How to Select High Bond Tapes for Modern Device Displays
How to Select High Bond Tapes for Modern Device Displays
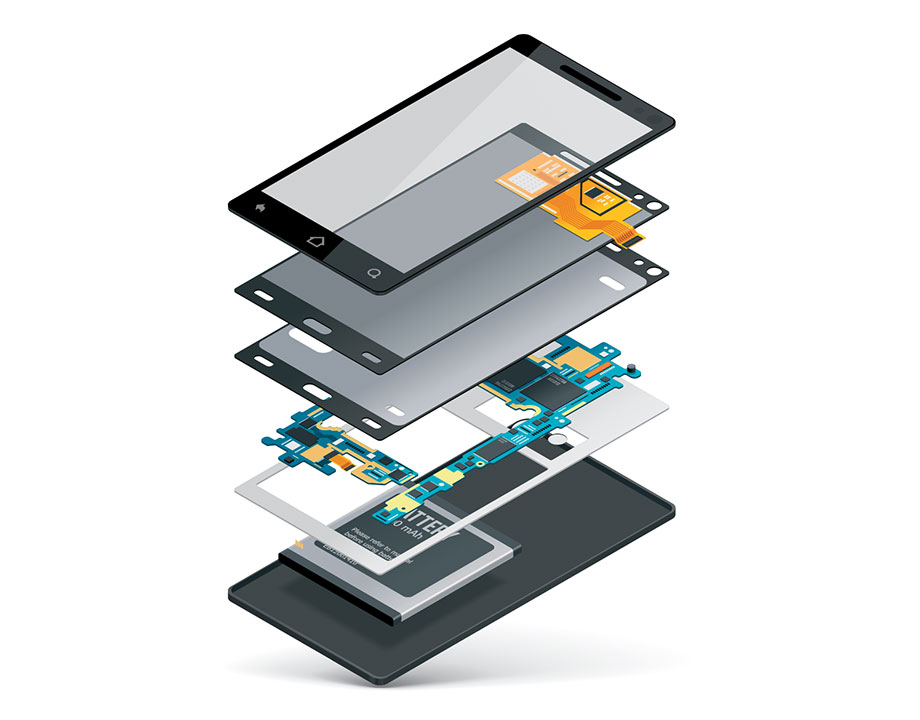
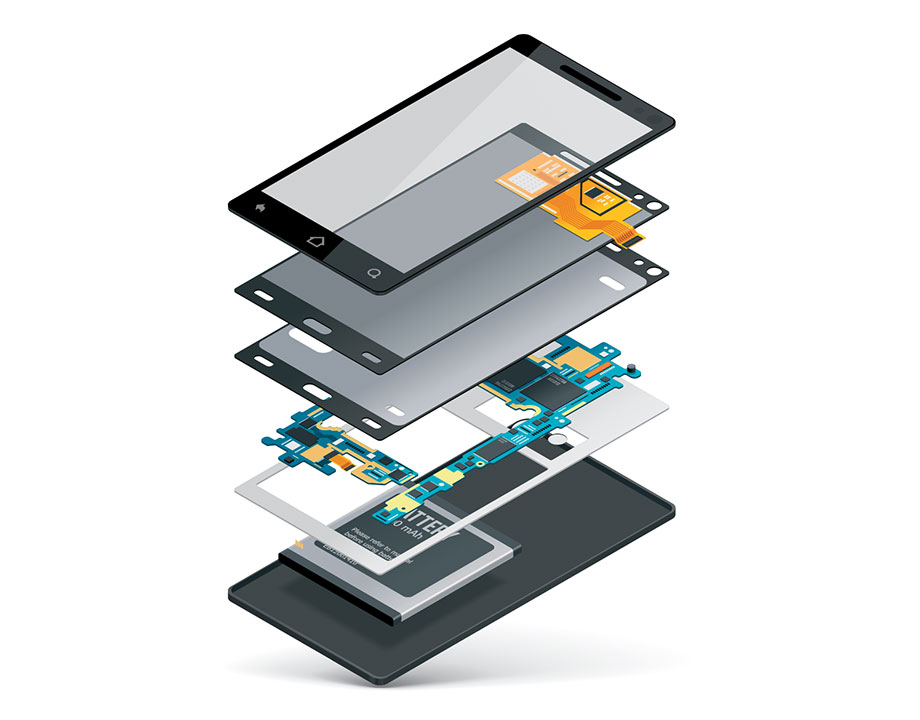
Explore how high bond tapes are used in modern display devices to seal out moisture, provide impact and vibration resistance, and maintain optical clarity.
Display technologies are evolving as more and more applications utilize clearer, better-performing displays, touchscreen, and human-machine interfaces (HIMs). Current trends include integrating high-end components and sensors, durability enhancements, edge-to-edge display technologies, and device miniaturization. Effective product launch of these modern display technologies reflects the assembly as a whole, and bezel bonding and display gasket materials must be selected based on application performance requirements to meet design specifications.
High bond tapes address the demands of a wide range of bezel bonding and display gasket applications. These high-strength, double-sided acrylic foam tapes are formulated to achieve application-specific characteristics. Still, they can also carry complications along to the converting process due to die-cut dimensions and narrow bond lines. Softer tapes can be challenging for rotary die-cutting processes. To obtain a die-cut integrated display gasket solution that adheres to required tolerances, original equipment manufacturers require a solutions provider with advanced converting capabilities.
High-strength, double-sided acrylic foam bond tapes are high-performance adhesives, and each tape is formulated to achieve a balance of properties that address specific performance requirements.
For example:
Applied stress is distributed evenly across the entire bond area, limiting the amount of force that gets exerted on display components. This acts to protect the electronic display. The closed-cell foam structure seals out contaminants, moisture, and solvents. These tapes are available with highly conformable and firm adhesive foam cores, acrylic and modified acrylic adhesives, and serval different release liners in a rand of thickness and colors.
An example of high-performance bond tape is the 3M™ VHB™ Tape 59xx Series that encompasses a wide range of high-performance bonding tapes that work with most bezel bonding and display gasket applications. These tapes are available in a thickness range from 150 µm to 1.6 mm. They are supplied with a modified acrylic adhesive on both sides of a very conformable adhesive foam core, providing good adhesion to the widest range of substrates, including most powder-coated paints and many plastics. These are the go-to tapes for most electronic display bonding applications.
Learn More: Advanced Thermal Interface Materials for Electronic Assemblies
Designed for longevity, very high bond tapes are selected based on design criteria, including display size, weight, bond width, the position of the display, and thickness. Proper selection of materials ensures a durable, long-lasting bond.
Tape thickness is selected based on the size and rigidity of the bonded substrates and their flatness. Thicker tapes provide an improved bond strength when mating irregular and larger surfaces. Rigid substrates with normal flatness are best handled by a tape thickness of 1.1 mm or greater, while flexible and flatter surfaces are most suitable for thinner tapes.
The durability of the bond tape is a function of design proportions. Due to their viscoelastic nature, care should be taken to specify an adequate amount of tape for bonding applications. To best avoid creep and premature failure, 4x2 inch pieces of tape should be used for every 1 lb. of weight supported under static loads.
As a rule of thumb, firm core tapes are most suitable for addressing flat substrates, while larger and curved displays are best suited for softer conformable core tapes. The softer conformable adhesive cores also provide enhanced impact resistance and have become the go-to products for most mobile electronics applications.
Recommended for You: Adding Textures to Touchscreens
Many display technologies and other engineered materials require integration into multi-functional stack-ups. They use advanced converting and manufacturing capabilities for one-shot multi-functional components, including integrated display gaskets and bezel bonding solutions, where local secondary applications are optimized by including in the original design. During this process, pull close proximity die cuts into the bezel solution for a one-pass, multi-layered, multi-solution deliverable, such as a microphone or speaker gaskets, display ring tape, spacers, and dampers. These multi-functional components are produced in a cleanroom environment and assembled via segmented frame technology, capabilities that enable contaminant and particulate-free, ultra-tight tolerance die-cut components at the lowest cost possible.
Optically Clear Adhesives (OCAs) are highly transparent adhesives used to bond visually clear components into an optically clear lamination without bubbles or distortion. OCAs laminate transparent materials and layers together, enabling complex optically clear assemblies to transmit as much light as possible through optimal refraction and refractive index matching. Optimizing the refractive index of laminated display components improves contrast ratio and optical clarity while reducing reflected light. This enhances the viewability, vivacity, clarity, and readability of LCD, LED, and OLED screens. OCAs create a differentiated automotive display experience with improved safety.
These adhesives are used specifically for their superior optical and mechanical attachment qualities. Optically Clear Adhesives have high dimensional stability, low shrinkage, and resist whitening over time. Integrating layers with the right OCAs enable rugged, long-lasting bonds in complex optically clear laminations. OCAs come in various formulations to accommodate a broad array of applications but are typically composed of acrylic, polyvinyl acetate (PVA), polyurethane (PU), silicone, or epoxy. The optical transparency of OCAs and application directly between the display and the user’s field of vision mean that they must be coated, handled, and fabricated with zero defects or visual flaws. It’s recommended to handle, fabricate, and assemble OCAs in high cleanliness environments certified to Class 100.
OCAs also offer ingress protection and reduce the width required for bezels to maximize screen space, better waterproof the display, protect it against contaminants, and create a more immersive display experience. OCAs are often utilized with bezel bonding techniques and integrated display gaskets for high performance, ultra-tight tolerance, streamlined touch display mounts.
Display technologies utilize sheet-type optically clear adhesives (OCA) when bonding visually clear components, such as touch screens, graphic overlays, and polymeric film glass laminates. Sheet-type OCA addresses inherent limitations that can affect screen brightness, contrast ratio, and the durability of these die-cut integrated display gasket solutions.
Sheet-type OCA is a superior alternative to optically clear resins (OCR) or liquid OCA (LOCA). Liquid adhesives are applied in a fishbone pattern prior to lamination and a UV curing process. These adhesives are prone to leakage, and users may experience uneven curing defects that can affect product quality and yield rates.
Light transmittance also decays as incremental materials are stacked upon each other. To eliminate any amount of light reflection or refraction, apply an adhesive of uniform thickness with a refractive index closely matched to mating components between each medium.
The integrated die-cut components are assembled with a sheet-type OCA with a refractive index between 1.4 and 1.5, close to that of display films, filters, or even touch panels. OCAs are dimensionally stable, exhibit low shrinkage, resist whitening and reduce any amount of reflection between each substrate in the finished component.
Segmented frame technology, such as the proprietary process at the Boyd Corporation, is a high precision reel-to-reel manufacturing principle. Production lines utilize this concept to eliminate waste and optimize the value of stock materials. Waste is eliminated by orienting release liners, bonding tapes, optical films, and optically clear adhesives in such a manner that material utilization is optimized, driving down operational costs.
Problematic foreign object debris (FOD) gives rise to costly defects that affect production yield rates and product performance. Rotary die-cutting production lines must be housed in class 100 to class 100K cleanroom facilities for many industries. This allows for the manufacture of highly sensitive, contaminant, and particulate-free multi-functional display bonding solutions.
You May Also Like: AR Goggles for Swimmers
Segmented frame technology and cleanroom facilities are complemented by a suite of advanced in-line inspection equipment and engineering controls. Heightened connectivity allows for real-time web adjustments. They respond and react to misalignments that would otherwise waterfall into lost productivity and lower yield rates.
Contact Boyd and learn how they can assist with advantage by co-developing and fabricating a custom integrated display gasket solution that addresses budget and design requirements.
Magnus Tedestedt is vice president of engineered materials at Boyd Corporation.
High bond tapes address the demands of a wide range of bezel bonding and display gasket applications. These high-strength, double-sided acrylic foam tapes are formulated to achieve application-specific characteristics. Still, they can also carry complications along to the converting process due to die-cut dimensions and narrow bond lines. Softer tapes can be challenging for rotary die-cutting processes. To obtain a die-cut integrated display gasket solution that adheres to required tolerances, original equipment manufacturers require a solutions provider with advanced converting capabilities.
High Bond Tapes for Bezel Bonding and Display Gaskets
High-strength, double-sided acrylic foam bond tapes are high-performance adhesives, and each tape is formulated to achieve a balance of properties that address specific performance requirements.
For example:
- Edge-to-edge display technologies have ultra-thin bond lines and require tapes with excellent peel strength, impact resistance, and energy absorption
- Larger displays require bonding tapes that are resistant to creep with greater shear strength
- Automotive displays require durable bonds that resist vibration fatigue and impact stress
- Industrial or agricultural interfaces often require water-tight seals and durability enhancements
Applied stress is distributed evenly across the entire bond area, limiting the amount of force that gets exerted on display components. This acts to protect the electronic display. The closed-cell foam structure seals out contaminants, moisture, and solvents. These tapes are available with highly conformable and firm adhesive foam cores, acrylic and modified acrylic adhesives, and serval different release liners in a rand of thickness and colors.
An example of high-performance bond tape is the 3M™ VHB™ Tape 59xx Series that encompasses a wide range of high-performance bonding tapes that work with most bezel bonding and display gasket applications. These tapes are available in a thickness range from 150 µm to 1.6 mm. They are supplied with a modified acrylic adhesive on both sides of a very conformable adhesive foam core, providing good adhesion to the widest range of substrates, including most powder-coated paints and many plastics. These are the go-to tapes for most electronic display bonding applications.
Learn More: Advanced Thermal Interface Materials for Electronic Assemblies
How to Select the Appropriate Bond Tape
Designed for longevity, very high bond tapes are selected based on design criteria, including display size, weight, bond width, the position of the display, and thickness. Proper selection of materials ensures a durable, long-lasting bond.
Thickness
Tape thickness is selected based on the size and rigidity of the bonded substrates and their flatness. Thicker tapes provide an improved bond strength when mating irregular and larger surfaces. Rigid substrates with normal flatness are best handled by a tape thickness of 1.1 mm or greater, while flexible and flatter surfaces are most suitable for thinner tapes.
Tape Usage Requirements
The durability of the bond tape is a function of design proportions. Due to their viscoelastic nature, care should be taken to specify an adequate amount of tape for bonding applications. To best avoid creep and premature failure, 4x2 inch pieces of tape should be used for every 1 lb. of weight supported under static loads.
Core Firmness
As a rule of thumb, firm core tapes are most suitable for addressing flat substrates, while larger and curved displays are best suited for softer conformable core tapes. The softer conformable adhesive cores also provide enhanced impact resistance and have become the go-to products for most mobile electronics applications.
Recommended for You: Adding Textures to Touchscreens
Integrated Display Gaskets and Bezel Bonding Solutions
Many display technologies and other engineered materials require integration into multi-functional stack-ups. They use advanced converting and manufacturing capabilities for one-shot multi-functional components, including integrated display gaskets and bezel bonding solutions, where local secondary applications are optimized by including in the original design. During this process, pull close proximity die cuts into the bezel solution for a one-pass, multi-layered, multi-solution deliverable, such as a microphone or speaker gaskets, display ring tape, spacers, and dampers. These multi-functional components are produced in a cleanroom environment and assembled via segmented frame technology, capabilities that enable contaminant and particulate-free, ultra-tight tolerance die-cut components at the lowest cost possible.
Optically Clear Adhesives & Bezel Bonding
Optically Clear Adhesives (OCAs) are highly transparent adhesives used to bond visually clear components into an optically clear lamination without bubbles or distortion. OCAs laminate transparent materials and layers together, enabling complex optically clear assemblies to transmit as much light as possible through optimal refraction and refractive index matching. Optimizing the refractive index of laminated display components improves contrast ratio and optical clarity while reducing reflected light. This enhances the viewability, vivacity, clarity, and readability of LCD, LED, and OLED screens. OCAs create a differentiated automotive display experience with improved safety.
These adhesives are used specifically for their superior optical and mechanical attachment qualities. Optically Clear Adhesives have high dimensional stability, low shrinkage, and resist whitening over time. Integrating layers with the right OCAs enable rugged, long-lasting bonds in complex optically clear laminations. OCAs come in various formulations to accommodate a broad array of applications but are typically composed of acrylic, polyvinyl acetate (PVA), polyurethane (PU), silicone, or epoxy. The optical transparency of OCAs and application directly between the display and the user’s field of vision mean that they must be coated, handled, and fabricated with zero defects or visual flaws. It’s recommended to handle, fabricate, and assemble OCAs in high cleanliness environments certified to Class 100.
OCAs also offer ingress protection and reduce the width required for bezels to maximize screen space, better waterproof the display, protect it against contaminants, and create a more immersive display experience. OCAs are often utilized with bezel bonding techniques and integrated display gaskets for high performance, ultra-tight tolerance, streamlined touch display mounts.
Optically Clear Adhesives Conversion
Display technologies utilize sheet-type optically clear adhesives (OCA) when bonding visually clear components, such as touch screens, graphic overlays, and polymeric film glass laminates. Sheet-type OCA addresses inherent limitations that can affect screen brightness, contrast ratio, and the durability of these die-cut integrated display gasket solutions.
Sheet-type OCA is a superior alternative to optically clear resins (OCR) or liquid OCA (LOCA). Liquid adhesives are applied in a fishbone pattern prior to lamination and a UV curing process. These adhesives are prone to leakage, and users may experience uneven curing defects that can affect product quality and yield rates.
Light transmittance also decays as incremental materials are stacked upon each other. To eliminate any amount of light reflection or refraction, apply an adhesive of uniform thickness with a refractive index closely matched to mating components between each medium.
The integrated die-cut components are assembled with a sheet-type OCA with a refractive index between 1.4 and 1.5, close to that of display films, filters, or even touch panels. OCAs are dimensionally stable, exhibit low shrinkage, resist whitening and reduce any amount of reflection between each substrate in the finished component.
Segmented frame technology
Segmented frame technology, such as the proprietary process at the Boyd Corporation, is a high precision reel-to-reel manufacturing principle. Production lines utilize this concept to eliminate waste and optimize the value of stock materials. Waste is eliminated by orienting release liners, bonding tapes, optical films, and optically clear adhesives in such a manner that material utilization is optimized, driving down operational costs.
Cleanroom Capabilities
Problematic foreign object debris (FOD) gives rise to costly defects that affect production yield rates and product performance. Rotary die-cutting production lines must be housed in class 100 to class 100K cleanroom facilities for many industries. This allows for the manufacture of highly sensitive, contaminant, and particulate-free multi-functional display bonding solutions.
You May Also Like: AR Goggles for Swimmers
Inspection Equipment and In-Process Quality Checks
Segmented frame technology and cleanroom facilities are complemented by a suite of advanced in-line inspection equipment and engineering controls. Heightened connectivity allows for real-time web adjustments. They respond and react to misalignments that would otherwise waterfall into lost productivity and lower yield rates.
Contact Boyd and learn how they can assist with advantage by co-developing and fabricating a custom integrated display gasket solution that addresses budget and design requirements.
Magnus Tedestedt is vice president of engineered materials at Boyd Corporation.