A Precast Masonry Arch Bridge that Lasts Centuries
A Precast Masonry Arch Bridge that Lasts Centuries
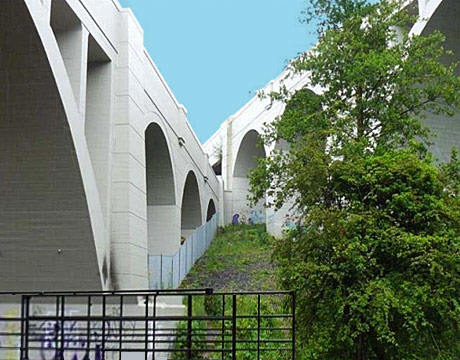
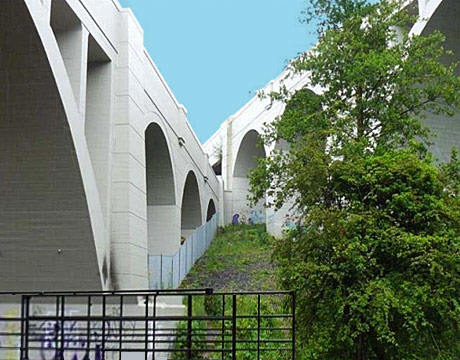
Newtownabbey Pathway Project. Image: Queen’s University, Belfast, UK
Masonry arch bridges are some of the most beautiful bridges in the world. This type of construction goes back to Roman days, and in fact, some of the surviving bridges are over 2,000 years old. Although they are strong, long-lasting, and aesthetically pleasing to the eye, traditional arch bridges are expensive and time-consuming to build. As a result, most arch bridges built since the 1970s have been constructed from steel-reinforced concrete arches and slabs, which are faster and cheaper to install.
The downside, however, is that steel-reinforced concrete corrodes—so much so that a masonry arch bridge that should last several hundred years starts to crumble after 40 or 50 if it is built with steel-reinforced concrete. Because of this rapid deterioration, engineers are looking more toward steel-free structures.
To improve on this situation, Adrian Long, a civil engineer at Queen’s University in Belfast, Ireland, challenged himself to develop a modern arch bridge system with all the attributes of an unreinforced masonry arch bridge, but that also can:
- Be installed as quickly as other types of bridges
- Eliminate the need for centering
- Use existing methods of design and analysis
- Be constructed off site using precast concrete methods
- Be cost-competitive with other types of bridges
After 10 years of research, Long perfected the “FlexiArch” bridge system in 2007. Because the main forces are compressive, no reinforcing steel is required. No centering is needed, and the bridge can be assembled in a day. Because there is no corrosion, the bridge is expected to last at least 300 years with minimal long-term maintenance, adding to its cost-competitiveness with other types of bridges.
How It Works
Precast voussoirs are laid side by side with a layer of polymeric reinforcement placed on top. This surface is then overlain with a 40-mm layer of fine aggregate concrete (screed) that hardens, assuring the voussoirs are interconnected.
“The FlexiArch units can be cast in convenient widths to suit the design requirements, site restrictions, and available lifting capacity,” says Long. “When lifted at the designated anchorage points, gravity forces cause the wedge-shaped gaps to close. Concrete hinges form in the screed and the integrity of the unit is provided by tension in the polymeric reinforcement and the shear resistance of the screed.”
Long notes that the degree of taper of the voussoirs controls the geometry of the arch: flatter arches require less taper, for example. The arch-shaped units are then lifted and placed on precast footings at the bridge site, “with all the self-weight then transferred from tension in the polymeric reinforcement to compression in the voussoirs, acting the same way a conventional masonry arch does,” Long adds.
The polymeric reinforcement provides the tensile strength needed to lift the FlexiArch units safely. Lab tests that simulated the bridge-site conditions were undertaken to test the strength of the polymeric reinforcement. “Using these results and taking into account creep effects, an appropriate load factor was applied to ensure there was no risk of failure during lifting,” adds Long. “A typical unit can be accurately located on-site every 15 minutes, therefore, most bridges can be installed in well under a day.”
A wide range of static loading tests were also carried out to validate the performance of the system. These have included model tests in the laboratory (at fifth, quarter and third scale) with granular or concrete backfill where it was possible to achieve the ultimate capacity. Full-scale tests under maximum loads (equivalent wheel load of 320 kN, or lane loading of over 1,000 kN) also showed the bridge system more than satisfied the stringent requirements for highway bridges.
Moving Forward
To date, more than 50 of these bridges have been built in the UK and Ireland, and discussions are in progress with several U.S. companies. Span lengths can reach 30 meters.
“By interconnecting the accurately precast voussoirs via a screed and polymeric reinforcement, arches can be produced to the precision required by designers without the need for centering,” says Long. “The speed of installation is comparable with precast concrete/steel beams. As such, it can be used for road bridges over railway lines where construction windows are restrictive. As there is no corrodible reinforcement, total life cycle costs are therefore minimal.”
Mark Crawford is an independent writer.
The arch-shaped units are then lifted and placed on precast footings at the bridge site, with all the self-weight then transferred from tension in the polymeric reinforcement to compression in the voussoirs—acting the same way a conventional masonry arch does. Adrian Long, civil engineer, Queen’s University
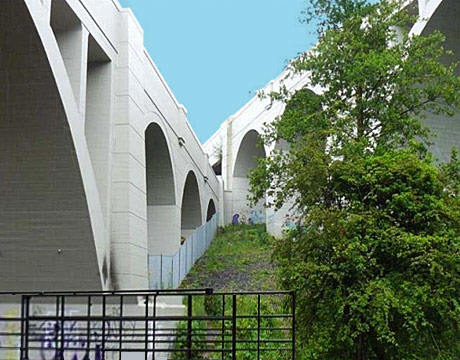
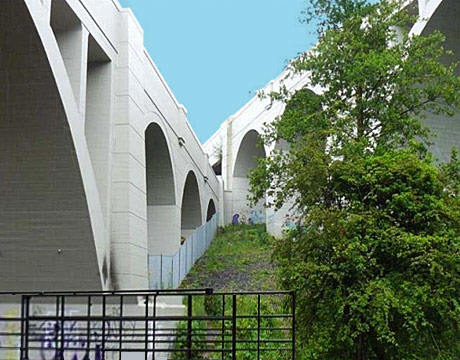