production of critical minerals and increase supply chain resilience. Yet, establishing an effective, energy efficient, and environmentally friendly circular economy to extract critical materials remains exceedingly difficult.
From mining extraction to the manufacturer of magnets, when it comes to rare earth materials, U.S. is behind China. This problem includes upstream (mining), midstream (refining and separation), and downstream (magnet-making and end-use product manufacturing). In fact, if the U.S. is serious about achieving rare earth independence, “It needs an industrial education renaissance,” Rare Earth Exchanges recently concluded.
With demand for these elements expected to grow by up to 600 percent over the next 10 to 20 years, developing sustainable ways to extract and recycle them has gotten urgent. As late as January of this year, the Department of Defense awarded more than $5 million to Rare Resource Recycling which targets the recovery of four elements critical to neodymium iron boron (NdFeB) magnets, which are used in numerous defense applications, including electric motors on major air platforms, missiles, submarines, and unpiloted vehicles.
Another effort is being made by Western Digital, Microsoft’s cloud data centers and materials recycling companies. The collaboration reported extracting rare earths from about 47,000 pounds of shredded end-of-life HDDs and other materials. PedalPoint Recycling sorted and processed the drives and eventually the elements are extracted by Critical Materials Recovery’s acid-free dissolution recycling whose pilot reached a 90 percent recovery rate for rare earths and base metals.
Meanwhile, researchers at the University of Texas at Austin have developed artificial membrane channels—tiny pores embedded in membranes—that mimic the selective transport mechanisms of transport proteins found in biological systems. Each channel is different, letting only ions with certain characteristics through while keeping others out. The researchers’ artificial channels use a modified version of a structure called pillararene to enhance their ability to bind and block specific common ions while transporting specific rare earth ions. The result is a system that can selectively transport middle rare earth elements, such as europium (Eu³⁺) and terbium (Tb³⁺).
Researchers are also looking at recovery and refining magnet-grade Nd, NdPr, and Dy at the source from coal and other mine waste. American Resources Corporation recently announced the development of a mobile unit that collects and produces leachate that ReElement Technologies then uses as a feedstock to be refined into ultra-pure rare earth products for domestic and allied-nation magnet manufacturers.
Other scientists are working to move away from rare earths entirely. The Cybertruck’s three-motor setup, for example, includes two induction motors and one permanent magnet motor. This configuration eliminates the need for rare earth materials. Also, back in 2022 Niron Magnetics, a startup out of the University of Minnesota, secured more than $17 million from the U.S. Department of Energy to scale up its work with sustainable permanent magnets that do not rely on rare earth minerals.
Despite such research the quickest way to clean energy is rare earth elements, reported the International Energy Agency (IEA). Unfortunately, there is only one mine in the U.S. that produces and processes rare earths. The Trump administration has brokered a deal with Ukraine that include access to rare earth minerals and it is also exploring joint rare earth metals projects with Russia. “Electric motors and generators driven by rare earth permanent magnets represent the most energy-efficient devices developed so far,” the IEA concluded in “Global Critical Minerals Outlook 2024.”
Cathy Cecere is membership content program manager.
Growing world-wide instability has made the stakes even higher. Indeed, solutions are part of the call to action articulated by the 2024 National Defense Industrial Strategy’s objective that includes the expansion of domestic production of critical minerals and increase supply chain resilience. Yet, establishing an effective, energy efficient, and environmentally friendly circular economy to extract critical materials remains exceedingly difficult.
From mining extraction to the manufacturer of magnets, when it comes to rare earth materials, U.S. is behind China. This problem includes upstream (mining), midstream (refining and separation), and downstream (magnet-making and end-use product manufacturing). In fact, if the U.S. is serious about achieving rare earth independence, “It needs an industrial education renaissance,” Rare Earth Exchanges recently concluded.
With demand for these elements expected to grow by up to 600 percent over the next 10 to 20 years, developing sustainable ways to extract and recycle them has gotten urgent. As late as January of this year, the Department of Defense awarded more than $5 million to Rare Resource Recycling which targets the recovery of four elements critical to neodymium iron boron (NdFeB) magnets, which are used in numerous defense applications, including electric motors on major air platforms, missiles, submarines, and unpiloted vehicles.
Another effort is being made by Western Digital, Microsoft’s cloud data centers and materials recycling companies. The collaboration reported extracting rare earths from about 47,000 pounds of shredded end-of-life HDDs and other materials. PedalPoint Recycling sorted and processed the drives and eventually the elements are extracted by Critical Materials Recovery’s acid-free dissolution recycling whose pilot reached a 90 percent recovery rate for rare earths and base metals.
Meanwhile, researchers at the University of Texas at Austin have developed artificial membrane channels—tiny pores embedded in membranes—that mimic the selective transport mechanisms of transport proteins found in biological systems. Each channel is different, letting only ions with certain characteristics through while keeping others out. The researchers’ artificial channels use a modified version of a structure called pillararene to enhance their ability to bind and block specific common ions while transporting specific rare earth ions. The result is a system that can selectively transport middle rare earth elements, such as europium (Eu³⁺) and terbium (Tb³⁺).
Researchers are also looking at recovery and refining magnet-grade Nd, NdPr, and Dy at the source from coal and other mine waste. American Resources Corporation recently announced the development of a mobile unit that collects and produces leachate that ReElement Technologies then uses as a feedstock to be refined into ultra-pure rare earth products for domestic and allied-nation magnet manufacturers.
Other scientists are working to move away from rare earths entirely. The Cybertruck’s three-motor setup, for example, includes two induction motors and one permanent magnet motor. This configuration eliminates the need for rare earth materials. Also, back in 2022 Niron Magnetics, a startup out of the University of Minnesota, secured more than $17 million from the U.S. Department of Energy to scale up its work with sustainable permanent magnets that do not rely on rare earth minerals.
Despite such research the quickest way to clean energy is rare earth elements, reported the International Energy Agency (IEA). Unfortunately, there is only one mine in the U.S. that produces and processes rare earths. The Trump administration has brokered a deal with Ukraine that include access to rare earth minerals and it is also exploring joint rare earth metals projects with Russia. “Electric motors and generators driven by rare earth permanent magnets represent the most energy-efficient devices developed so far,” the IEA concluded in “Global Critical Minerals Outlook 2024.”
Cathy Cecere is membership content program manager.