Manufacturing Blog: Software Can Help Identify Additive Manufacturing Prospects
Manufacturing Blog: Software Can Help Identify Additive Manufacturing Prospects
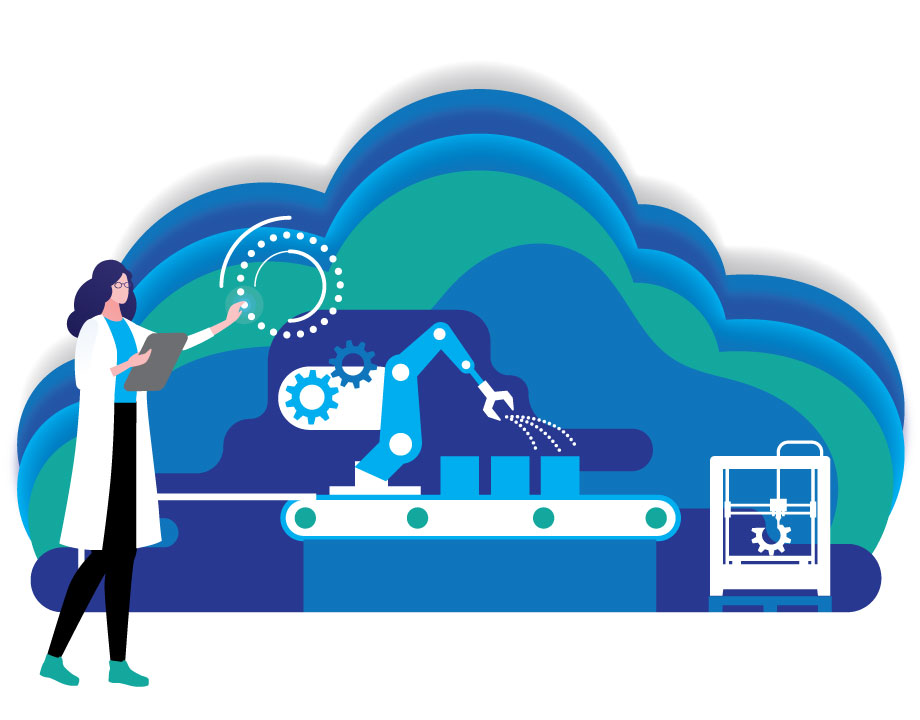
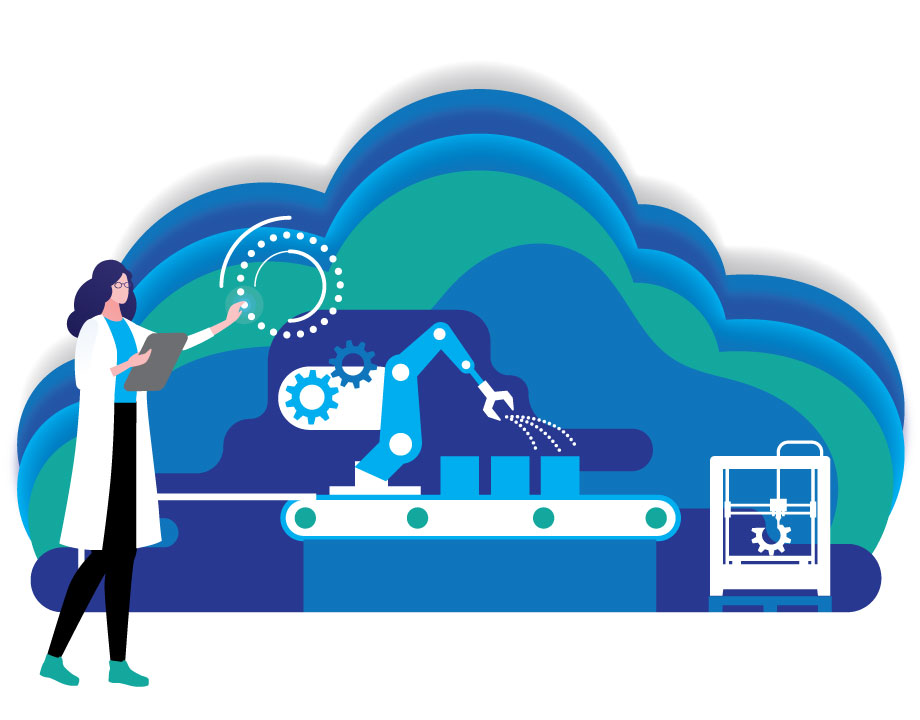
Knowing if a component or assembly is a good candidate for AM opens the door to new opportunities.
Knowing whether a component or assembly is a good candidate for AM opens the door to new opportunities.
Even hardened veterans can stumble on a long-existing barrier when the opportunity arises to use a manufacturing process with which they have little experience. That issue is identifying which parts good candidates for fabricating via a given process.
The good news for additive manufacturing (AM) is that part identification solutions have emerged. And a strong software tool can not only identify candidates but also advise on beneficial alterations while comparing cost and time to other AM solutions and traditional manufacturing methods.
Without the intelligent guidance of a software algorithms, many are trapped in a variation on the hammer and nail adage. If the only tool you know is a hammer, all candidates must look like nails for you to consider pulling the hammer out of the toolbox. This kind of unfamiliarity with AM will lead to missed opportunities, poorly selected projects, and non-ideal designs.
More for You: Ceramic Materials Advance Climate Change Efforts
This is true for AM as an alternative to molding, machining, casting, and forming. The challenge is even greater when it comes time to select a specific AM process.
To counter the challenges, software for part identification, design optimization and cost comparison has emerged. Historically, these tools were either the intellectual property of service organizations that offered a wide array of manufacturing solutions or they were limited to basic considerations of part size and desired material class. Today, the software is more intelligent, more capable, and available to use without reaching out to a service provider.
Admittedly, it is still early days for what can be done, but advancements will transpire as the software continues to mature and the algorithms are fed by more comprehensive data sets. Yet, the software can help you to conquer AM applications today.
For starters, it will report if a part (or an entire assembly) is appropriate for AM. That evaluation considers part design, at the feature level, and the all-important element of cost. If a component has some objectionable characteristics, a capable software solution will also advise of possible changes that can convert it into a good candidate. To round out the solution, guidance for design modification, such as where to reduce mass or how to consolidate parts, is part of the analysis.
Reader’s Choice: Which New Materials are Popular in 3D Printing?
But as Ron Popeil was famous for saying, wait, there’s more: Point the software at an archive of parts, and it can root through years of designs to extract those that you should consider for AM. There are even early efforts to make that possible when all that exists is 2D documentation. You are sitting on years of designs that AM part identification software can expose as viable opportunities, which is ideal when tackling legacy products or building out an AM spares program.
These software solutions give you a strong start by removing part identification and optimization blind spots. Doing so opens the door to more AM opportunities. But they won’t take you across the finish line. For that, you will need to develop expertise at the system level and in the business case realm.
While you will be provided a green light for AM, recommendations for process classes and specific processes tend to be generalizations. This is not a software problem; it is a data issue. A deep, rich data archive does not exist with the vast array of AM solutions and numerous user-defined controls. Over time, that data will become increasingly available, perhaps fueled by machine learning, but at present, you will only receive rough guidance.
The most impactful gap, both in the software and in users experience bases, is the challenge of building the business case. Although cost is a component of the justification, and the software can provide this, a sound business case goes well beyond part cost. To green-light an intended project, you must prove that AM offers benefits that are unmatched by your conventional solutions. For that, you can’t rely on a software solution. After the software provides the answer to “Can we?” it is up to you and your team to answer the question, “Should we?”
Todd Grimm is president of T.A. Grimm & Associates, an additive manufacturing consulting and communications company, and a 30-year industry veteran.
Even hardened veterans can stumble on a long-existing barrier when the opportunity arises to use a manufacturing process with which they have little experience. That issue is identifying which parts good candidates for fabricating via a given process.
The good news for additive manufacturing (AM) is that part identification solutions have emerged. And a strong software tool can not only identify candidates but also advise on beneficial alterations while comparing cost and time to other AM solutions and traditional manufacturing methods.
Without the intelligent guidance of a software algorithms, many are trapped in a variation on the hammer and nail adage. If the only tool you know is a hammer, all candidates must look like nails for you to consider pulling the hammer out of the toolbox. This kind of unfamiliarity with AM will lead to missed opportunities, poorly selected projects, and non-ideal designs.
More for You: Ceramic Materials Advance Climate Change Efforts
This is true for AM as an alternative to molding, machining, casting, and forming. The challenge is even greater when it comes time to select a specific AM process.
To counter the challenges, software for part identification, design optimization and cost comparison has emerged. Historically, these tools were either the intellectual property of service organizations that offered a wide array of manufacturing solutions or they were limited to basic considerations of part size and desired material class. Today, the software is more intelligent, more capable, and available to use without reaching out to a service provider.
Admittedly, it is still early days for what can be done, but advancements will transpire as the software continues to mature and the algorithms are fed by more comprehensive data sets. Yet, the software can help you to conquer AM applications today.
For starters, it will report if a part (or an entire assembly) is appropriate for AM. That evaluation considers part design, at the feature level, and the all-important element of cost. If a component has some objectionable characteristics, a capable software solution will also advise of possible changes that can convert it into a good candidate. To round out the solution, guidance for design modification, such as where to reduce mass or how to consolidate parts, is part of the analysis.
Reader’s Choice: Which New Materials are Popular in 3D Printing?
But as Ron Popeil was famous for saying, wait, there’s more: Point the software at an archive of parts, and it can root through years of designs to extract those that you should consider for AM. There are even early efforts to make that possible when all that exists is 2D documentation. You are sitting on years of designs that AM part identification software can expose as viable opportunities, which is ideal when tackling legacy products or building out an AM spares program.
These software solutions give you a strong start by removing part identification and optimization blind spots. Doing so opens the door to more AM opportunities. But they won’t take you across the finish line. For that, you will need to develop expertise at the system level and in the business case realm.
While you will be provided a green light for AM, recommendations for process classes and specific processes tend to be generalizations. This is not a software problem; it is a data issue. A deep, rich data archive does not exist with the vast array of AM solutions and numerous user-defined controls. Over time, that data will become increasingly available, perhaps fueled by machine learning, but at present, you will only receive rough guidance.
The most impactful gap, both in the software and in users experience bases, is the challenge of building the business case. Although cost is a component of the justification, and the software can provide this, a sound business case goes well beyond part cost. To green-light an intended project, you must prove that AM offers benefits that are unmatched by your conventional solutions. For that, you can’t rely on a software solution. After the software provides the answer to “Can we?” it is up to you and your team to answer the question, “Should we?”
Todd Grimm is president of T.A. Grimm & Associates, an additive manufacturing consulting and communications company, and a 30-year industry veteran.