Eight Applications To Keep Every Engineer Running Lean
Eight Applications To Keep Every Engineer Running Lean
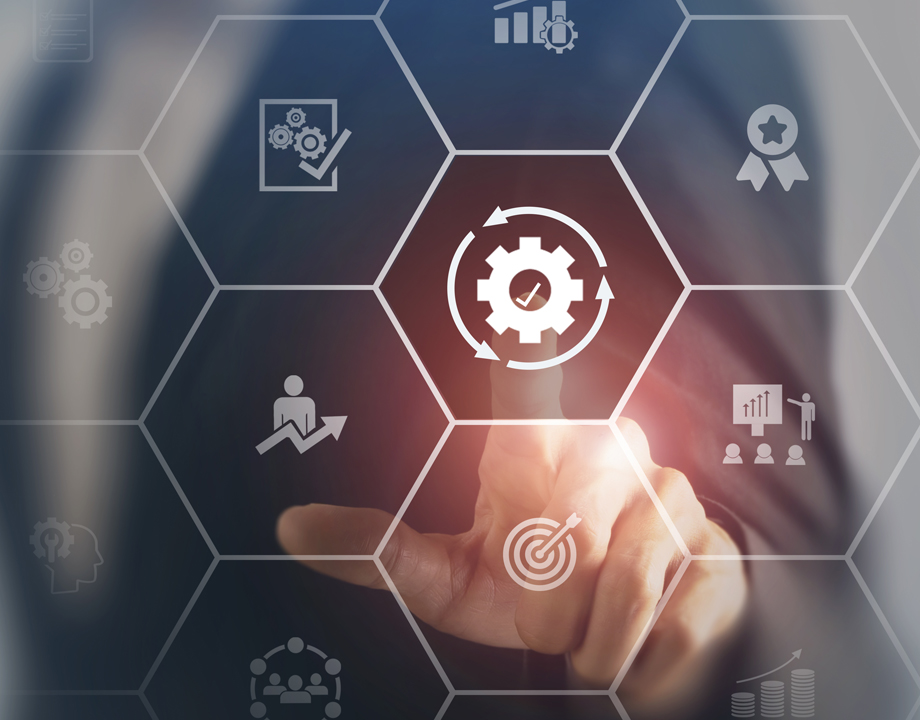
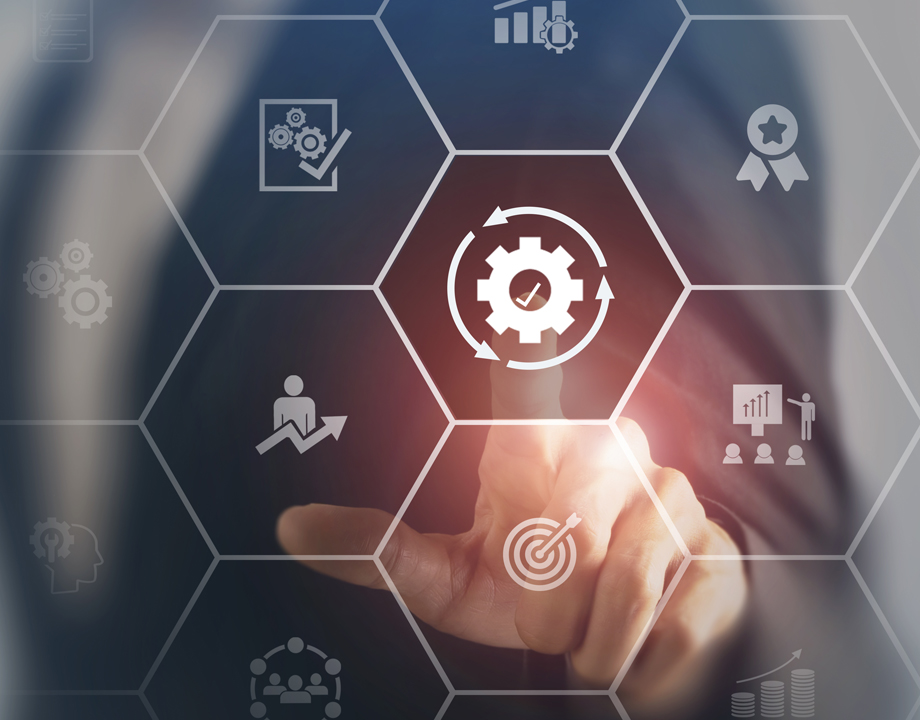
Lean principles are a straightforward, common-sense approach for improving manufacturing operations within any production process. Here are eight essential ones engineers should always embrace.
Lean manufacturing was originally created by Toyota to eliminate waste and inefficiency in its manufacturing operations. Lean is a straightforward, common-sense approach for improving manufacturing operations that can be applied to any production process.
The goal of lean is to eliminate waste—the non-value-added components in any process. Unless a process has gone through lean many times, it contains some element of waste—overproduction, excess inventory, poor workflow, repeated steps, product defects, overprocessing, unused employee potential, and production delays, for example.
The Ultimate Lean Principle: How to Join ASME
A lean organization focuses on continuous improvement to reduce waste, add value to the final product, and pass these cost and time savings on to the customer, creating long-term relationships based on a culture of high quality, continuous improvement, and worker pride.
Below are eight lean principles that are essential for every engineer to understand and practice in the manufacturing environment:
Cellular manufacturing creates the optimal arrangement of machines and equipment to maximize the efficiency of production. The smaller footprint streamlines workflow and helps teams work together more efficiently, reducing cycle time and freeing up inventory space. Machines can be added or removed as needed to adjust for production volume. Cellular manufacturing creates a production layout that is only as large as it needs to be, helping to reduce cycle time and inventory.
Takt time is about maintaining a steady pace of production, say, manufacturing one part every 60 seconds, for example. It is calculated as planned production time/customer demand and reflects the average time between the start of making one part and the start of production of the next part. The production process is monitored to maintain this optimum pace of production, the production team making adjustments as needed in real time to bring variances back into control.
More Like This: Seven Ways IoT Super-charges Lean Manufacturing
Sharing elements of takt time and standardized work, continuous flow makes sure that each step in the production process occurs when it should, with no delays upstream or downstream that would create a slowdown or stoppage. Continuous flow does its best to remove all delays and mistakes, striving for uninterrupted flow throughout the process and maintaining takt time. The goal is also to maintain the right amount of work-in-process as too much work-in-process creates delays and reduces productivity.
Poka-Yoke is the process of error proofing a manufacturing process. Methods are created that inspect production processes with the goal of achieving zero defects. This can include inline and offline inspection processes, often with high-resolution optical equipment and measuring machines. Poka-Yoke mitigation strategies include prevention, detection (preferably in real time), and automatic correction.
Career-related Article: Who Are the Engineers of the Future?
Kaizen is the process of helping employees work together proactively to achieve steady improvements in the manufacturing process. It acknowledges that they know the ups and downs of their equipment and processes the most and will know how to eliminate waste from those processes that managers do not see. Kaizen emphasizes improving processes through small, incremental changes, which carries over to creating a corporate culture of continuous improvement.
Productivity inefficiencies and delays are usually attributed to six major loss categories: unplanned stops, planned stops, small stops, slow cycles, production defects, and start-up defects. These production weaknesses are ideal places to start lean initiatives. Managers can create team strategies to gradually, but steadily, resolve these issues, improving operational efficiency, speed of production, and product quality.
Continue the Read: 6 Lean Principles for an Industry 4.0 World
When done correctly, lean can create huge improvements in efficiency, cycle time, productivity, material costs, and scrap, leading to lower costs and improved competitiveness. When lean is enabled by the speed and accuracy of the Internet of Things, lean goals are much easier and faster to attain. As artificial intelligence and machine-to-machine communications continue to advance—especially the ability to self-correct in real time—lean objectives will be achieved much more quickly, with less human intervention.
Mark Crawford is technology writer based in Corrales, N.M.
The goal of lean is to eliminate waste—the non-value-added components in any process. Unless a process has gone through lean many times, it contains some element of waste—overproduction, excess inventory, poor workflow, repeated steps, product defects, overprocessing, unused employee potential, and production delays, for example.
The Ultimate Lean Principle: How to Join ASME
A lean organization focuses on continuous improvement to reduce waste, add value to the final product, and pass these cost and time savings on to the customer, creating long-term relationships based on a culture of high quality, continuous improvement, and worker pride.
Below are eight lean principles that are essential for every engineer to understand and practice in the manufacturing environment:
1. Cellular manufacturing
Cellular manufacturing creates the optimal arrangement of machines and equipment to maximize the efficiency of production. The smaller footprint streamlines workflow and helps teams work together more efficiently, reducing cycle time and freeing up inventory space. Machines can be added or removed as needed to adjust for production volume. Cellular manufacturing creates a production layout that is only as large as it needs to be, helping to reduce cycle time and inventory.
2. Takt time
Takt time is about maintaining a steady pace of production, say, manufacturing one part every 60 seconds, for example. It is calculated as planned production time/customer demand and reflects the average time between the start of making one part and the start of production of the next part. The production process is monitored to maintain this optimum pace of production, the production team making adjustments as needed in real time to bring variances back into control. More Like This: Seven Ways IoT Super-charges Lean Manufacturing
3. Standardized work
When any work process is standardized, it is easier to monitor, maintain, and control. The greater the number of processes that are standardized with each other, the better the efficiency and communication. Methods, best practices, materials, tools, processes, and tasks can all be standardized to create an environment of innovation and efficiency, eliminating redundant actions or behaviors and simplifying forecasting and inventory management.
4. Continuous flow
Sharing elements of takt time and standardized work, continuous flow makes sure that each step in the production process occurs when it should, with no delays upstream or downstream that would create a slowdown or stoppage. Continuous flow does its best to remove all delays and mistakes, striving for uninterrupted flow throughout the process and maintaining takt time. The goal is also to maintain the right amount of work-in-process as too much work-in-process creates delays and reduces productivity.
5. Poka-Yoke
Poka-Yoke is the process of error proofing a manufacturing process. Methods are created that inspect production processes with the goal of achieving zero defects. This can include inline and offline inspection processes, often with high-resolution optical equipment and measuring machines. Poka-Yoke mitigation strategies include prevention, detection (preferably in real time), and automatic correction.Career-related Article: Who Are the Engineers of the Future?
6. Value stream mapping
One of the most basic lean tools, value stream mapping maps out all the steps and inputs that go into a production process This value stream is then analyzed to identify and remove any forms of waste that will add value and efficiency to the process and the final product. The entire life cycle of a product can be evaluated with value stream mapping, from raw material inputs to administration and waste disposal.
7. Kaizen
Kaizen is the process of helping employees work together proactively to achieve steady improvements in the manufacturing process. It acknowledges that they know the ups and downs of their equipment and processes the most and will know how to eliminate waste from those processes that managers do not see. Kaizen emphasizes improving processes through small, incremental changes, which carries over to creating a corporate culture of continuous improvement.
8. Six big losses
Productivity inefficiencies and delays are usually attributed to six major loss categories: unplanned stops, planned stops, small stops, slow cycles, production defects, and start-up defects. These production weaknesses are ideal places to start lean initiatives. Managers can create team strategies to gradually, but steadily, resolve these issues, improving operational efficiency, speed of production, and product quality. Continue the Read: 6 Lean Principles for an Industry 4.0 World
When done correctly, lean can create huge improvements in efficiency, cycle time, productivity, material costs, and scrap, leading to lower costs and improved competitiveness. When lean is enabled by the speed and accuracy of the Internet of Things, lean goals are much easier and faster to attain. As artificial intelligence and machine-to-machine communications continue to advance—especially the ability to self-correct in real time—lean objectives will be achieved much more quickly, with less human intervention.
Mark Crawford is technology writer based in Corrales, N.M.
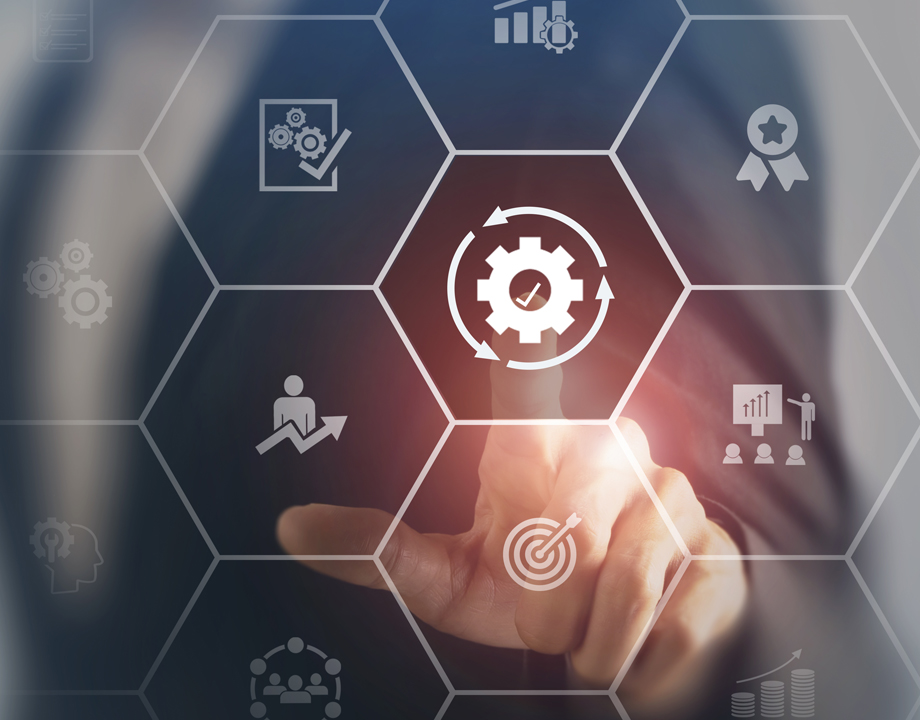
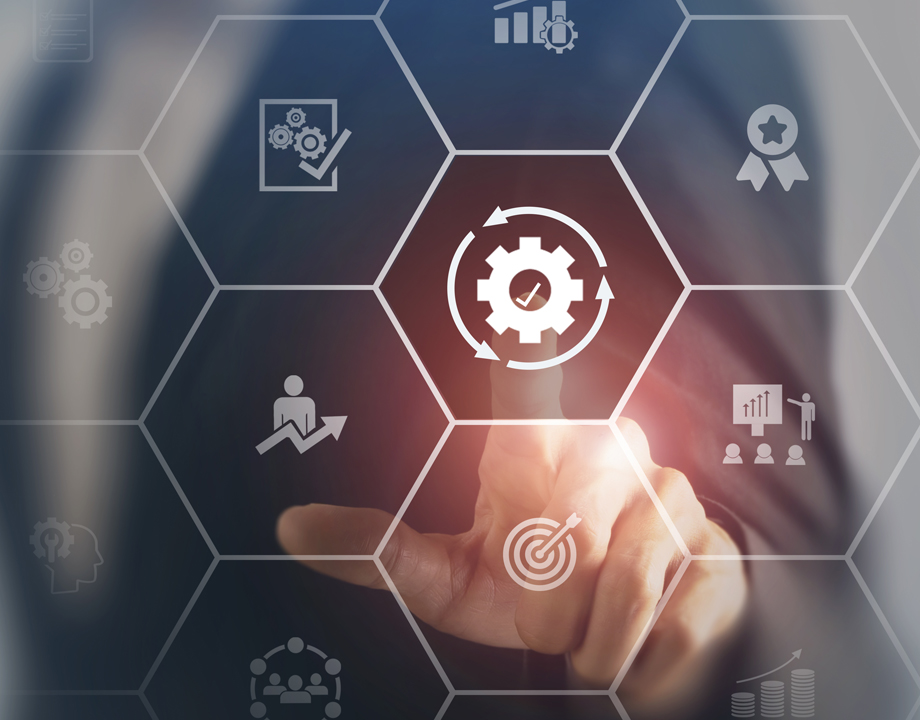