5 Popular Applications for Design for Additive Manufacturing
5 Popular Applications for Design for Additive Manufacturing
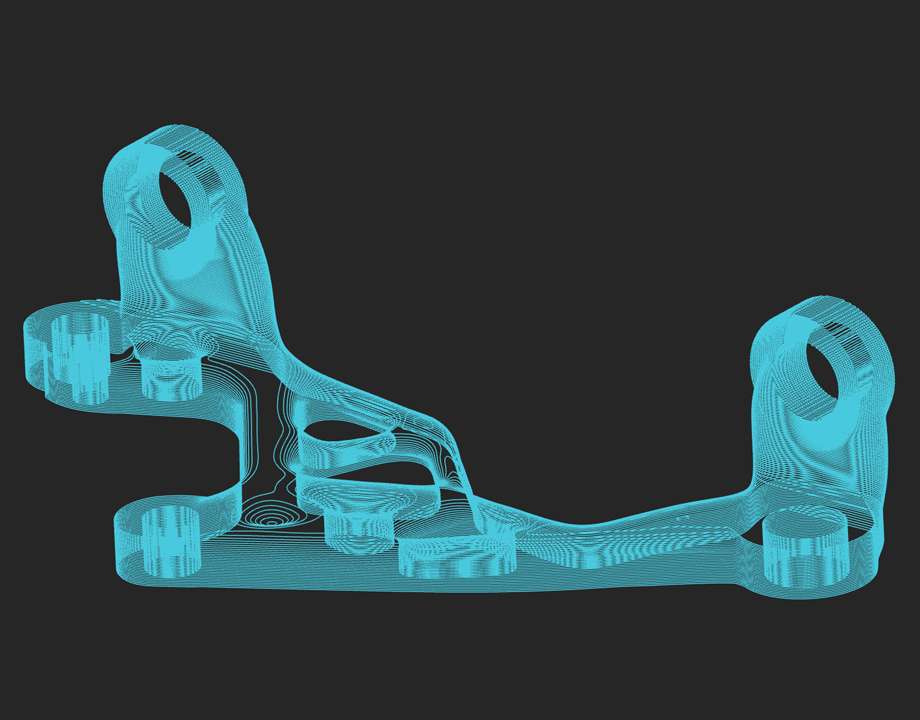
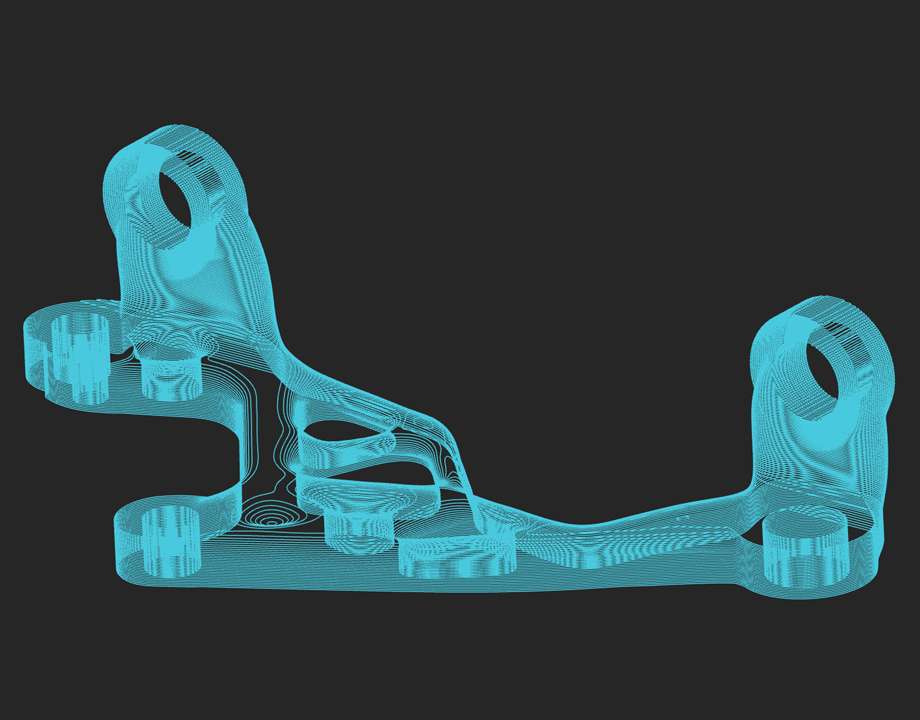
Design for additive manufacturing has many advantages in dealing with complex parts, but engineers must pay attention to nuances to make the case for 3D printing.
DfAM empowers engineers to create more intricate products while reducing weight and material consumption, maximizing efficiency, and reducing production costs. According to a recent Jabil survey, nearly two-thirds of 3D-printing stakeholders interviewed said AM had already changed the way they approach design in working with parts and products that are more complex, have innovative internal structures and channels, complex geometric shapes, or multi-material designs.
Although the basics of DfAM are easy to understand, becoming an expert can be challenging, especially as the capabilities of additive technologies, including the engineering design software, continue to advance rapidly.
The first goal of DfAM is to address the fundamental manufacturing question: Can it be printed with AM?
“Engineers often think 3D printing is easy and inexpensive because desktop polymer 3D printing is so readily available to them now for projects,” said Tim Simpson, a professor of engineering design and manufacturing engineering at Penn State and co-director of Pennsylvania State University’s Center for Innovative Materials Processing through Direct Digital Deposition. “As a result, they tend to think everything can/should be 3D printed, when this is far from the reality. Just because you can 3D print a part doesn’t mean that you should.”
here are some popular applications for DfAM.
1. Minimum material consumption
The DfAM process can determine the least amount of material that is required to meet the intended end-use specifications. Obvious benefits include less material used, less material wasted, lighter product weight, and reduced costs. Tools such as topology optimization and lattice structures make products that are lighter, stronger, and more flexible.
2. Lightweighting
“Most DfAM software tools optimize a part by making it as lightweight as possible,” said Simpson. Not only does lightweighting reduce material costs, it also improves part function and longevity and eases ergonomic fatigue in setting such as medicine, where a surgeon uses a lighter-weight instrument.
3. Part consolidation
Converting an assembly of many parts into a single customized part means that the entire part is printed in a few steps, greatly reducing assembly time and related costs. Part consolidation also reduces the number of potential failure points a product has, making it longer-lasting. For example, General Electric Aviation replaced 900 parts with 16 parts in building a helicopter engine using AM methods.
4. Improved function
DfAM adds value by making designs more efficient and functional. For example, a cooling channel that is traditionally designed as a straight line for injection molding can instead be curved using AM to better fit the shape of the end part to provide faster cooling. “DfAM is as much about adding value to the part as it is about saving costs to make AM a viable production method for the part in consideration,” said Simpson.
5. Optimized materials
DfAM can determine the best material to use for achieving the intended performance specifications. New AM materials continue to be released into the marketplace that have highly-specific chemical and physical properties. These materials may be difficult or impossible to machine with traditional methods and can be quickly tested with AM through rapid prototyping.
Become a Member: How to Join ASME
An understanding of DfAM software tools is essential for becoming proficient with DfAM. The two most popular types of DfAM software tools are “generative design” and “topology optimization.” These DfAM capabilities are readily available from software companies such as Autodesk (Fusion 360), Altair (Inspire), and nTopology.
“SolidWorks, NX, and Creo are also adding DfAM tools to their software offerings,” said Simpson.
These software programs can help engineers create iterations for prototyping, simulate stresses, generate support structures, and optimize a component by reducing the required amount of material while maximizing strength and performance.
Simpson observed that DfAM can be a double-edged sword: For example, creating the lightest weight possible often comes at the greatest expense.
Editor’s Pick: 3D Printing at the Nanoscale
“MEs need to become adept at thinking about not only the geometry they are designing, but also the orientation in which a part will be built,” he said. “This is often where the business case for AM is lost and it is hard for MEs to grasp all the nuances of this on their own. As such, they need to be comfortable working in a team and communicating across multiple disciplines for AM to be successful.”
Simpson teaches the ASME course Design for Additive Manufacturing with Metals. The course provides the foundational knowledge to properly evaluate AM as a viable technology solution. Simpson discusses the in-depth technical knowledge necessary to take an AM product from design through post-processing and into the market using three use cases: replication, adaptation, and optimization.
Being at the cutting edge of AM technology, Simpson continuously updates his course to reflect the advancing capabilities of generative design and other AI-assistive design tools.
“The ability to quickly customize a component or tailor a part for a specific patient, product, or application will get easier and easier,” said Simpson. “As this happens, the role of MEs will shift from doing the CAD and 3D modeling work to formulating the problem—for example, load cases, constraints, bounding volume, and mating interfaces—that is then solved by AI to generate the geometry. This is the biggest shift that will happen in the next few years and change how MEs learn about design and think about engineering structures.”
Mark Crawford is a science and technology writer in Corrales, N.M.
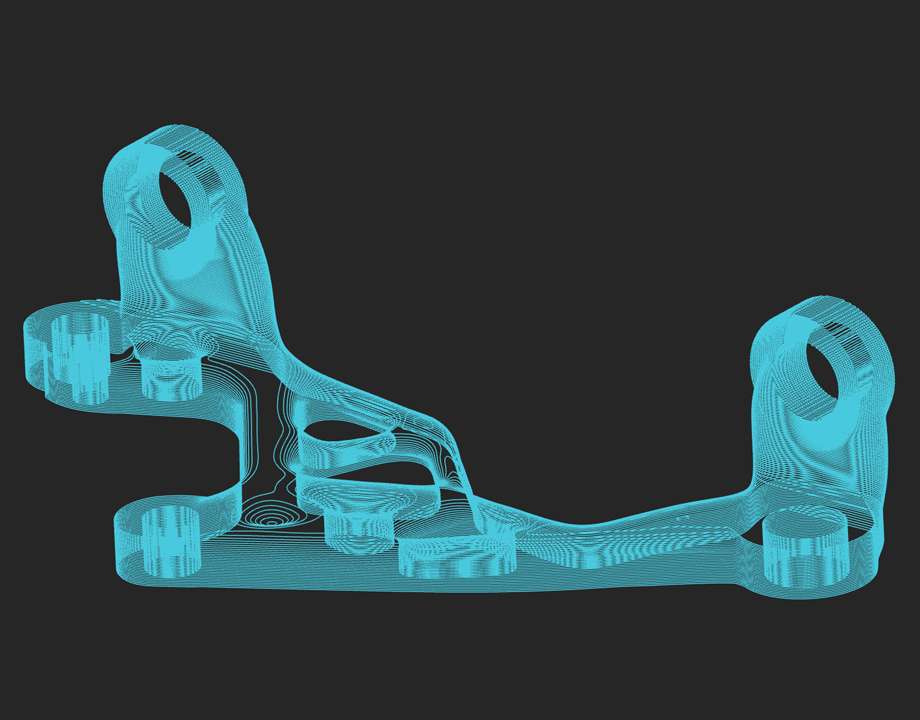
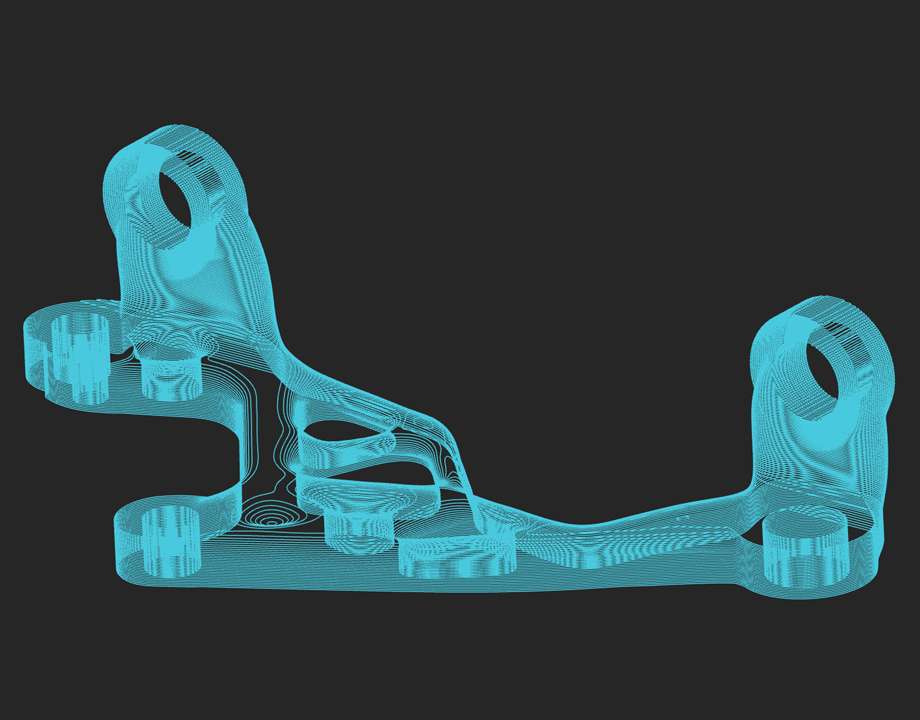