3D-Printed Heat Shield Proves Itself to Student Engineers
3D-Printed Heat Shield Proves Itself to Student Engineers
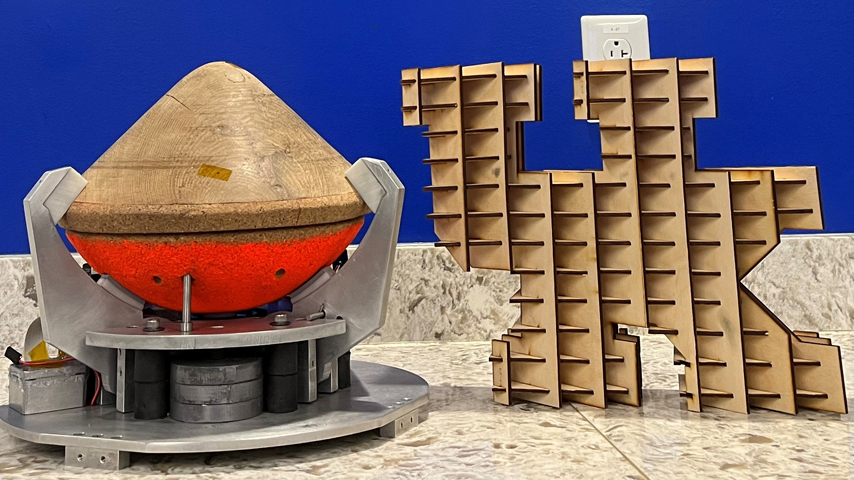
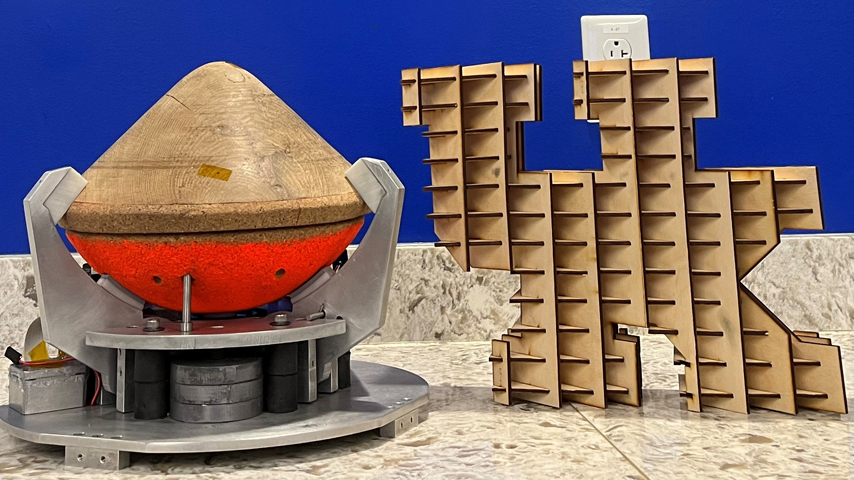
Space capsule designed by University of Kentucky engineering students tested thermal heat protection.
Thanks in part to 3D-printed plastic, and perhaps bubbles and gyroids, a project to collect re-entry data from space capsules has become a key figure in the thermal protection industry.
University of Kentucky and NASA first saw success in December 2021 with its joint project that saw several firsts: a university-built entry capsule successfully entering a planetary atmosphere from space; a university flying a hypersonic vehicle; and a 3D-printed heat shield flying on an entry mission. That success—to continue with a second mission slated for this year—turned the project into an eagerly sought opportunity for companies to test other materials meant to cover and shield objects coming back from space.
"It’s a really inexpensive way to test heat shields. Not only that, we can accommodate multiple tests,” said Kirsten Ford, a UK postgrad student who took over as project lead in 2022 and, during an interview earlier this year, was about to begin a new full time job at NASA after completing her master’s degree. The capsule missions have “become valuable not just to us, but to the thermal protection industry at large,” she said.
To understand how that happened it’s important to get a primer on the Kentucky Re-Entry Universal Payload System [KRUPS] program and its capsules, and the Kentucky Re-Entry Probe Experiment [KREPE] missions using those capsules.
The UK team began building three capsules in summer 2020. Two were covered in space shuttle orbiter tiles for reentry, and the third had a 3D-printed thermal projective shield, developed by Oak Ridge National Lab, NASA Johnson Space Center and NASA Ames Research Center. In December 2021, the capsules were strapped to the Cygnus resupply vehicle and sent to the International Space Station. On reentry, the Cygnus, filled with trash from the ISS, burned up, but the capsules were ejected and landed in the ocean near New Zealand.
Between ejection and landing, the capsules transmitted data to the Iridium satellite network, which relayed the information back to the ground. The team was interested in measuring heat flux, and have made new additions like a spectrometer system and pressure ports.
Become a Member: How to Join ASME
"When we add something new we learn something new about the re-entry environment,” Ford said. Though this was the initial purpose of the program, the focus expanded during the KREPE-1 mission from collecting reentry data to validating new thermal protection systems, she said.
"It’s a really inexpensive way to test heat shields. Not only that, we can accommodate multiple tests,” Ford said. The missions also are unmanned, making them a safe way to conduct these tests.
Ford wasn’t able to share details of new heat shields that will be tested in the upcoming KREPE-2 mission, which will use five capsules this time. But the team relied on Protolabs, which was tapped to create 3D-printed shielding for the new capsules.
Its mineral-filled nylon is integral for a few reasons. First, plastic is a better material to encase electronics within a capsule, since metal would act as a Faraday cage and prevent data transmission. Second, the capsule housing is of a very specific geometry, so something custom 3D-printed especially will fit more closely. Third is its high strength to weight ratio. Fourth, the material ablates, or chars, and that burned coating reacts with released gasses to add more thermal protection but doesn’t entirely disintegrate.
Eric Utley, Protolabs engineering manager, said the 3D-printed material has further benefits to the space industry. Overall, it allows for reduction of weight, greater combinations of assemblies, and fewer pieces to build a rocket. It also enables creation of bespoke parts.
More for You: Designing a Golden Eye for the Sky
"Aerospace is so low volume, you can make changes from rocket to rocket,” Utley said. “Not like a molding process where you make 500 and expect to use that for a year or two. So a client can really be flexible and adapt [their] designs.”
Shield material design gets down to a structural level, he noted, referring to the bubbles.
"Over the last few years, there’s been an uptick in more procedural designs, more designs that use lattice structures, or TPMS,” triply periodic minimal surfaces, or gyroids, similar to soap bubbles, he said. They make very lightweight structures and have a “very high strength to weight ratio.”
Gyroids are important to heat shield materials. “It fills up the space of a cube but is kind of like a LEGO in that the opposite spaces match,” Utley said. They can be put together in 3D “like a bathroom tile. It has a lot of surface area, so is used in heat exchangers, and it’s pretty isotropic, meaning it’s equally strong” in any direction.
Before KRUPS, Protolabs had built rocketry for other academic clients like University of California at Berkeley, Utley said. Perhaps ironically, other companies in the field may benefit from the firm’s expertise.
"We’ve had more interest from people testing heat shields than we could accommodate. I see this project continuing to grow and expand,” Ford said.
Eydie Cubarrubia is an independent writer in New York City.
University of Kentucky and NASA first saw success in December 2021 with its joint project that saw several firsts: a university-built entry capsule successfully entering a planetary atmosphere from space; a university flying a hypersonic vehicle; and a 3D-printed heat shield flying on an entry mission. That success—to continue with a second mission slated for this year—turned the project into an eagerly sought opportunity for companies to test other materials meant to cover and shield objects coming back from space.
"It’s a really inexpensive way to test heat shields. Not only that, we can accommodate multiple tests,” said Kirsten Ford, a UK postgrad student who took over as project lead in 2022 and, during an interview earlier this year, was about to begin a new full time job at NASA after completing her master’s degree. The capsule missions have “become valuable not just to us, but to the thermal protection industry at large,” she said.
To understand how that happened it’s important to get a primer on the Kentucky Re-Entry Universal Payload System [KRUPS] program and its capsules, and the Kentucky Re-Entry Probe Experiment [KREPE] missions using those capsules.
The UK team began building three capsules in summer 2020. Two were covered in space shuttle orbiter tiles for reentry, and the third had a 3D-printed thermal projective shield, developed by Oak Ridge National Lab, NASA Johnson Space Center and NASA Ames Research Center. In December 2021, the capsules were strapped to the Cygnus resupply vehicle and sent to the International Space Station. On reentry, the Cygnus, filled with trash from the ISS, burned up, but the capsules were ejected and landed in the ocean near New Zealand.
Between ejection and landing, the capsules transmitted data to the Iridium satellite network, which relayed the information back to the ground. The team was interested in measuring heat flux, and have made new additions like a spectrometer system and pressure ports.
Become a Member: How to Join ASME
"When we add something new we learn something new about the re-entry environment,” Ford said. Though this was the initial purpose of the program, the focus expanded during the KREPE-1 mission from collecting reentry data to validating new thermal protection systems, she said.
"It’s a really inexpensive way to test heat shields. Not only that, we can accommodate multiple tests,” Ford said. The missions also are unmanned, making them a safe way to conduct these tests.
Ford wasn’t able to share details of new heat shields that will be tested in the upcoming KREPE-2 mission, which will use five capsules this time. But the team relied on Protolabs, which was tapped to create 3D-printed shielding for the new capsules.
Its mineral-filled nylon is integral for a few reasons. First, plastic is a better material to encase electronics within a capsule, since metal would act as a Faraday cage and prevent data transmission. Second, the capsule housing is of a very specific geometry, so something custom 3D-printed especially will fit more closely. Third is its high strength to weight ratio. Fourth, the material ablates, or chars, and that burned coating reacts with released gasses to add more thermal protection but doesn’t entirely disintegrate.
Eric Utley, Protolabs engineering manager, said the 3D-printed material has further benefits to the space industry. Overall, it allows for reduction of weight, greater combinations of assemblies, and fewer pieces to build a rocket. It also enables creation of bespoke parts.
More for You: Designing a Golden Eye for the Sky
"Aerospace is so low volume, you can make changes from rocket to rocket,” Utley said. “Not like a molding process where you make 500 and expect to use that for a year or two. So a client can really be flexible and adapt [their] designs.”
Shield material design gets down to a structural level, he noted, referring to the bubbles.
"Over the last few years, there’s been an uptick in more procedural designs, more designs that use lattice structures, or TPMS,” triply periodic minimal surfaces, or gyroids, similar to soap bubbles, he said. They make very lightweight structures and have a “very high strength to weight ratio.”
Gyroids are important to heat shield materials. “It fills up the space of a cube but is kind of like a LEGO in that the opposite spaces match,” Utley said. They can be put together in 3D “like a bathroom tile. It has a lot of surface area, so is used in heat exchangers, and it’s pretty isotropic, meaning it’s equally strong” in any direction.
Before KRUPS, Protolabs had built rocketry for other academic clients like University of California at Berkeley, Utley said. Perhaps ironically, other companies in the field may benefit from the firm’s expertise.
"We’ve had more interest from people testing heat shields than we could accommodate. I see this project continuing to grow and expand,” Ford said.
Eydie Cubarrubia is an independent writer in New York City.
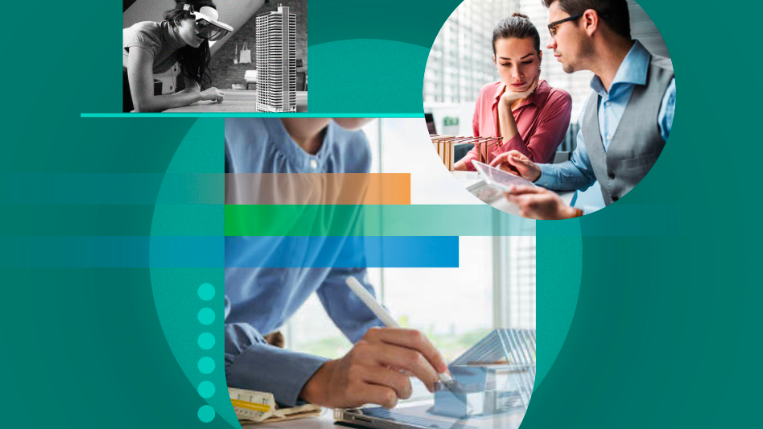
Pulse of the Profession: CAD in 2030
CAD technologies and their applications are rising in tandem with trends in Industry 4.0.
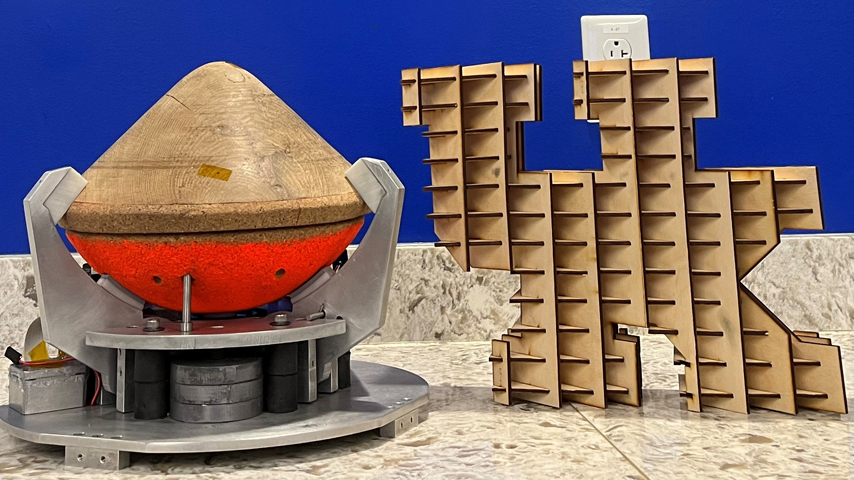
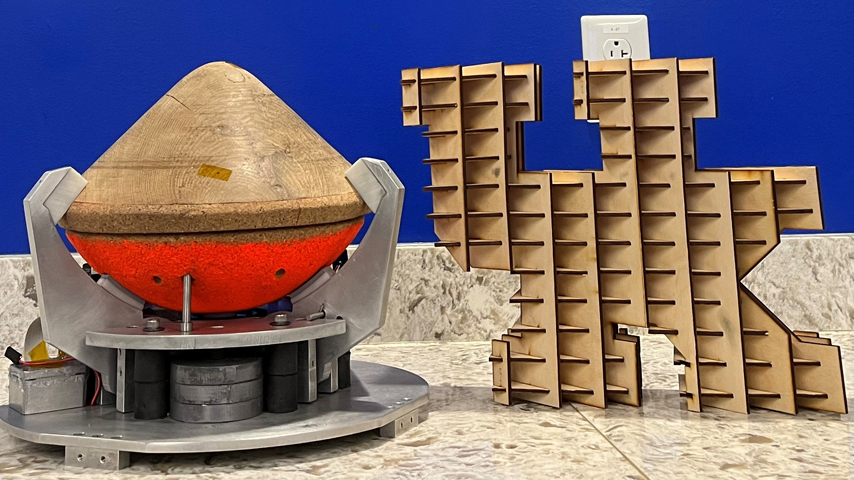