Injecting Medicine in Zero Gravity
Injecting Medicine in Zero Gravity
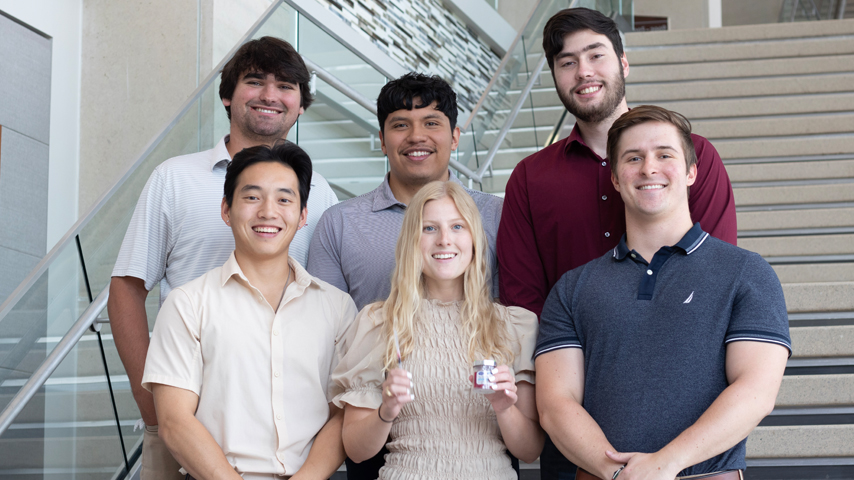
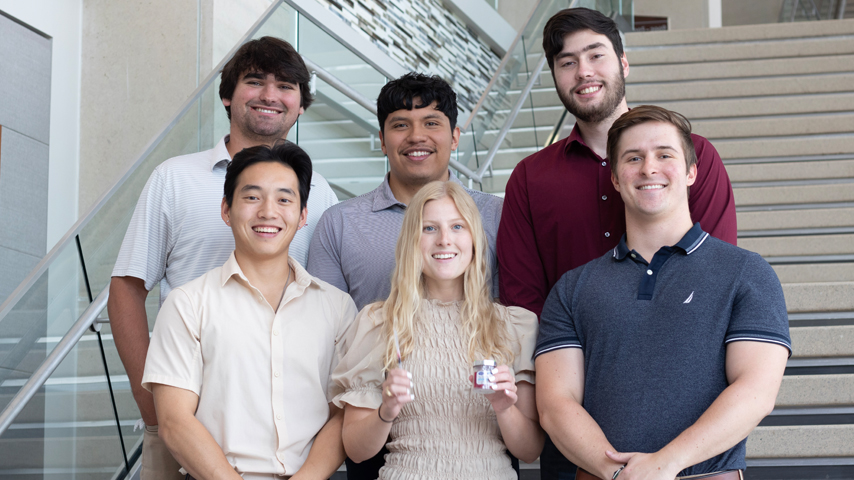
Texas A&M engineering students devised a syringe vial that separates bubbles from liquid and can be used in zero gravity.
A vertical needle, with the point fixed on the ceiling, and a thumb pressing on the syringe’s plunger to eject the medicine is the classic move health care workers perform before sticking the needle into a patient. It’s not done just to heighten the drama of the jab, of course, but to remove air from the syringe. And the tactic is effective thanks to the power of gravity.
In space, it doesn’t work at all. Where there’s no gravity, a vial will have gas bubbles distributed evenly through whatever medication it contains and there’s no easy way to quickly remove them. Thankfully, no one on the space station has yet needed an emergency shot. But to prepare for such an event a group of engineering students in Texas A&M’s Department of Biomedical Engineering have created a zero-g-proof vial that will keep the bubbles at bay.
The students were brainstorming what to pursue for their capstone project when they looked at a list of problems withwhich NASA needed help. “Our team selected five problems,” said team member Simon Herz. “Then we down-selected from there to try to see what was most feasible to do within our year time frame. And we ended up looking at was called ‘novel medication storage for space.’ ”
As it happened, another teammate, Evan Pettit, was the son of astronaut Donald Pettit, whose accomplishments include the invention of the zero-g coffee mug, also known as the Capillary Cup.
"When I was a kid he developed that coffee cup and I remember hearing a lot about it at home,” said the younger Pettit. In speaking with people at NASA, he learned about the extent of the medication-in-space problem.
"If you're conducting research with liquid medication, or—God forbid—you need to use that liquid medication in an emergency scenario where an astronaut's life is on the line, and it’s very mission-critical, you need something to mitigate these issues that come with it. That's when the idea clicked: ‘Hey, I know a way to utilize this open container design to conform this liquid into a uniform volume just through my years of exposure to my father's design.’”
Become a Member: How to Join ASME
The airfoil shape of Donald Pettit’s mug forced coffee or another liquid to one corner where it could be sipped without a slurping war. Minus gravity, the capillary power of the mug’s walls acting on the liquid becomes the dominant force. When the coffee goes to one side, air goes to the other.
The team of Texas A&M students decided to put the same phenomenon, and the same shape, to use in their vial. “We just took that shape, and put it on a much smaller scale,” said Herz. “So instead of half a liter volume, we made it just three to five milliliters, which is just enough for like a single-dose medication.”
More for You: 3D-Printed Turbine Parts Withstand High Temperatures
Having borrowed the shape from NASA’s coffee cup, the chief challenge became finding the right material. “We wanted to find a good material, that was clear enough. We wanted individuals to be able to see inside but still have radiation protection properties,” said Herz. “Because in space you’re exposed to a lot of a lot of background radiation and that can really deteriorate your medication.” In the end, they chose polystyrene, which has all those properties and is inexpensive.
To better keep things sterile, an issue of paramount importance in space, they also decided to make a vial of five small chambers rather than a larger one that could be drawn from multiple times. After a single compartment of medication is sucked up by a syringe, the user can peel away a sticker to show that it’s been used.
The team was able to subject their vial to radiation and degradation testing at the university, but to really put it through its paces, it needs to be tested in space or someplace like it. That might mean convincing NASA to 3D-print the vial on the International Space Station or seeing how it works in a drop test tower or on a reduced-gravity aircraft.
"Whatever company or organization you’re pitching this to needs to know, at mission-critical time, that it will succeed,” Pettit said
But first, the team needs to patent the idea. “Of course, it costs $10,000 to patent something, and we’re just a team of students,” Herz said. “So we’re trying to find someone who could help us out with that."
Michael Abrams is a science and technology writer in Westfield, N.J.
In space, it doesn’t work at all. Where there’s no gravity, a vial will have gas bubbles distributed evenly through whatever medication it contains and there’s no easy way to quickly remove them. Thankfully, no one on the space station has yet needed an emergency shot. But to prepare for such an event a group of engineering students in Texas A&M’s Department of Biomedical Engineering have created a zero-g-proof vial that will keep the bubbles at bay.
The students were brainstorming what to pursue for their capstone project when they looked at a list of problems withwhich NASA needed help. “Our team selected five problems,” said team member Simon Herz. “Then we down-selected from there to try to see what was most feasible to do within our year time frame. And we ended up looking at was called ‘novel medication storage for space.’ ”
As it happened, another teammate, Evan Pettit, was the son of astronaut Donald Pettit, whose accomplishments include the invention of the zero-g coffee mug, also known as the Capillary Cup.
"When I was a kid he developed that coffee cup and I remember hearing a lot about it at home,” said the younger Pettit. In speaking with people at NASA, he learned about the extent of the medication-in-space problem.
"If you're conducting research with liquid medication, or—God forbid—you need to use that liquid medication in an emergency scenario where an astronaut's life is on the line, and it’s very mission-critical, you need something to mitigate these issues that come with it. That's when the idea clicked: ‘Hey, I know a way to utilize this open container design to conform this liquid into a uniform volume just through my years of exposure to my father's design.’”
Become a Member: How to Join ASME
The airfoil shape of Donald Pettit’s mug forced coffee or another liquid to one corner where it could be sipped without a slurping war. Minus gravity, the capillary power of the mug’s walls acting on the liquid becomes the dominant force. When the coffee goes to one side, air goes to the other.
The team of Texas A&M students decided to put the same phenomenon, and the same shape, to use in their vial. “We just took that shape, and put it on a much smaller scale,” said Herz. “So instead of half a liter volume, we made it just three to five milliliters, which is just enough for like a single-dose medication.”
More for You: 3D-Printed Turbine Parts Withstand High Temperatures
Having borrowed the shape from NASA’s coffee cup, the chief challenge became finding the right material. “We wanted to find a good material, that was clear enough. We wanted individuals to be able to see inside but still have radiation protection properties,” said Herz. “Because in space you’re exposed to a lot of a lot of background radiation and that can really deteriorate your medication.” In the end, they chose polystyrene, which has all those properties and is inexpensive.
To better keep things sterile, an issue of paramount importance in space, they also decided to make a vial of five small chambers rather than a larger one that could be drawn from multiple times. After a single compartment of medication is sucked up by a syringe, the user can peel away a sticker to show that it’s been used.
The team was able to subject their vial to radiation and degradation testing at the university, but to really put it through its paces, it needs to be tested in space or someplace like it. That might mean convincing NASA to 3D-print the vial on the International Space Station or seeing how it works in a drop test tower or on a reduced-gravity aircraft.
"Whatever company or organization you’re pitching this to needs to know, at mission-critical time, that it will succeed,” Pettit said
But first, the team needs to patent the idea. “Of course, it costs $10,000 to patent something, and we’re just a team of students,” Herz said. “So we’re trying to find someone who could help us out with that."
Michael Abrams is a science and technology writer in Westfield, N.J.
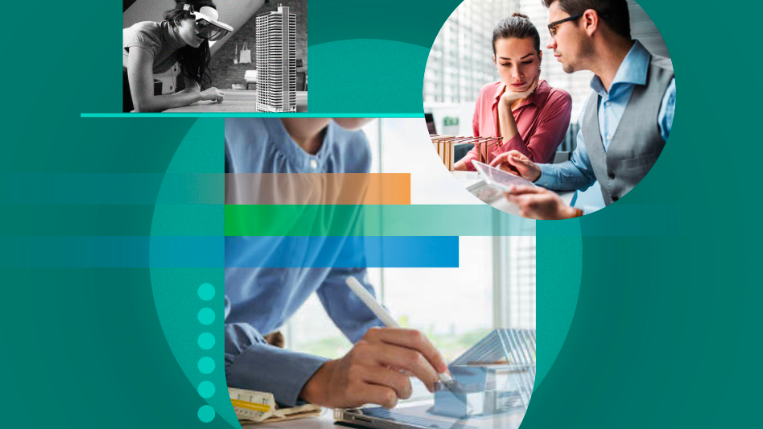
Pulse of the Profession: CAD in 2030
CAD technologies and their applications are rising in tandem with trends in Industry 4.0.
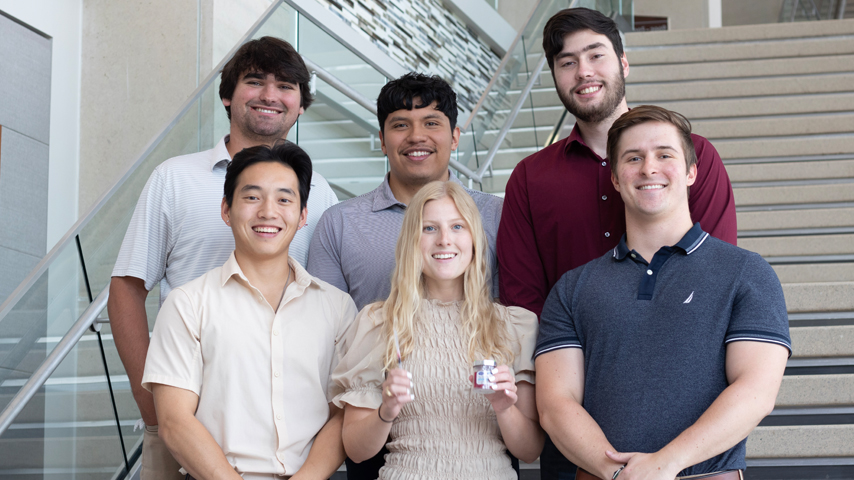
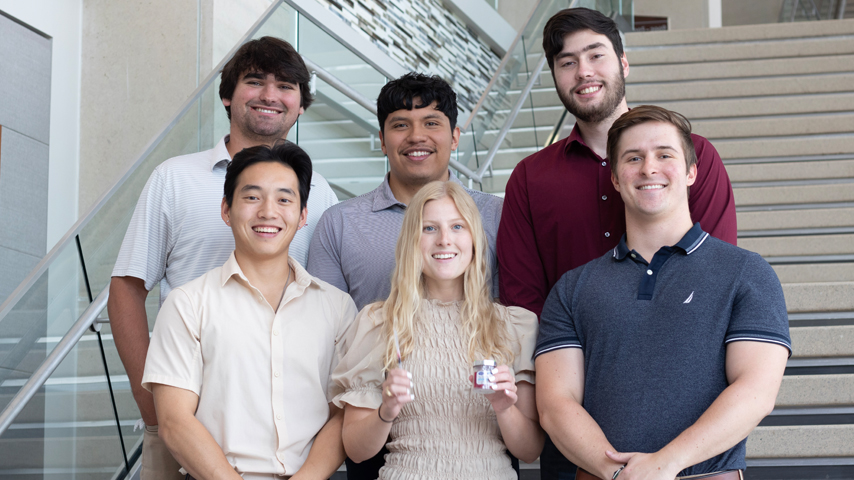