New Compressor Makes Fuel Cell Aircraft Viable
New Compressor Makes Fuel Cell Aircraft Viable
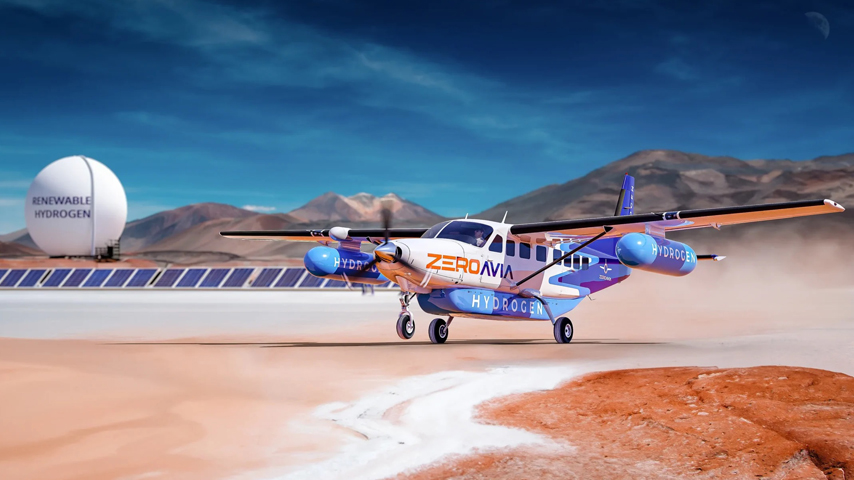
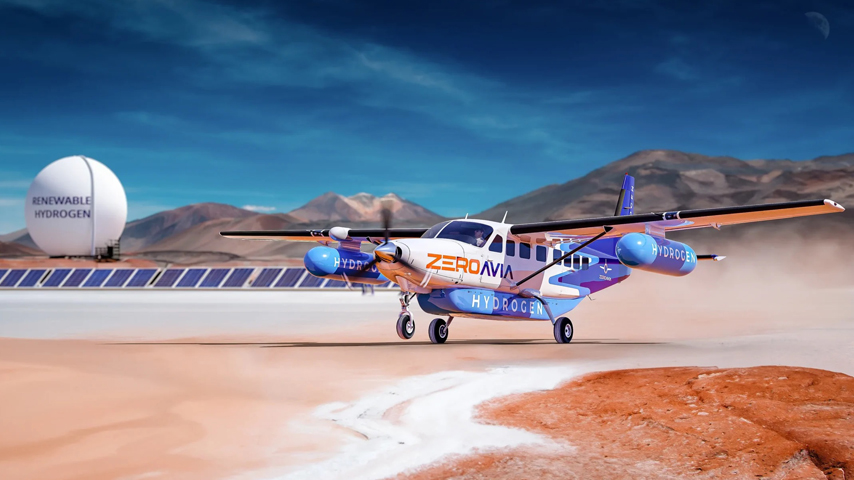
World’s first high performance compressor for hydrogen fuel cell aviation powertrains would enable several stacks to operate with a single compressor.
Green aviation has been a focus of the aircraft industry for the past several years, but taking the carbon out of flying is easier said than done. Batteries—the popular choice for cars—are heavy and not terribly energy dense, while hydrogen fuel cells have been plagued with complications.
An announcement from Anglo-American startup ZeroAvia may tip the scales toward hydrogen: The company said it has developed the world’s first high performance compressor for hydrogen fuel cell aviation powertrains. The technology would enable a bank of fuel cells to operate with a single compressor rather than many, saving weight.
A fuel cell uses hydrogen to produce electricity by separating the proton and electron of a hydrogen atom on one side of a membrane and recombining them on the other. While the protons pass through the membrane, the electrons run through an external circuit to power devices. A catalyst on the cathode side combines protons and electrons with oxygen atoms to produce water and heat.
“All hydrogen fuel cells need a compressor of some kind to increase the pressure of the air going into the fuel cell and help with the electric chemical reaction,” said Rudolf Coertze, head of research and development at ZeroAvia. “The higher-pressure air enhances the performance of the fuel cells themselves.”
To generate enough electricity to operate an aircraft, the ZeroAvia system stacks several fuel cells together. The fuel cells operate in unison to increase the electrical power generated. A silicon carbide inverter converts DC power generated by the fuel cell to AC power when required.
ZeroAvia designed its hydrogen fuel cell system with a single compressor to provide oxygen to all the stacks. Traditional fuel cell systems have separate compressors for each stack—powered independent from the propulsion motor—requiring additional motors, inverters, and power electronics. By combining all the fuel cell stacks to one compressor and running this compressor from the main propulsion motor, the system architecture is optimized and reduces both weight and complexity.
ASME Membership Is For You
To further reduce weight, ZeroAvia does not rely on high voltage batteries, similar to those in an electric car. However, onboard electronics require a low voltage battery to provide power for redundancy and safety.
The system stores hydrogen in pressurized tanks in the plane’s cargo pod and wings. The ZA600 fuel cell, expected to deploy in 2025, can produce up to 750 kW of continuous power over 300 nautical miles, enough to power turboprop planes such as the Cessna Grand Caravan. The ZA2000 fuel cell can produce up to 5 MW of continuous power over 1,000 nautical miles, enough for an 80-passenger plane.
The company sees its fuel cells as a retrofit to replace conventional aircraft propulsion systems.
“For a pilot licensed to operate a Cessna Caravan for example, the hydrogen fuel cell retrofitted powertrain will have some differences with the man-machine interface in the cockpit, instrumentation, and how the plane will handle, when compared to a traditional turbine engine,” Coertze said.
ASME B31.12 Code for Hydrogen Piping
The fuel cell electric motor is quieter than traditional turbines, but propeller noise, which is usually heard over the engine noise, would still be present.
The ZeroAvia compressor was designed with aircraft certification in mind. With the ZA600 being the first hydrogen fuel cell powertrain for aircraft, ZeroAvia reviewed existing standards for turbine engines and worked with certification authorities to ensure they understood the requirements for new technology. While more work is required before large aircraft outfitted with hydrogen fuel cells can complete long haul flights, significant progress has been made in design development and proof of concept.
Nicole Imeson is a technology writer in Calgary, Alta.
An announcement from Anglo-American startup ZeroAvia may tip the scales toward hydrogen: The company said it has developed the world’s first high performance compressor for hydrogen fuel cell aviation powertrains. The technology would enable a bank of fuel cells to operate with a single compressor rather than many, saving weight.
A fuel cell uses hydrogen to produce electricity by separating the proton and electron of a hydrogen atom on one side of a membrane and recombining them on the other. While the protons pass through the membrane, the electrons run through an external circuit to power devices. A catalyst on the cathode side combines protons and electrons with oxygen atoms to produce water and heat.
“All hydrogen fuel cells need a compressor of some kind to increase the pressure of the air going into the fuel cell and help with the electric chemical reaction,” said Rudolf Coertze, head of research and development at ZeroAvia. “The higher-pressure air enhances the performance of the fuel cells themselves.”
To generate enough electricity to operate an aircraft, the ZeroAvia system stacks several fuel cells together. The fuel cells operate in unison to increase the electrical power generated. A silicon carbide inverter converts DC power generated by the fuel cell to AC power when required.
ZeroAvia designed its hydrogen fuel cell system with a single compressor to provide oxygen to all the stacks. Traditional fuel cell systems have separate compressors for each stack—powered independent from the propulsion motor—requiring additional motors, inverters, and power electronics. By combining all the fuel cell stacks to one compressor and running this compressor from the main propulsion motor, the system architecture is optimized and reduces both weight and complexity.
ASME Membership Is For You
To further reduce weight, ZeroAvia does not rely on high voltage batteries, similar to those in an electric car. However, onboard electronics require a low voltage battery to provide power for redundancy and safety.
The system stores hydrogen in pressurized tanks in the plane’s cargo pod and wings. The ZA600 fuel cell, expected to deploy in 2025, can produce up to 750 kW of continuous power over 300 nautical miles, enough to power turboprop planes such as the Cessna Grand Caravan. The ZA2000 fuel cell can produce up to 5 MW of continuous power over 1,000 nautical miles, enough for an 80-passenger plane.
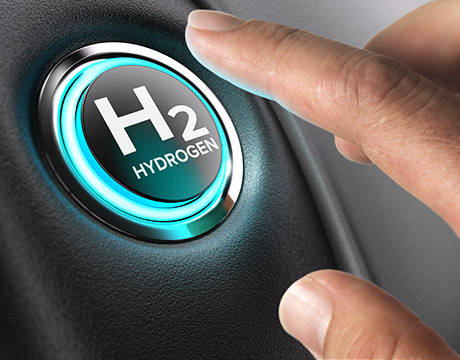
Clean Hydrogen
ASME plays a vital role in supporting the production, transport, and use of hydrogen.
The company sees its fuel cells as a retrofit to replace conventional aircraft propulsion systems.
“For a pilot licensed to operate a Cessna Caravan for example, the hydrogen fuel cell retrofitted powertrain will have some differences with the man-machine interface in the cockpit, instrumentation, and how the plane will handle, when compared to a traditional turbine engine,” Coertze said.
ASME B31.12 Code for Hydrogen Piping
The fuel cell electric motor is quieter than traditional turbines, but propeller noise, which is usually heard over the engine noise, would still be present.
The ZeroAvia compressor was designed with aircraft certification in mind. With the ZA600 being the first hydrogen fuel cell powertrain for aircraft, ZeroAvia reviewed existing standards for turbine engines and worked with certification authorities to ensure they understood the requirements for new technology. While more work is required before large aircraft outfitted with hydrogen fuel cells can complete long haul flights, significant progress has been made in design development and proof of concept.
Nicole Imeson is a technology writer in Calgary, Alta.
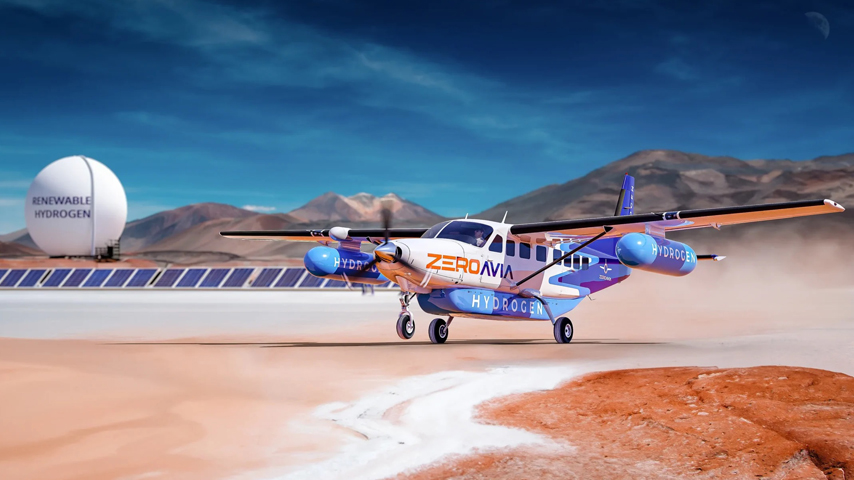
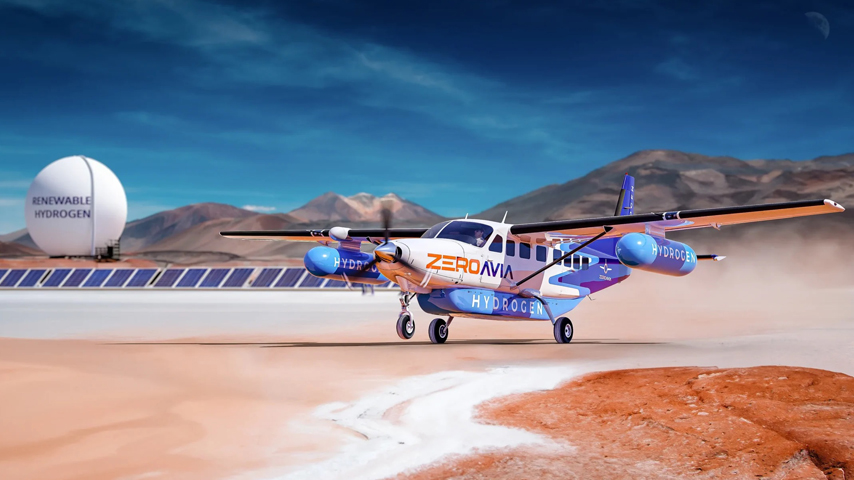